With EDNA from EMAG: Traceability every tenth of a second
Every recall of car models is associated with huge costs for manufacturers - even if only a small component is affected. On the other hand, the technical complexity of vehicles is increasing, which further increases the risk of errors. In this context, the traceability of production processes becomes more important than ever, which, of course, includes all companies in the supply chain. The aim is to achieve 100 percent traceability in order to uncover any weak points and prevent costly recalls.
EMAG uses its IoT technology EDNA to establish highly accurate and comprehensive traceability and to determine the energy consumption per component or layer.
Focus on comprehensive traceability
With EDNA, EMAG has a comprehensive IoT ecosystem for the digitalization of industrial production. The foundation for this is the so-called EDNA IoT Core - an industrial PC that is connected to the machine's control system and records all important production and sensor data with the help of the EDNA Cortex software, which in turn forms the basis for comprehensive traceability.
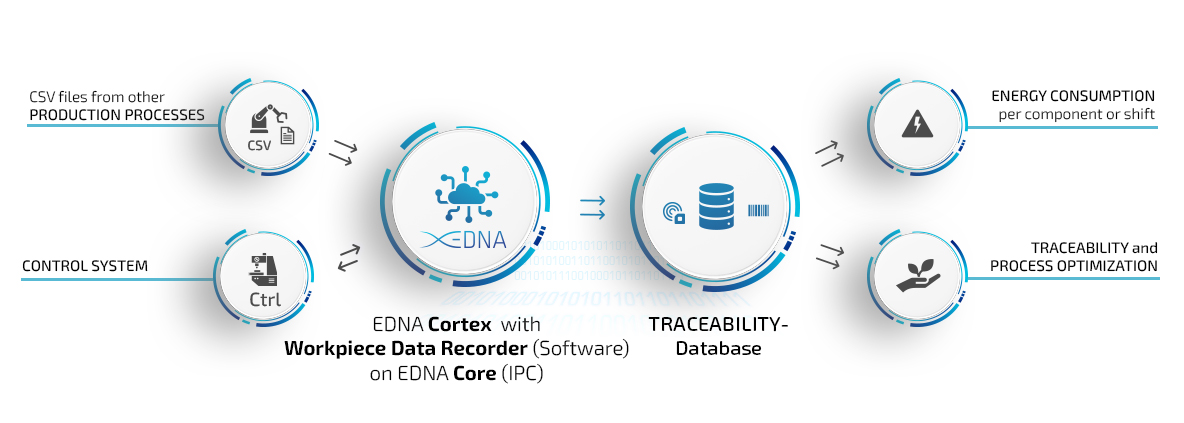
This is what the process looks like in detail:
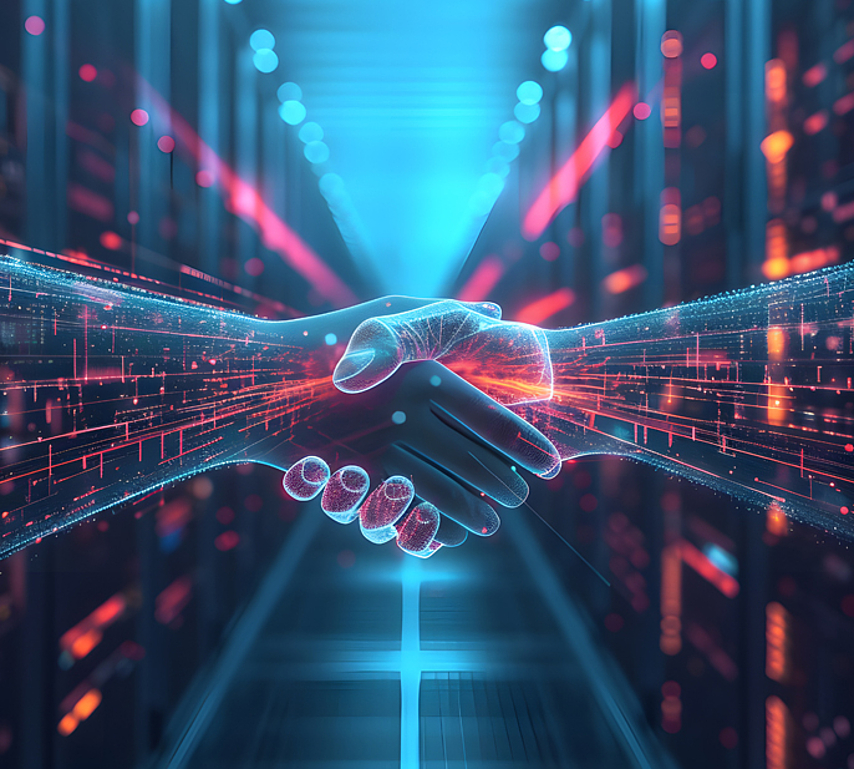
Handshake Procedure
The handshake procedure forms the basis. It stands for a secure connection between the machine controller and EDNA Cortex. With each handshake, new information is exchanged, stored and provided with metadata - including time stamp, machine type, workpiece ID number and type as well as the process values.
The handshakes can be repeated as often as required (even for the same component) at tenths of a second intervals, whereby values relating to the current sub-process are recorded in each case.
The software calculates average values per workpiece and shift. The results are then available as a CSV file for further processing within the company. Alternatively, it is of course also possible to read out all data/handshakes.
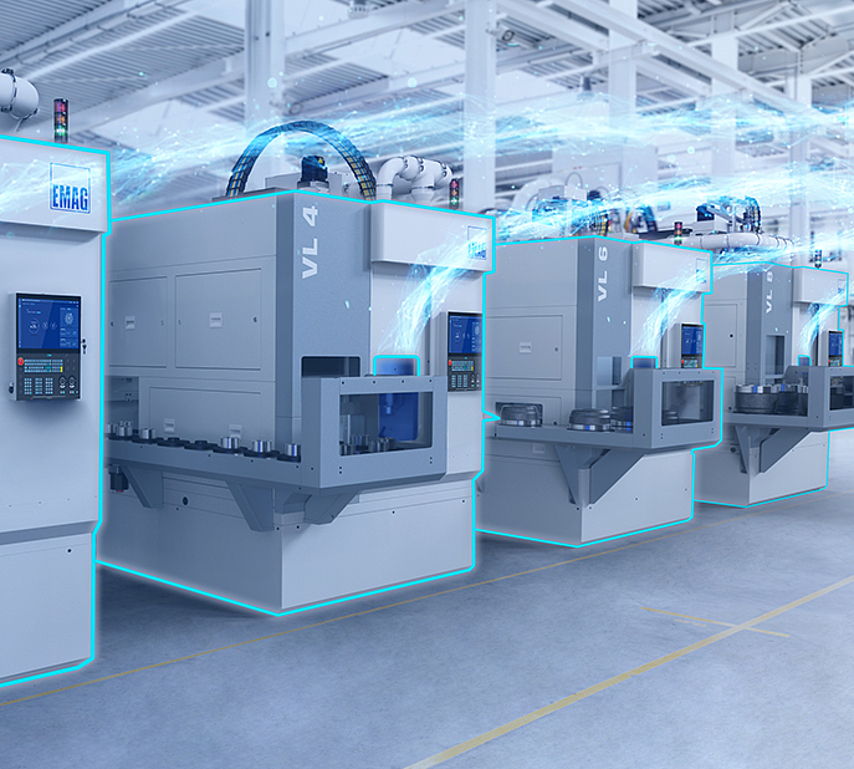
External sources are included
Information from external units (i.e. outside of NC/PLC machine controls) can also be merged. This includes sources such as OPC UA interfaces from robots and lasers or CSV files from downstream production processes.
Overall, this approach opens up far-reaching possibilities, as production planners can analyze each sub-process individually. This complete transparency opens the door to comprehensive optimization.
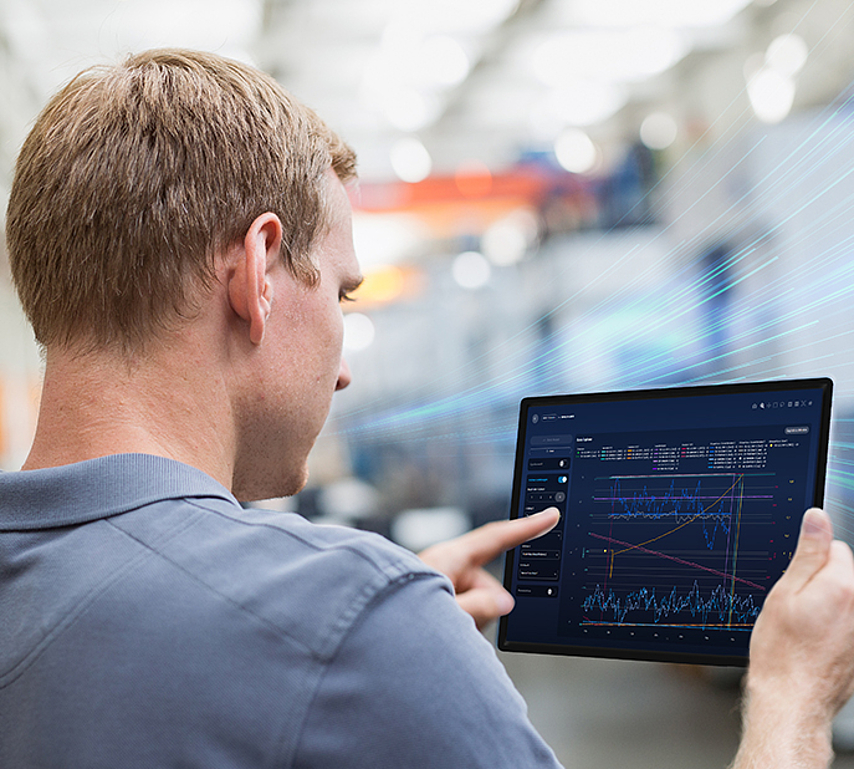
Determine Energy Consumption
It is also possible to determine the energy consumption per component or layer. It clearly shows how the sub-processes influence consumption. Incidentally, the EDNA system can also be used to visualize the data on electrical power, air volume flow and CO2 consumption.
Advantages
- Secure data acquisition every tenth of a second via "handshake"
- Assign values individually to the workpiece
- Data from external sources with different interfaces can be integrated
- Process average values per workpiece and shift (or all "handshakes") via CSV file
Contact IoT
Do you have questions or need more detailed information? Please contact us!
iot@emag.com