14/10/2019 - Oliver Hagenlocher - Presse
Système de production EMAG : Perfectionnement de l'usinage de finition des arbres de turbocompresseur
La fabrication des turbocompresseurs fait partie des tâches les plus exigeantes de la construction automobile : des matériaux très résistants, des exigences géométriques extrêmes, un grand nombre de pièces et la pression sur les prix caractérisent la tâche qui incombe aux équipementiers et aux sous-traitants. À cela s'ajoute : l’inexorable rationalisation – puissance augmentée à cylindrée réduite – auquel la construction automobile est soumise, qui ramène les pièces telles que l'arbre du turbocompresseur au centre de l'intérêt des planificateurs de production. Les solutions de production demandées doivent être automatisées et capables de produire des nombres de pièces en constante augmentation, à un coût unitaire en baisse, tout en assurant l'extrême précision des processus. EMAG a développé une solution complète pour assurer cette tâche : un système de production intégré « d'un seul fournisseur » gère l'usinage de finition complet de l'arbre de turbocompresseur, depuis le pré-tournage, la trempe, la rectification, jusqu'à l'équilibrage ECM. Une pièce quitte la ligne dans sa qualité finale en moins de 50 secondes.
La tendance à la rationalisation se répand inexorablement dans la construction automobile. C'est en tout cas ce que prévoit notamment une étude du VDMA, « L'évolution de l'entraînement », qui pronostique une réduction du nombre des cylindres des voitures de 4,3 aujourd'hui à 4 en 2030. Les moteurs de demain seront donc plus petits. La cylindrée diminuera elle aussi, ce qui sera compensé par une augmentation de la turbocompression : l'air aspiré sera davantage compacté avant d'être comprimé à pression maximum dans la chambre de combustion. Dans la pratique, cela conduira à des performances extrêmes : la roue du compresseur d'un moteur moderne tourne jusqu'à 290 000 tr/min., la pièce est donc soumise à une température extrêmement élevée. Dans ces conditions, la fabrication des arbres de turbocompresseur compte parmi les tâches les plus exigeantes de la construction automobile. Les arbres sont fabriqués en matériaux hautes performances, en Inconel par exemple, capables de résister à des températures dépassant 1000 degrés Celsius mais difficiles à usiner à cause de leur dureté. Mais ce domaine des turbocompresseurs, qui implique de produire de grands nombres de pièces avec une précision extrême et une grande sécurité de processus, demeure globalement une tâche classique de la société EMAG, comme le souligne Markus Neubauer, Technical Application Engineer chez EMAG : « Notre important savoir-faire est un atout majeur car l'éventail de technologies que nous utilisons nous permet de couvrir l'ensemble de la chaîne d'opérations requises, du pré-usinage à la finition, équilibrage compris. La ligne complète de fabrication, planification, gestion de projet, réalisation et service, est ainsi réalisée par un seul constructeur. Cette qualité joue un rôle décisif dans la réalisation d'une nouvelle ligne de production de turbocompresseurs. Les phases de planification et d'après-vente sont considérablement simplifiées pour les clients. »
Tournage, trempe, rectification et équilibrage dans une seule ligne
Pour comprendre l'importance de cet atout, il suffit d'observer le processus sophistiqué qui va du pré-usinage au traitement thermique inductif en passant par la rectification, jusqu'à l'équilibrage électrochimique. Cet usinage compte en tout cinq opérations majeures :
- En début de ligne, un robot de palettisation pose les pièces brutes sur le convoyeur du tour vertical VTC 100-4, puis la pince de préhension de la machine transporte le composant dans l'espace de travail. L'arbre de turbine est pré-tourné en un seul serrage avec un usinage en quatre axes qui garantit la réduction des temps principaux. La structure verticale et la chute sans obstacle des copeaux qui en résulte empêchent l’accumulation de ceux-ci.
- Un second robot prélève les pièces pré-tournées du convoyeur du tour VTC 100-4 et déclenche le traitement thermique dans la machine MIND-M 1000 EMAG eldec, qui chauffe très rapidement les composants à une température précise. Les experts désignent cette opération par « stress relieve » (suppression des contraintes). Les tensions intrinsèques éventuelles du composant sont ainsi éliminées de manière ciblée. Lorsqu'elle est nécessaire, la trempe des sièges de paliers du composant est également possible avec cette machine.
- La troisième et la quatrième étapes consistent en diverses tâches de rectification : La rectification en position horizontale de l'arbre est d'abord effectuée dans une machine HG 204 EMAG. Ensuite, la rectifieuse verticale VLC 200 GT réalise l'usinage de précision des rainures circulaires et du contour extérieur des pales de la roue de turbine. Une option permet d'ébavurer le contour des pales au moyen d'une brosse supplémentaire située dans l'espace de travail de la machine VLC 200 GT.
- L'opération finale se déroule une fois que les pièces ont traversé un dispositif de lavage et un système de mesure : l'équilibrage via l’usinage électrochimique des métaux dans une machine CS EMAG ECM. Cette opération sans copeau s’effectue en une seule étape répétitive. L'enlèvement de matière sans contact permet d'obtenir une usure minimum de l'outil, ce qui représente un avantage majeur par rapport aux méthodes générant des copeaux.
Processus parfaits pour obtenir une qualité finale prête au montage
L'usinage complet pour la finition de l'arbre du turbocompresseur automobile (rotor de turbine) se déroule en un temps de cycle inférieur à 50 secondes. En production sur trois équipes, la machine peut ainsi produire de 420 000 à 450 000 rotors de turbine par an. Et ils présentent tous la qualité suivante : une fois que le composant a été équilibré, il est prêt à être monté. « En définitive, nous garantissons toujours une architecture de système parfaitement adaptée, que ce soit pour ces projets ou des projets équivalents. En étroit contact avec le client, la société EMAG apporte toutes ses connaissances en matière d'utilisation très diversifiée des outils, pour la conception de machines-outils multifonctions dotées d’une commande et d’une interconnexion globales, et pour l'intégration dans des systèmes complets. » résume Markus Neubauer. « Ce savoir-faire provenant d'une source unique est aussi le facteur déterminant pour garantir le succès dans la production de composants très exigeants avec lesquels nous pouvons nous établir sur le marché. »
Images
Interlocuteurs
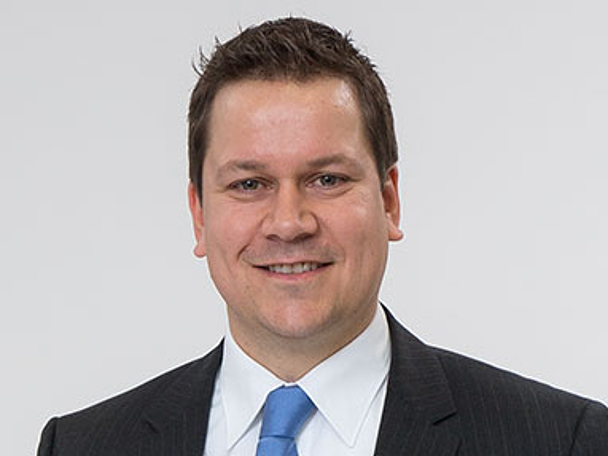
Oliver Hagenlocher
Zone
Press and Communication