08/23/2019 - Oliver Hagenlocher - Press
Laser Cleaning Machine of EMAG LaserTec: LC 4-2 Laser Cleaning Machine for implementation in Manufacturing Lines or as a Standalone Machine
EMAG LaserTec is known first and foremost for highly productive laser welding systems. The focus is indeed on the word “system”: In addition to the actual welding process, steps that occur upstream or downstream of the welding are frequently integrated as well. Proper cleaning of the workpieces prior to welding is an important process step, as this determines the resulting quality. Impurities from upstream processes (such as coolants or residues of forming processes), as well as preservatives or surface treatments such as phosphatized coatings are “poison” for the welding process and have to be removed (without affecting the process reliability) in order to create high-quality welded joints. Currently, the commonly used and accepted method is a washing process, usually with water-based cleaning agents, in a so-called three-zone washing machine (the process steps are washing, rinsing and drying). However, this process is not desirable.
Images
An alternative is the so-called laser cleaning: This process makes use of laser ablation, in which the surface of the workpiece is “bombarded” with brief but powerful light pulses and the impurities thus removed from the surface.
Laser cleaning offers numerous advantages. Compared to customary industrial washing systems, laser beam cleaning is very energy- and space-efficient. The new LC 4-2 laser cleaning machine needs only 4.5 square meters of floor space. For the cleaning process, a highly efficient 200 W laser is used. It is switched on for only a few seconds per component. Cleaning systems frequently require a floor space of more than 20 square meters and consume energy permanently, to keep the washing solutions at the right temperature. Additionally, laser cleaning is practically maintenance-free, as no cleaning agents are consumed and no washing media has to be replaced.
Another big plus is the speed the technology offers. The entire cleaning process with the laser beam is fully automated, takes only a few seconds and can be integrated directly into the line cycle. Also, no sacrifices have to be made when it comes to quality, as all residues – both anorganic (e.g. oxides) and organic (e.g. grease) – are removed reliably.
Expertise in laser processing
“Developing laser cleaning machines is quite a challenge, as the requirements can differ vastly from component to component,” explains Nikolas Meyer, head of sales at EMAG LaserTec. “Experience is of key importance for providing effective production solutions with short development and delivery periods.” EMAG LaserTec has many years of experience in laser welding of powertrain components (e.g. gear wheels, differentials, clutch parts and also components for electromobility, such as rotor shafts) and in developing the corresponding systems. The ELC laser welding machines of EMAG form the heart of these systems. These machines provide a highly effective yet very flexible basis for numerous applications. “We have decades of experience when it comes to process development and system concepts. Our customers are increasingly making use of this and entrust us with the complete development and project management. In the end, they then receive turnkey systems that have been perfectly customized for the respective component and production site,” says Meyer. The laser experts from Heubach have now invested their experience in developing a new laser cleaning machine.
Laser cleaning: Application know-how is key
In the laser application laboratory of EMAG LaserTec GmbH, laser cleaning technology is studied intensely. To achieve optimal cleaning results, the process parameters need to be adapted. To this end, large-scale application trials and parameter studies are conducted and processing strategies are developed and tested. For example, the processing parameters differ depending on whether the lubricants are oil-based or water-based.
To make this technology easy to use, special software is required to free the users from getting bogged down in technical laser settings or optical parameters, thus allowing them to concentrate on the technology. The EMAG EC Clean achieves this goal. Together with the integrated SINUMERIK 840D sl, it forms the brain of the laser cleaning machine.
The lab in Heubach also provides the means for processing trials.
New LC 4-2 laser cleaning machine for components with a diameter of up to 200 mm
“Modularization” has been a buzzword in mechanical engineering for some years now: Customized system solutions are created using a “building block” system of modules. “Here at EMAG LaserTec, we are also constantly expanding our set of building blocks. We are particularly proud that we are now able to present our new LC 4-2 laser cleaning machine, which is on equal footing with the ELC laser welding machines when it comes to performance and flexibility, at the EMO in Hanover,” adds Nikolas Meyer (note: LC 4-2 stands for “Laser Cleaning”, size 4 with 2 workpiece holders). The 200 W laser beam source mentioned earlier is the heart of the LC 4-2. “Right from the start, our goal was to develop a system that can be used autonomously,” explains Meyer. “The users of the standalone machine also profit from our large service network, which is quite a significant benefit.” Whether as standalone solution or as laser cleaning system within the line cycle: In both cases, the integrated rotary indexing table enables easy, safe and process-reliable manual loading, or can just as easily be configured for automatic loading. The workpiece holders, which can be implemented as single or double holders, are equipped with rotary drives that handle the feed motion during the cleaning process. “The positioning of the cleaning lens in 3 axes (XZB) is another aspect where the user can choose whether it should be performed manually or be completely NC-operated. The latter is the obvious choice for use in the production line, for example when different components are welded on the same line. That guarantees absolute process reliability,” adds Nikolas Meyer.
The new LC 4-2 of EMAG clearly bears the signature of EMAG LaserTec. The system offers maximum cleaning performance even in tight spaces, without sacrificing user-friendliness. The integrated automation system guarantees easy handling and thus makes it an alternative to customary cleaning systems for a large range of customers.
The advantages at a glance
- Significantly reduced energy consumption compared to washing machines No liquids that have to be heated or later removed with a vacuum dryer.
- The workpieces stay dry. This is particularly important in the case of complex geometries, narrow gaps etc. that are hard to dry.
- The component cleaning is perfectly integrated into the flow of components and takes place directly upstream of the welding. There are no idle times or interruptions in the material flow, and no preheating times.
- Thanks to the compact design, the required floor space is significantly reduced.
- High process capability and constant results.
- Even problematic impurities, such as certain coolants used for minimal quantity lubrication (MQL), which are very difficult to wash off, are easily evaporated.
- Minimum maintenance required
Downloads
Contact
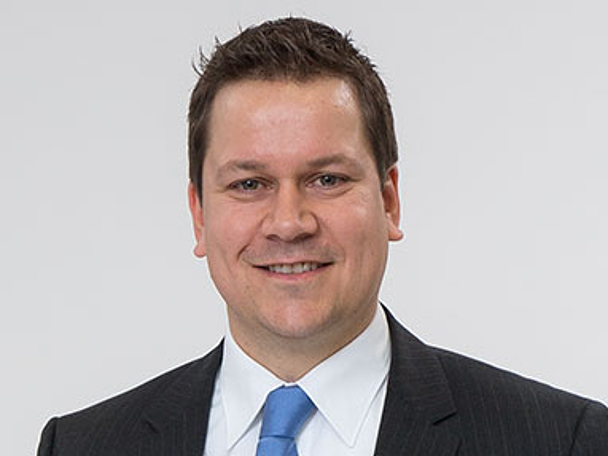
Oliver Hagenlocher
Area
Press and Communication