08/24/2020 - Oliver Hagenlocher - Press
HLC 150 H by EMAG KOEPFER: All-round gear-cutting solution for more flexibility and lower cost
More than ever, planners in the automotive industry are faced with the crucial challenge of flexibility in production technology. Manufacturers continually need to cope with modified ranges of components. For instance, the geometry can change very quickly. For gear cutting in particular, this development can reach new extremes. Take the example of steering components: Production planners are looking for extremely flexible machines that can efficiently cut the gears of steering pinions, worm gears and screws. This is how an EPS steering gear can be produced on a single machine. Innovative machine builders are able to accomplish this task, as demonstrated by EMAG KOEPFER with their horizontal gear cutting machine HLC 150 H – an all-round solution in every way. This high-performance machine is able to process a very wide range of workpieces – transmission and anchor shafts, pinions, and planetary gears with a length of up to 500 millimeters. It features all relevant gear cutting technologies such as gear hobbing, skiving, screw milling, worm skiving and chamfering. Workpieces up to module 3 can be finished without burrs, meeting high quality requirements. You could hardly ask for more flexibility in gear production.
Images
Huge output quantities, a wide variety of demands on the workpieces, and materials ranging from high-strength steel to relatively soft plastics: Automotive gear production is a very large and challenging field. In view of hybrid drives and various assistance systems, the wide array of gearing in cars tends to increase even further. The big question is therefore, more than ever: Which production solutions allow the efficient and comprehensive gearing of the largest possible number of different workpieces?
Universal machining at low cost
“This was exactly the question to start the development of the HLC 150 H machine”, explains Jörg Lohmann, Sales Director of EMAG KOEPFER in Schwenningen, Germany. “Our answer was to develop a universal solution with high-performance components. We are using all relevant machining technologies including chamfering. We have a large axis center distance of up to 130 millimeters, and a powerful 28 kW cutter head. As a result, we can efficiently cut gears on a wide range of workpieces up to module 3 with a maximum crown circle diameter of 150 millimeters, and up to 500 millimeters in length. The customer benefits from lower costs and higher workpiece quality.” Transmission shafts are a good example to illustrate this approach – the HLC 150 H guarantees hobbing and chamfering completely free of secondary burrs. After rough-machining the gears in a first step, the gearing is deburred. The finish is applied during the second hobbing step. The result is an entirely burr-free chamfered gear. In addition, the HLC 150 H has many cost-reducing features – for instance, the highly energy-efficient frequency-controlled hydraulic units, and the fact that the media supply is only activated when required. Furthermore, the counter bearing with its quick-clamping system and the good accessibility of the machine allow changing of all tools within a very short time. Unproductive downtimes, such as for changing batches, are thus reduced to a minimum. “Regarding the cost aspect, we must emphasize that the customer will benefit from excellent value for money from the day of his initial investment”, adds Lohmann. “This is made possible by the highly efficient EMAG production facilities in Zerbst, Germany, and in Jintan, China. This is where the basic machine structure is created by means of highly efficient processes.”
Workpiece quality guaranteed
It is noteworthy to examine some of the technical details that contribute to the workpiece quality and process reliability on the HLC 150 H. During the milling operation, for instance, the cutter head with its very rigid suspension always moves in its entirety. The shift axis is based on the interpolation of two axes. This results in a large swivel angle for the cutter head, and a large shift path at the same time. As a result, the milling process is very smooth and precise. The quality of the cut gears (also in view of absolute measuring systems) is at the very highest level. A similarly important feature is the chip disposal concept by EMAG KOEPFER. Users benefit from free downward chip flow without any chip build-up. That is why the machine is also perfect for dry machining. Additionally, different solutions are available including scraper-belt or permanent-magnetic conveyors – with the option of a deep-bed filter with magnetic preseparator drum for ferromagnetic materials, non-ferrous metals, and plastic. “In each case we ensure that the discharge process runs very smoothly, guaranteeing high process reliability”, says Lohmann. “Especially in large-scale production at high performance this is vitally important.”
Modular automation concept and wide range
Last but not least, a largely modular automation concept is available for this machine, providing for short chip-to-chip times. To begin with, the HLC 150 H can be loaded both manually and by automation system. As a second option, lighter components up to 3 kg are handled by an integrated high-speed gantry loader with rotating twin gripper. However, for heavier workpieces up to 10 kg a V-shaped linear gripper is available. Integration into complete EMAG production lines is equally simple. “In summary we are confident to say that this machine sets a new benchmark for the flexible machining of workpieces up to 500 millimeters in length. Many steering components such as steering pinions, worm gears, screws and transmission shafts fall into this category”, summarizes Lohmann. “This machine really has all it takes: high-performance machining with the 28 kW cutter head, press deburring integrated in the machining area, or chamfering for end-to-end processes and flexible automation for virtually ideal integration into production lines. The bottom line is that the costs for machining steering components or transmission shafts will decrease, while the quality is increasing. We are convinced that the HLC 150 H has the best market opportunities in the automotive industry and with its suppliers.”
Contact
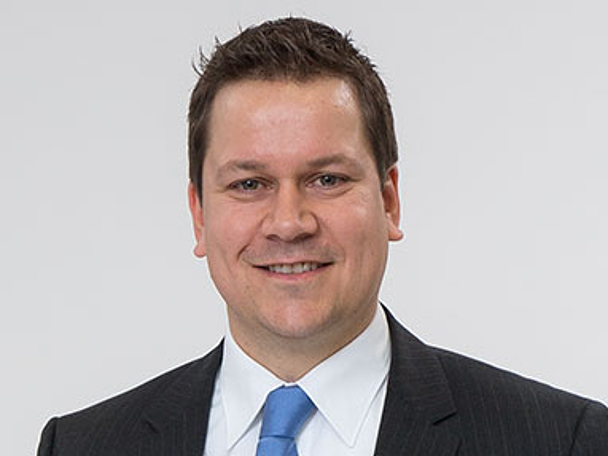
Oliver Hagenlocher
Area
Press and Communication