10/14/2019 - Oliver Hagenlocher - Press
EMAG Production System: Perfecting the Finish-Machining of Turbocharger Shafts
The production of turbochargers is one of the most demanding tasks in automotive engineering: High-strength materials, precise geometric requirements, large quantities and price pressure are key challenges for OEMs and suppliers. The continual pressure to downsize in the automotive industry, paired with the increased demand for high performance parts, with smaller displacement, is putting components like turbochargers and shafts as the primary focus for production planners. These planners are demanding automated production solutions that increase quantities produced while decreasing overall cost per part and guaranteeing high precision. To meet this demand, EMAG has developed a complete production solution: A linked production system with all components developed by a single source, which will complete machine the turboshaft. This includes pre-turning, hardening and grinding and ECM balancing. The component will be complete machined in less than 50 seconds, and the finished product will exceed all quality requirements.
The downsizing trend in automotive engineering does not appear to be slowing down. For example, the VDMA (German Engineering Federation) predicts in its study “Antrieb im Wandel” (“Drives Undergoing Change”) that the average number of cylinders in passenger cars will decrease from 4.3 today to 4 by the year 2030. So the engines of tomorrow will continue to shrink in size. At the same time, their displacement is decreasing, which is compensated for by increased turbocharging: The intake air is compressed even more and forced into the combustion chamber at maximum pressure. This leads to extreme performance values: In modern engines, the compressor wheel rotates at up to 290,000 rpm, resulting in enormously high temperatures in the component. Under these conditions, the manufacturing of turbocharger shafts is an especially demanding task in automotive engineering. These components are made out of high-performance materials such as Inconel, which can withstand temperatures of over 1,000 degrees Celsius (1,832 degrees Fahrenheit), but are difficult to machine due to their hardness. Even with all of these requirements, turbochargers still have to be produced in large quantities with high precision and process reliability – a standard request for EMAG, as Markus Neubauer, Technical Application Engineer at EMAG, points out: “Our comprehensive experience benefits us here, because our wide range of technologies covers the entire process chain – from pre-machining to finishing, including balancing. This means that the complete line including planning, project management, implementation and service comes from a single source. This benefit plays a decisive role in establishing a new turbocharger production facility. For the customer, the entire planning and after-sales process is simplified, drastically.”
Turning, Hardening, Grinding and Balancing in a Single Line
The advantage of this line can is obvious when you look at the complex individual processes, which range from pre-turning and induction hardening, to grinding and electro-chemical balancing. In total there are five main operations:
- At the start of the line, a palletizer robot places the blanks on the conveyor belt of the VTC 100-4 vertical turning center, and then the machine’s workpiece gripper transports the component into the machining area. In a single clamping operation, the turbine shaft is pre-turned, with four-axis machining, guaranteeing reduced processing times. The vertical design and the resulting free flow of chips prevent chip build-up.
- A second robot removes the pre-turned parts from the conveyor belt of the VTC 100-4 and forwards them for heat treatment in the MIND-M 1000 by EMAG eldec, where the components are quickly heated to a precise temperature. Experts refer to this as “stress relief”: Any stresses that may exist in the component are relieved in a controlled environment. If it is necessary to harden the bearing seats on the component, this machine could do that as well.
- Various grinding operations take place in the third and fourth operations: First, the horizontal grinding of the shaft is performed on an EMAG HG 204. Next, the VLC 200 GT vertical grinding machine finishes the ring grooves and the outer wing contour of the turbine wheel. Optionally, the wing contour can be deburred with an additional driven brush in the machining area of the VLC 200 GT.
- After the components have passed through a washing facility and a measuring system, the final operation takes place: Balancing with electro-chemical machining in a CS machine by EMAG ECM. This chip-free process is performed with a single repeat step. Due to the non-contact removal of material, tool wear is minimal – a great advantage compared to cutting processes.
Perfect Processes for a Final Quality
The entire finish processing of the car turbocharger shaft (turbine rotor) is completed in less than 50 seconds. For a three-shift operation, this results in an output of 420,000 to 450,000 turbine rotors per year. In each case, after the final balancing, the component is ready for installation. “We always guarantee a customized system architecture for these and similar projects. For this reason, EMAG will provide all of its product knowledge to the customer about a variety of tool applications, the design of multifunctional machine tools and their overall control and interlinking, as well as their integration into cross-system concepts,” Markus Neubauer sums up. “Providing this kind of know-how from a single source guarantees our success, especially in the production of challenging components, and gives us a convincing edge in the market.”
Images
Downloads
Contact
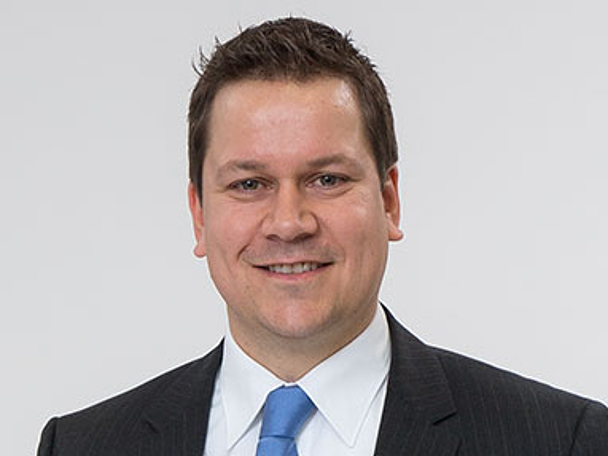
Oliver Hagenlocher
Area
Press and Communication