20.08.2019 - Oliver Hagenlocher - Presse
PI 800 – Modulare ECM / PECM-Maschine: Komplexe Bearbeitungsaufgaben mit elektrochemischen Verfahren hocheffizient umsetzen
Dass das ECM-Verfahren eine innovative Technologie darstellt, weiß jeder, der sich schon einmal mit den Möglichkeiten des Verfahrens auseinandergesetzt hat. Um den Einstieg in die Fertigung mit ECM / PECM noch einfacher zu gestalten, hat das Unternehmen EMAG ECM mit Sitz in Gaildorf bei Schwäbisch Hall nun eine neue Maschine entwickelt, die PI 800, die sich durch einen modularen und kompakten Aufbau auszeichnet.
Bilder
PECM-Anlagen von EMAG ECM aus Gaildorf bei Schwäbisch Hall kommen zum Beispiel bereits im Automobilbau, in der Flugzeugindustrie, der Medizintechnik oder der Energiewirtschaft zum Einsatz. Jetzt machen die Experten mit der neuen PI-Reihe einen entscheidenden technologischen Schritt nach vorne, um einen noch größeren Kundenkreis ansprechen zu können. Auf einem Maschinengrundkörper werden die Generatortechnik, das Elektrolyt-Management-System sowie ein neues, modulares Werkzeugsystem untergebracht. So kommt die neue PI inklusive Filtration auf einen Footprint von nur rund 5,5 Quadratmetern. Die geringe Aufstellfläche der staplerfähigen Maschine macht sie damit zur neuen Universalmaschine für ECM-Anwendungen unterschiedlichster Art. Um Kosten zu reduzieren, übernimmt man die Standardisierungsphilosophie, die von den Kollegen von EMAG Salach bereits für die Modular Solutions angewendet wurde. Das neue, serientaugliche Senkmodul der PI-Maschine wird auf der bestehenden und bewährten Standardplattform der C-Maschinen aufgebaut, was Lieferzeiten und die Kosten senkt. Nicht Funktion, sondern Aufwand wird reduziert, um auf den Kostendruck in der Produktion die passende Antwort geben zu können „Darauf haben viele unserer Anwender wirklich gewartet“, erklärt Daniel Plattner vom Technischen Vertrieb bei EMAG ECM. „Auch die Werkzeugmodule wurden standardisiert, um ein optimales Preis-Leistungs-Paket schnüren zu können. Gleichzeitig haben wir bei der Konstruktion der Maschine, aber vor allem bei den Bearbeitungsmodulen auf maximale Steifigkeit geachtet. Damit läuft der ECM-Prozess absolut präzise, effizient und prozesssicher ab.“
(Was ist eigentlich ECM? Alles zu der Technologie erfahren Sie in diesem Video https://www.youtube.com/watch?v=k6yeDLK457k)
Für jede Anwendung das passende Modul
„In der Regel suchen unsere Kunden eine Alternative zur Zerspannung, da diese aus verschiedenen Gründen zu aufwendig und damit schlicht zu teuer ist“, erklärt Plattner. „Viele Anfragen, die wir bekommen, können wir mit den Technologien ECM-Bohren, ECM-,Räumen‘ und ECM-Senken abdecken.“ Speziell dafür entwickelten die Spezialisten von EMAG ECM eine passgenaue Produktionslösung zu einem attraktiven Preis, die neue PI 800. Dem Anwender stehen dabei zwei Module zur Auswahl: Das PECM-Modul mit Oszillator und das ECM-Senkmodul, beide für die Simultanbearbeitung mehrerer identischer Werkstücke. Jedes der Module wird auf einem Grundkörper aus Polymerbeton MINERALIT® aufgebaut. MINERALIT® hat ideale schwingungsdämpfende Eigenschaften und trägt zu einer hohen Präzision der Module bei. Auf dem Grundkörper sind die Linearführungen mit absoluten Messsystemen angebracht, die für eine hohe Steifigkeit und Genauigkeit bei der Bearbeitung sorgen.
(Bearbeitung von E-Bike Komponenten mit Elektrochemischer Metallbearbeitung: Sehen Sie das Bearbeitungsbeispiel in diesem Video: https://www.youtube.com/watch?v=HtSBQgvcgH0)
Berührungslos und perfekt angepasst.
Das ECM-Verfahren ist ein berührungsloses Bearbeitungsverfahren, bei dem die Materialhärte keinen Einfluss auf Vorschub oder Präzision hat. Das führt wiederum zu einer hohen Standzeit der Werkzeugkathode und trägt so zu den sehr niedrigen Produktionskosten bei. Da der Großteil des Bearbeitungsmoduls im Standard hergestellt wird, muss lediglich die Werkzeugkathode selbst auf die jeweilige Anwendung bzw. das jeweilige Werkstück angepasst werden. So entstehen Oberflächen mit maximaler Güte, je nach Werkstoff Top-Werte von bis zu Ra 0,2 und besser. Selbst schwierige 3D-Geometrien lassen sich reproduzierbar und präzise bearbeiten. Auf dieser Basis können Vorschübe im Bereich der Schruppbearbeitung von bis zu 5 mm/min erreicht werden. In der Endbearbeitung werden durchschnittlich 0,1 bis 0,2 mm/min. erzielt. Durch die flächige Bearbeitung von Bauteilen bzw. die parallele Bearbeitung mehrerer Bauteile lässt sich bei mittleren bis großen Stückzahlen eine hohe Wirtschaftlichkeit erreichen. Die dabei erzielbaren Genauigkeiten in der Produktion reichen bis unter 20 Mikrometer. Nicht zuletzt ist die Technologie sehr flexibel. So kann zum Beispiel die Taktzeit durch skalierbare Vorrichtungen verändert, eine Aufrüstung zur Vollautomation durchgeführt oder die Maschine mit weiteren EMAG Maschinen verkettet werden.
Insgesamt sehen die ECM-Spezialisten bei EMAG beste Zukunftschancen für ihre Technologie. Das gilt beispielsweise auch mit Blick auf die aufstrebende Elektromobilität in Asien, Amerika und Europa: Wenn die Automobilindustrie oder deren Zulieferer neue Produktionsvorhaben planen und dabei auf effiziente Abläufe setzen, komme man in vielen Anwendungsbereichen nicht an ECM bzw. PECM vorbei, so Plattner. „Einerseits vereinfacht das Verfahren den gesamten Bearbeitungsprozess komplexer Bauteile mit anspruchsvoller Geometrie. Dabei lassen sich die Produktionskosten merklich senken. Andererseits sorgt das elektrochemische Abtragen für eine sehr konstante Bauteilqualität. Diese Vorteile werden sich aus unserer Sicht durchsetzen.“
Lesen Sie außerdem unser Interview mit Richard Keller vom EMAG ECM und warum man die EMO 2019 auf keinen Fall verpassen sollte.
Downloads
Ansprechpartner
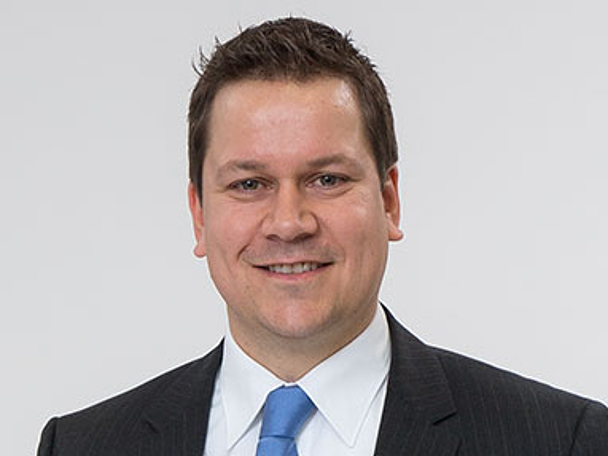
Oliver Hagenlocher
Bereich
Presse und Kommunikation