08/20/2019 - Oliver Hagenlocher - Press
PI 800—Modular ECM / PECM Machine: Completing complex machining tasks very efficiently with an electrochemical process
Anyone who has had a closer look at the ECM process knows that it is an innovative technology. In order to make manufacturing with PECM even more accessible, EMAG ECM, headquartered in Gaildorf, near Schwäbisch Hall in Germany, has developed a new machine—the PI 800—which boasts a modular and compact design.
Images
PECM machines from EMAG ECM, based in Gaildorf, near Schwäbisch Hall in Germany, are already used in the automotive, aerospace, and energy industries, and in medical engineering, just to mention a few. With the new PI series, EMAG ECM experts are now making a decisive technological leap forward to be able to address an even larger customer base. The generator technology, the electrolyte management system and a new modular tool system are housed on a single machine base. The new PI thus comes with a footprint of only about 5.5 square meters, including filtration. Its minimal footprint has made the forklift-compatible machine become the new universal machine for the most varied ECM applications. The standardization philosophy that the colleagues from EMAG Salach already use for their modular solutions has been adopted to reduce costs. The new dipping module of the PI machine, which is suitable for mass production, has been built on the tried-and-tested standard platform of the C machines, which shortens lead times and reduces costs. Rather than giving up on functionality, costs are reduced to be able to provide an appropriate response to the pressure on costs in production. “Many of our users have really been waiting for this,” explains Daniel Plattner from Technical Sales at EMAG ECM. “Even the tool modules have been standardized in order to be able to bundle an optimal price-performance package. At the same time, maximum rigidity was a foremost priority when we designed the machine and above all for the machining modules. That’s what makes the ECM process run with utmost precision, efficiency and reliability.”
(What exactly is ECM? Find out everything about the technology in this video https://www.youtube.com/watch?v=k6yeDLK457k)
The right module for every application
“As a rule, our customers are searching for an alternative to conventional machining, since it is too elaborate for various reasons and thus just too expensive,” explains Plattner. “We are able to cover many inquiries that we receive with the ECM drilling, ECM broaching and ECM countersinking technologies.“ This is precisely the reason for which the specialists at EMAG ECM have developed a tailored production solution at an attractive price—the new PI 800. Users can choose from two models: The PECM module with oscillator and the ECM dipping module, both for simultaneous machining of several identical workpieces. Each module is built on a machine base made from MINERALIT® polymer concrete. MINERALIT® has optimal vibration-damping properties and contributes to the modules’ high precision. The linear guides with absolute measuring systems, which ensure high rigidity and precision during machining operations, are fastened onto the machine base.
(Machining e-bike components using electro-chemical machining: Watch the machining example in this video: https://www.youtube.com/watch?v=HtSBQgvcgH0)
Contactless and perfectly tailored
The ECM process is a contactless machining process in which the hardness of the material has no impact on the feed rate or precision. This in turn leads to long tool life of the tool cathode and contributes to very low production costs. Since the major part of the machining module is manufactured from the standard version, only the actual tool cathode needs to be adapted to the respective application or workpiece. This produces top-quality surfaces, depending on peak top values of the material, which reach up to Ra 0.2 and higher. Even complex 3D geometries can be reproduced and machined with precision. Based on this, feed rates of up to 5 mm/min can be reached in the field of rough-machining. On average, 0.1 to 0.2 mm/min are achieved in finish-machining. High economic efficiency can be attained for medium to high unit volumes through flat machining of components or parallel machining of several components. The precision that can be achieved in production reaches down to 20 micrometers. Last but not least, the technology is very flexible. For example, the cycle time can be changed with scalable equipment, the system can be upgraded to full automation or the machine can be interlinked with additional EMAG machines.
On the whole, the ECM specialists at EMAG foresee great opportunities for their technology in the future. This, for example, also applies with a view to the emerging electromobility in Asia, the Americas and Europe: According to Plattner, when the automotive industry or its suppliers plan new production projects for which they rely on efficient workflows, in many areas of application there is no way around ECM or PECM. On one hand, the process simplifies the overall machining process of complex components with demanding geometries. In this context, production costs can be remarkably reduced. On the other hand, electrochemical removal of material ensures a very constant component quality. We believe these advantages will make the difference.”
Also read our interview with Richard Keller from EMAG ECM and why one should not miss the EMO 2019 under any circumstances.
Downloads
Contact
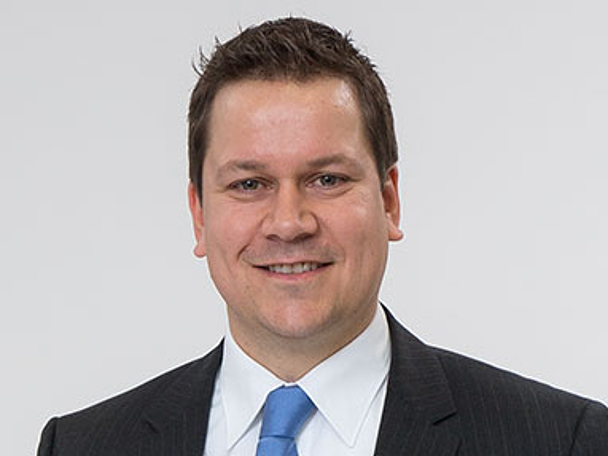
Oliver Hagenlocher
Area
Press and Communication