Producing Rotor Shafts on a Fully Automated Line
EMAG designs and constructs complete production lines for one-piece or two-piece rotor shafts in which all machining processes are perfectly integrated, one after the other. Technology, automation, and process development come from a single source – ideal solutions for the rapidly rising volumes in the electric vehicles sector.
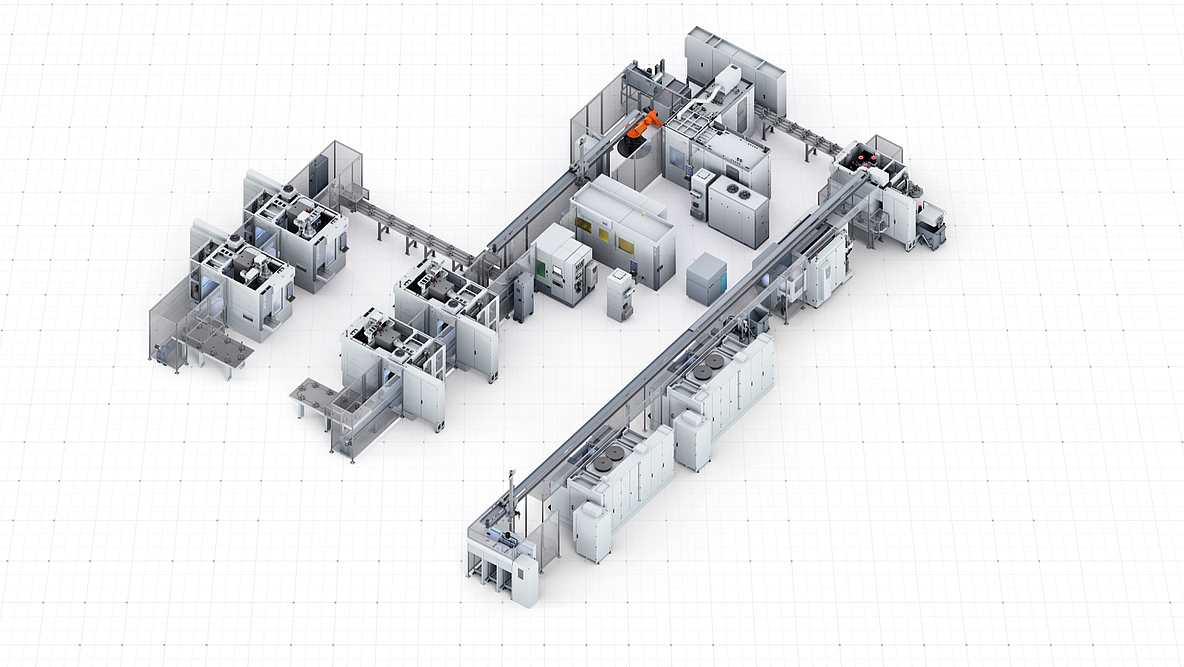
"One face to the customer"
Cooperation often begins in an early phase: Customers can clarify the design drawings of their component with EMAG in advance to enable a production process that is as lean and reliable as possible. In the end, the companies get a perfect production system, which sets benchmarks for cycle times, but at the same time exhibits a high level of stability and production reliability.
The principle "one face to the customer" always applies throughout. An experienced contact at EMAG discusses the requirements of the entire production solution with the customer – including machines that don’t come from EMAG, but might still form part of the complete process chain. EMAG takes care of each and every element of the production solution and works out its specifications. This means customers save a great deal of capacity during the quotation phase – and have a central contact for the subsequent order processing.
Example of a solution for a two-piece rotor shaft
This results in impressive processes – such as the following fully automated production line example for a two-piece rotor shaft. Its production capacity is about 360,000 parts per year. A total of eight operations are involved, all executed by EMAG machines. The individual machines and stations are automated and interlinked by robots, loading gantries, pallet conveyors, and EMAG’s own TrackMotion system.
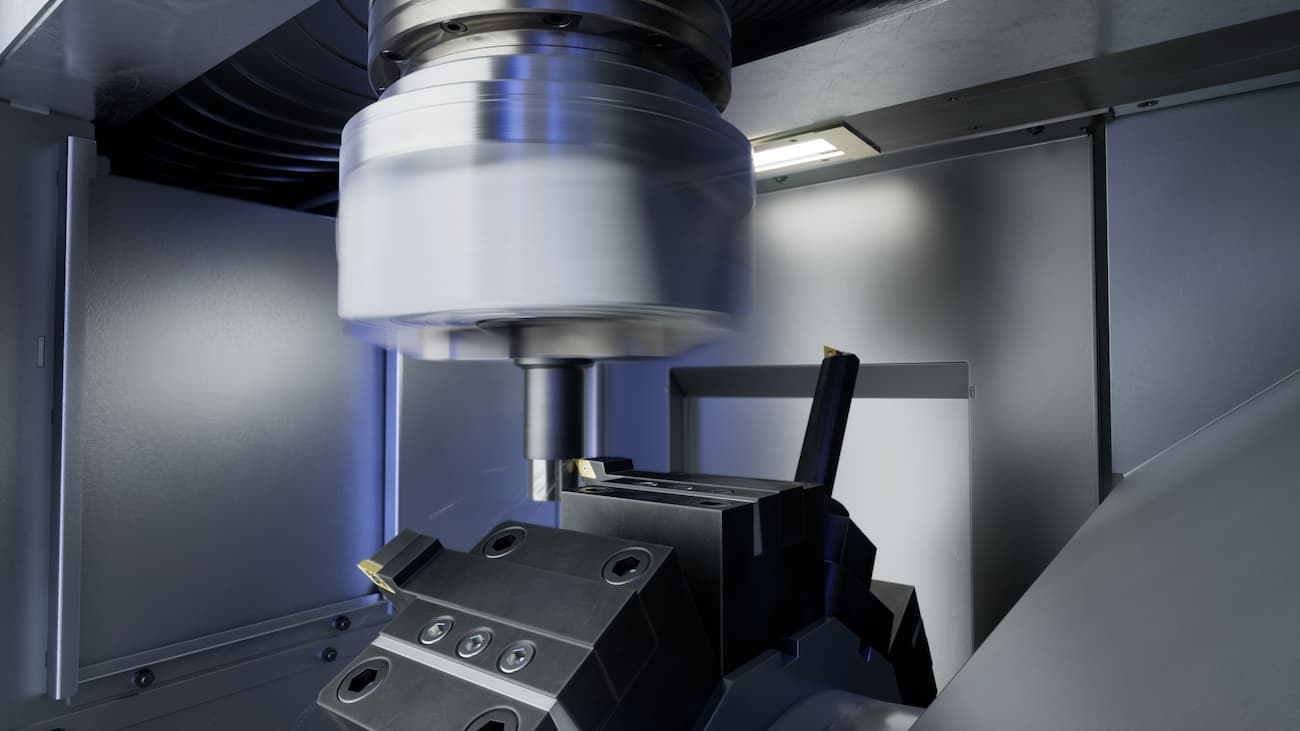
OP 10/OP 20: Turning the End Pieces of the Rotor Shaft
After the raw part is fed in, the pre-turning of the two end pieces is started on a total of four VLC 200 machines from EMAG (OP 10 and OP 20). Each part passes through two machines. After the first side is machined, the part is flipped by the EMAG TrackMotion system and the turning process then starts on the other side.
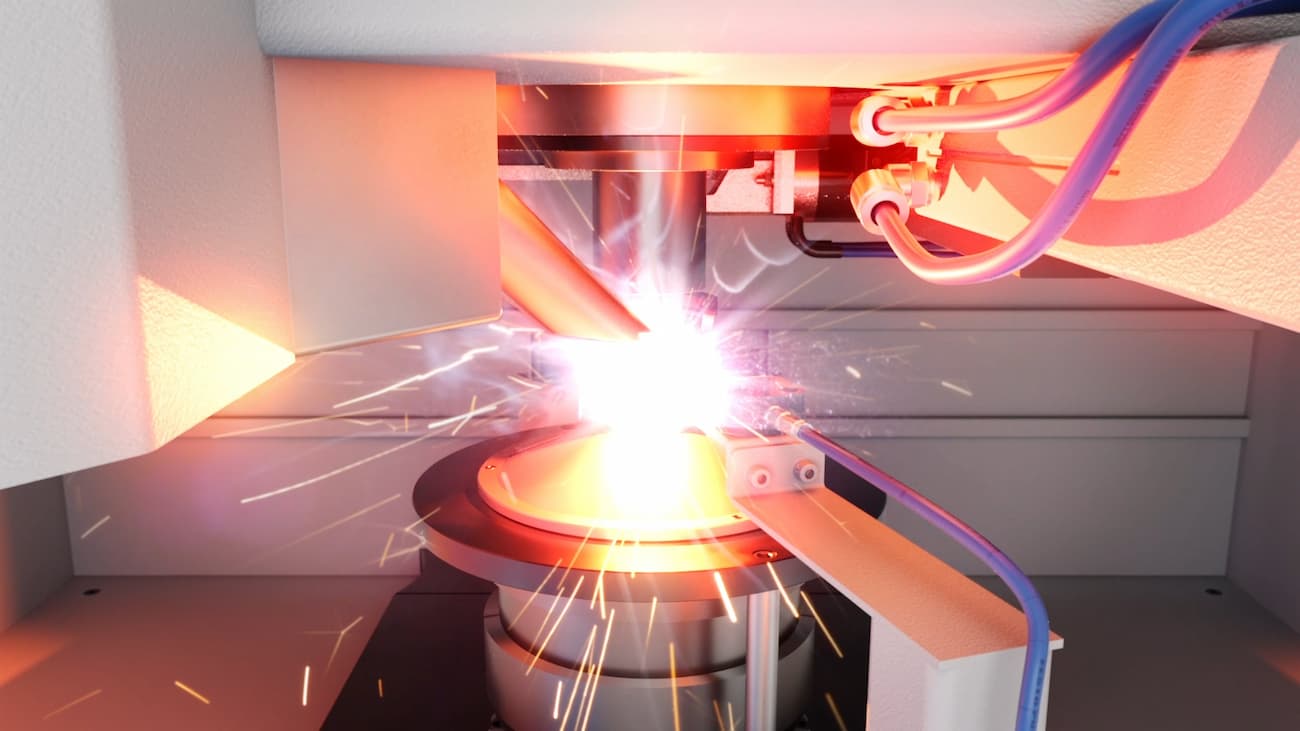
OP 30: Laser Cleaning & Laser Welding
Next, the joining seam is laser-cleaned in OP 30.
The two end pieces (flange and tube) are then fed via a loading gantry to the ELC 6 laser welding machine from EMAG LaserTec. Here, the parts are first joined and then welded.
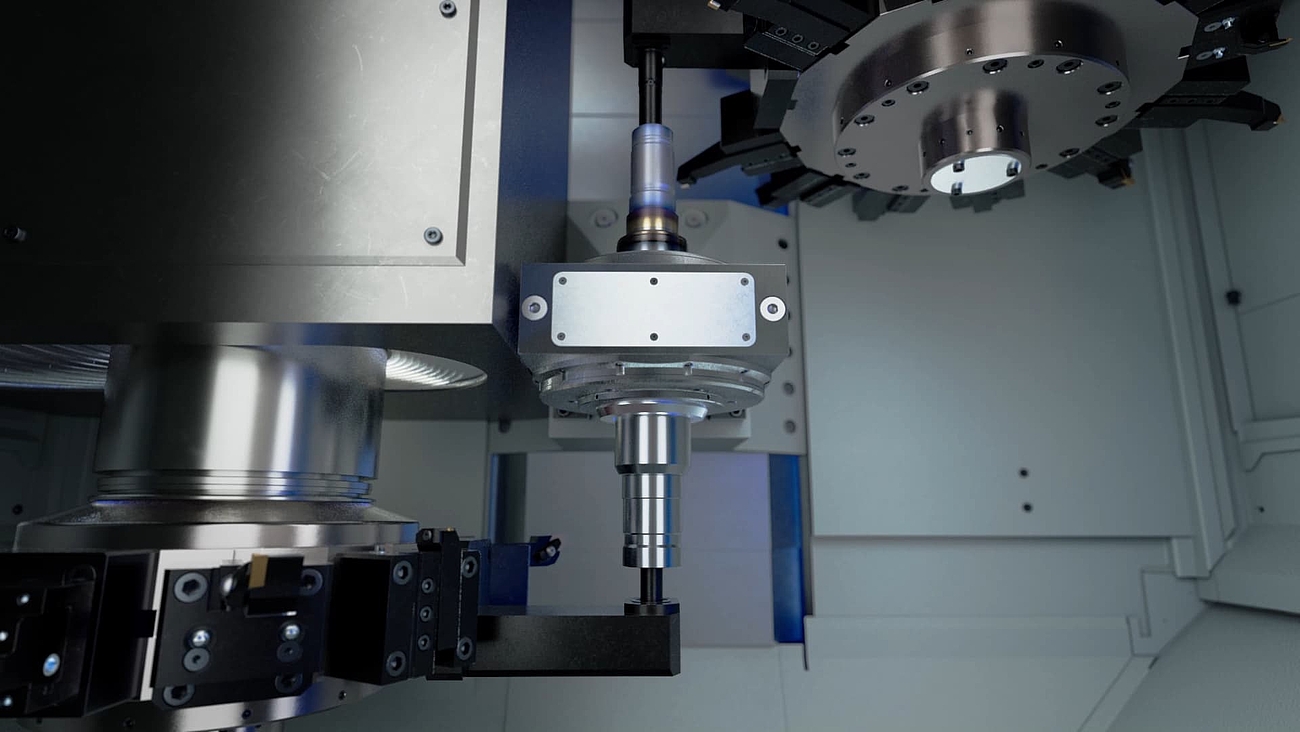
OP 50: Hard Turning of Rotor Shaft
During the subsequent hard turning (OP 50) in a VTC 200 CD (center drive), the shaft undergoes centering.
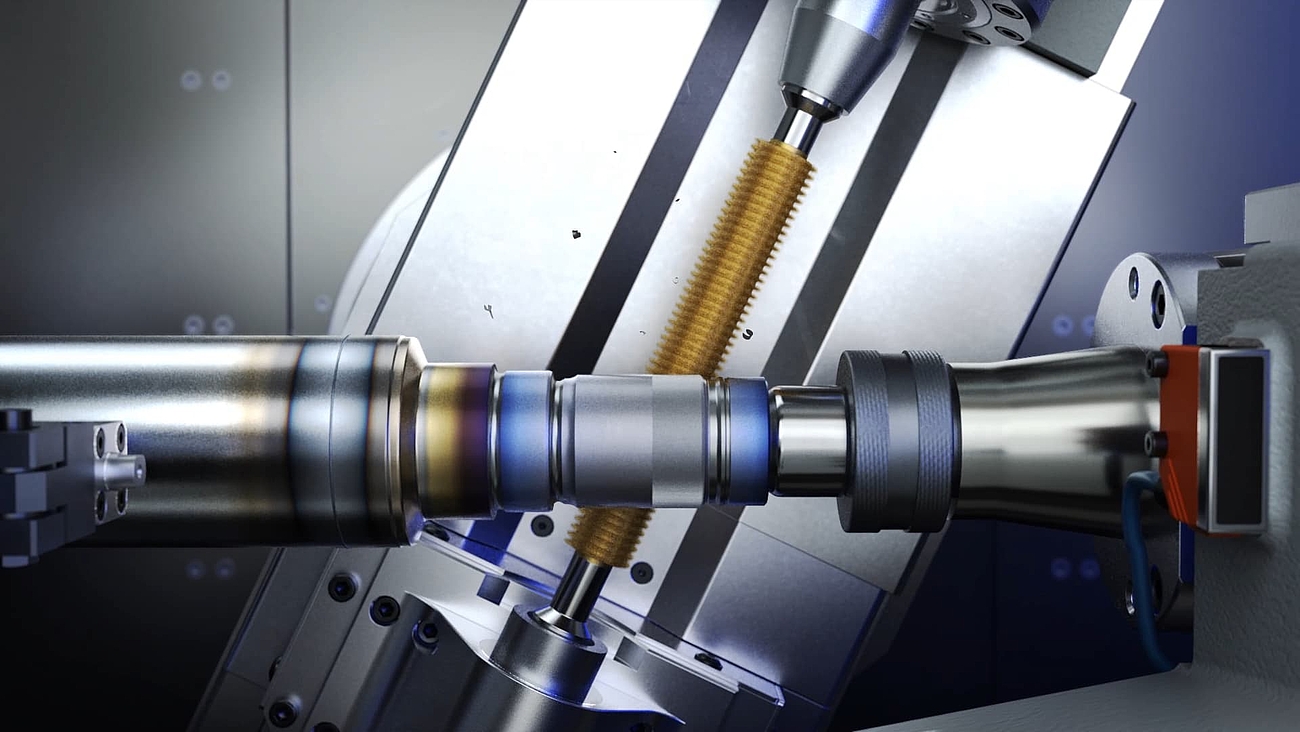
OP 60: Gear Hobbing
In OP 60, the HLC 150 gear hobbing machine from EMAG Koepfer is used to cut splines. This machine, too, is loaded and unloaded by the loading gantry. The parts are fed into the machining area by the internal automation system of the HLC 150.
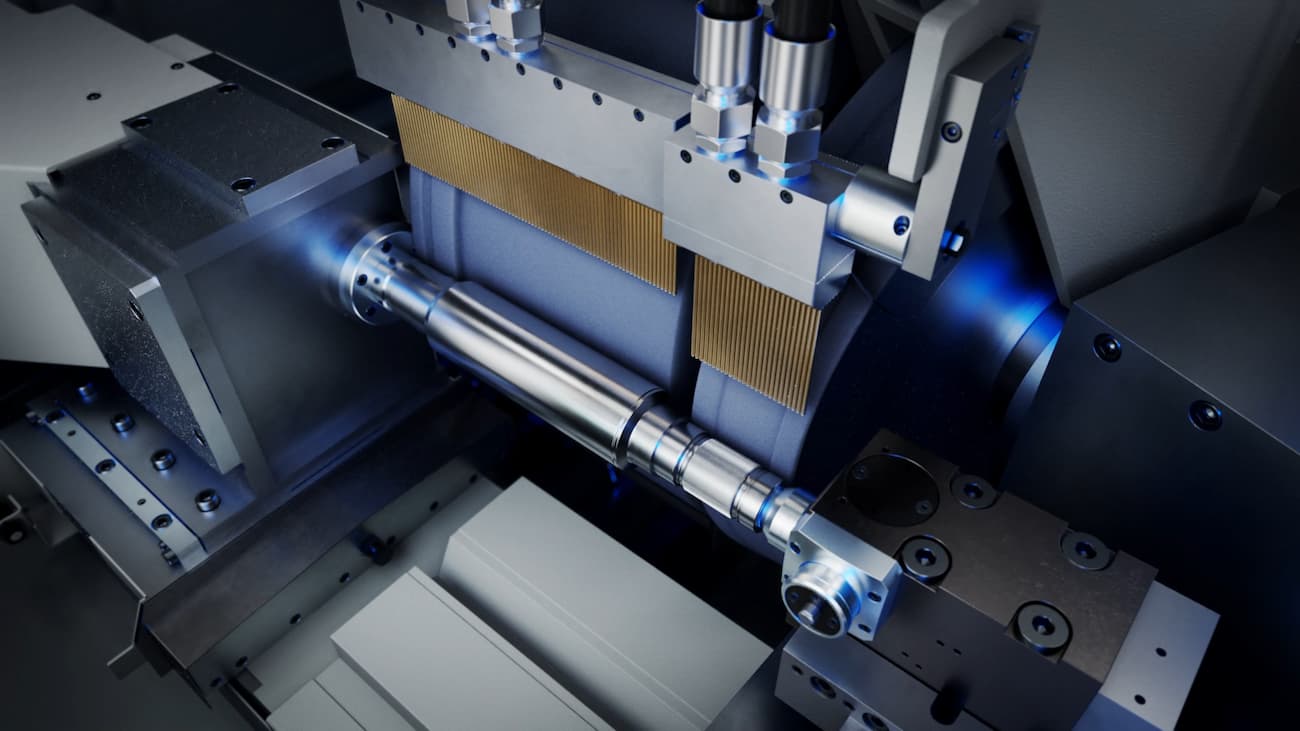
OP 70: Grinding the Rotor Shaft
The grinding processes (OP 70) on bearing seats, flat collars, and the running surface of the rotary shaft seal complete the production process on the rotor shaft. Two EMAG machines of type HG 310 are used for this purpose.
Watch the complete process in this video!
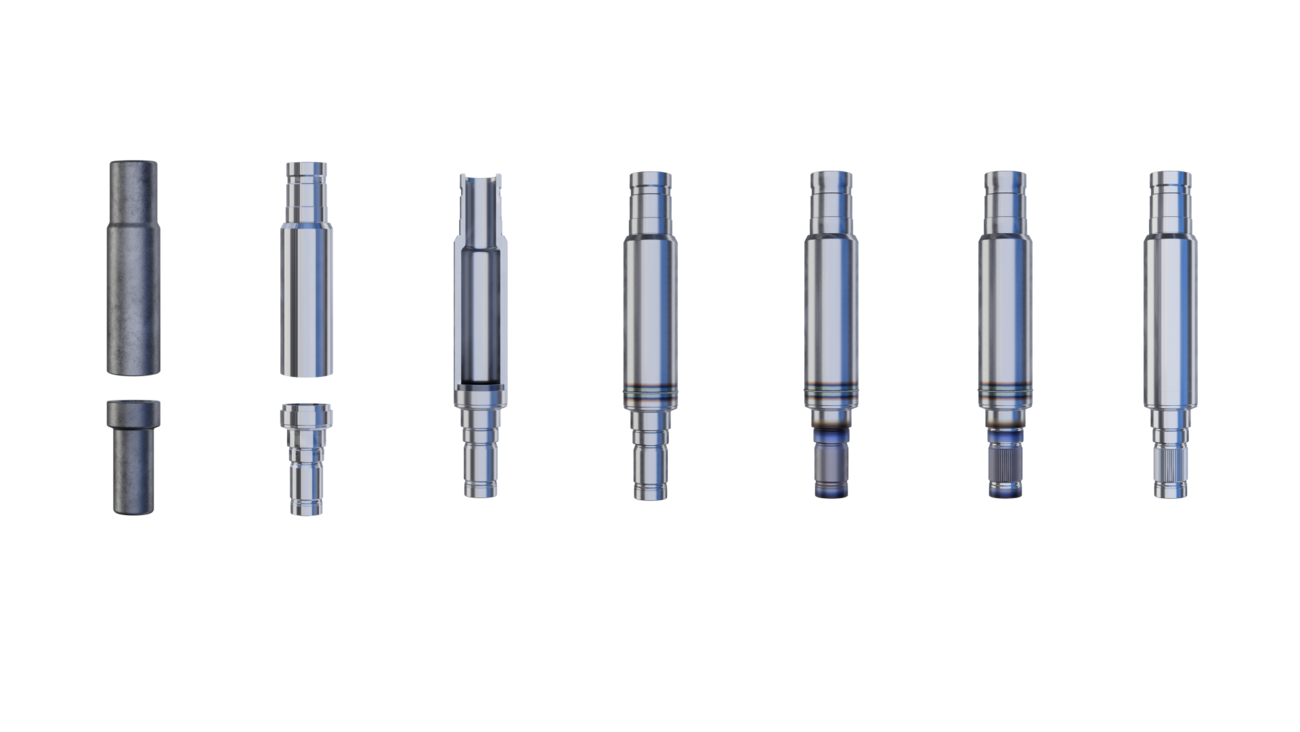
Advantages of this Production Line for Rotor Shafts
- Technology, automation, and process development come from a single source – with the focus always on short delivery times and a rapid start to production.
- All machines and the automation system are perfectly coordinated.
- Simple automation systems, optimized interfaces, and short transport distances create rapid production processes.
- The production system excels with short re-tooling and maintenance times.
- "One face to the customer": an experienced contact at EMAG discusses the requirements of the entire production solution with the customer.
White Paper
Electromobility
Learn in this white paper how highly efficient production solutions for rotors, stator housings and gear parts can look like. Download this White Paper in our Media Center.
Media CenterMachines
(6) machines found
Technologies
Complex Manufacturing Systems from a Single Source thanks to a High Range of Technologies
Laser cleaning is a fast and space-saving process that can replace conventional washing machines in many applications. One of its main strengths is…
Laser welding is a precondition for compact, weight-optimised components and thus for energy- efficient vehicles. Adjustable doses of concentrated…
Vertical turning is a machining process for metal components. EMAG was one of the first machine tool manufacturers to use the vertical turning process…