Brake Disc Grinding Machines
VLC 450 DG
- Outer diameter of friction ring max.: 450 mm | 17.5 in
- Diameter friction ring inside max.: 250 mm | 10 in
- Friction ring thickness: mm 10 - 45
Adapting to layer diversity: challenges and solutions
Specific machining strategies are required depending on the coating material. Multi-layer coatings place high demands on the grinding process. Their machining behavior is similar to the carbide machining known from tool grinding. This type of coating requires low cutting speeds, but all the higher torque. Before machining, these coatings have a roughness of up to 100 micrometers. After the grinding process, both the matrix and the carbides are machined. The machining behavior is due to the dual properties of the coatings: brittle-hard carbides on the one hand and a ductile matrix on the other.
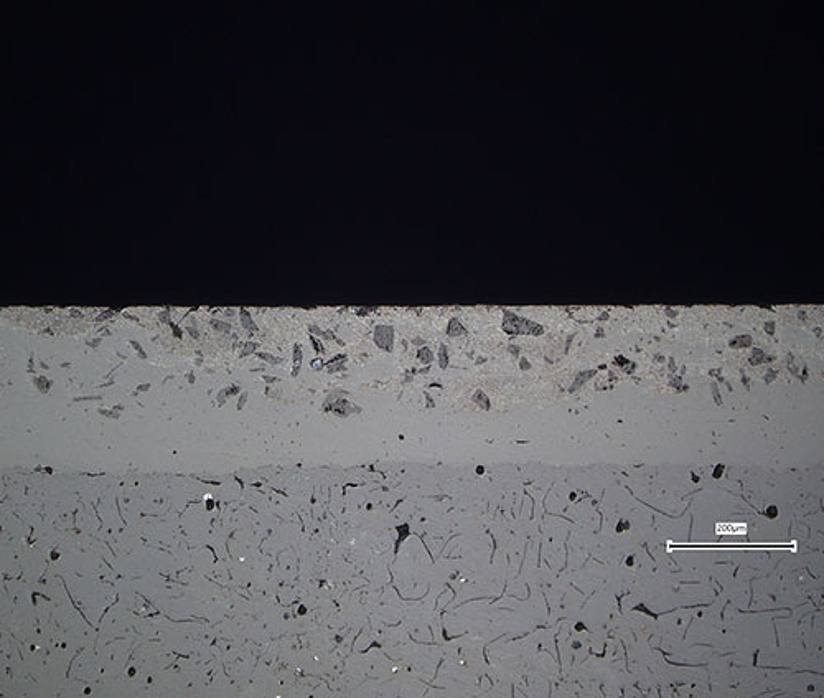
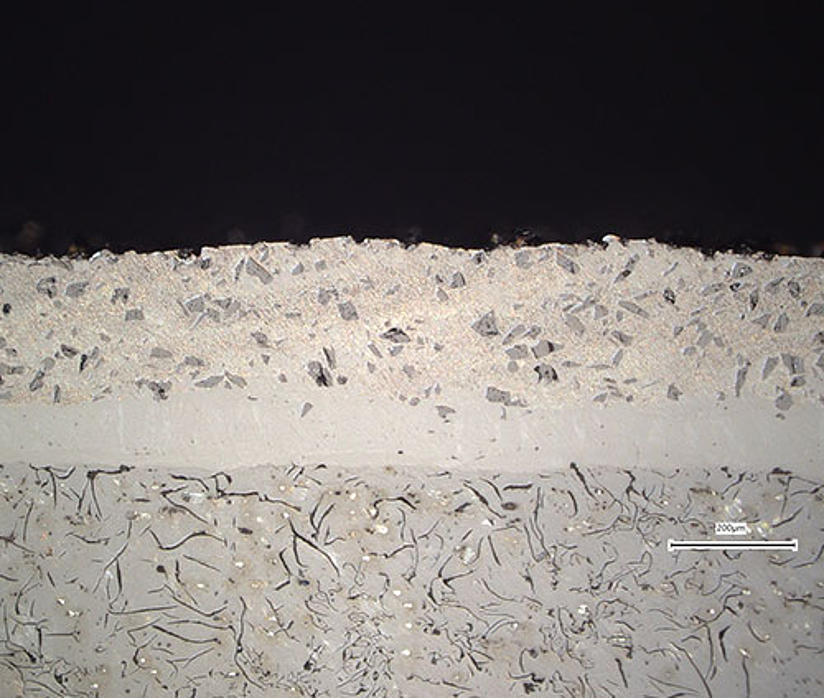
Ductile and brittle materials generally require individual grinding strategies. In the case of the hard coating of brake discs, both come together. The material properties and cutting behavior are not only influenced by the volumetric composition of the materials, but also by the process parameters during laser metal deposition.
Crucial for precision and process reliability: the grinding machine and the technology

The machine concept
The VLC 450 DG is designed for rigidity and durability in order to meet the high demands of batch production. Outside the work area, the machine shuttle forms the interfaces to downstream automation. The machine concept is based on decades of experience in the construction of vertical turning and grinding machines. The intelligent sensory equipment enables adaptive process control.
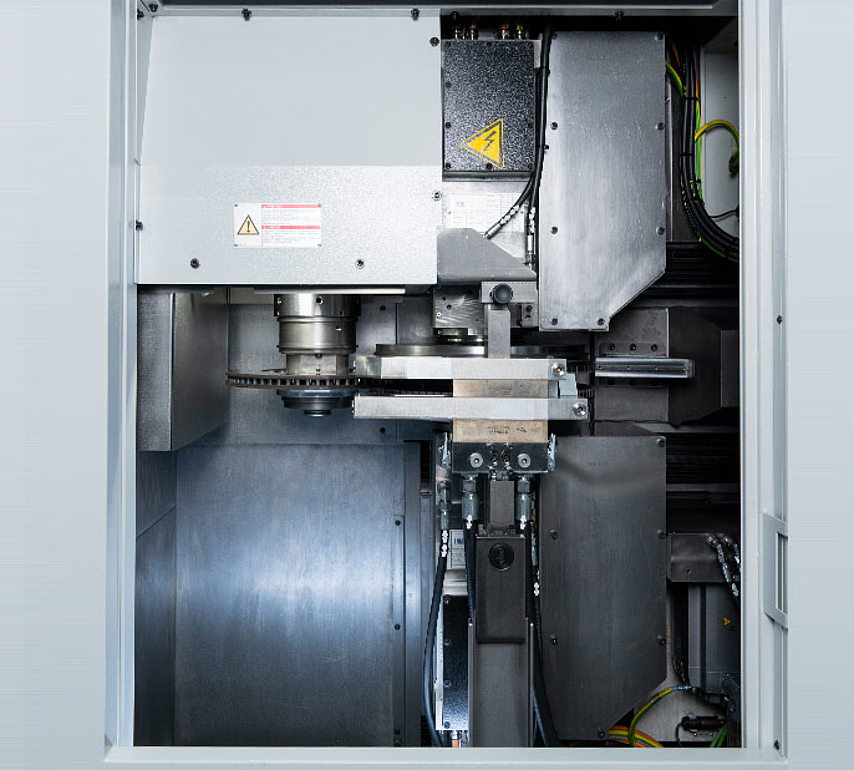
Large work area, vertical design
- Minimizes the accumulation of sanding residue on the workpiece and in the machine
- Excellent accessibility for set-up and maintenance work
- Direct removal of grinding sludge thanks to vertical spindle arrangement
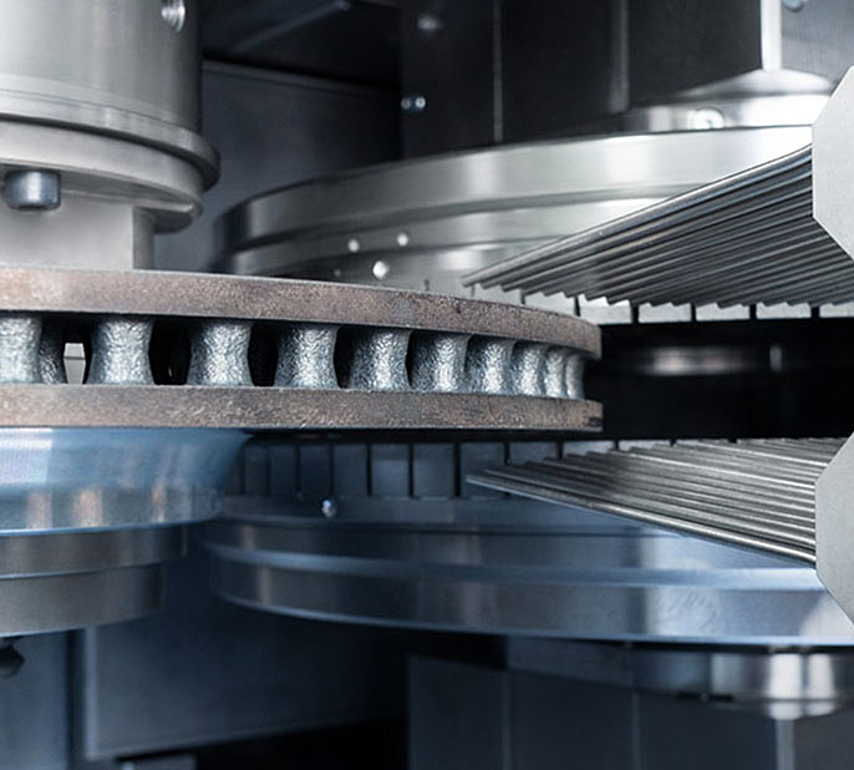
The technology:
Focus on quality with double-sided surface grinding
Cross-ground structures have significantly better tribological running-in behavior than structures in the circumferential direction. Double-sided surface grinding is therefore of central importance. Cross-grinding structures are created perpendicular to the axis of rotation of the grinding wheel.
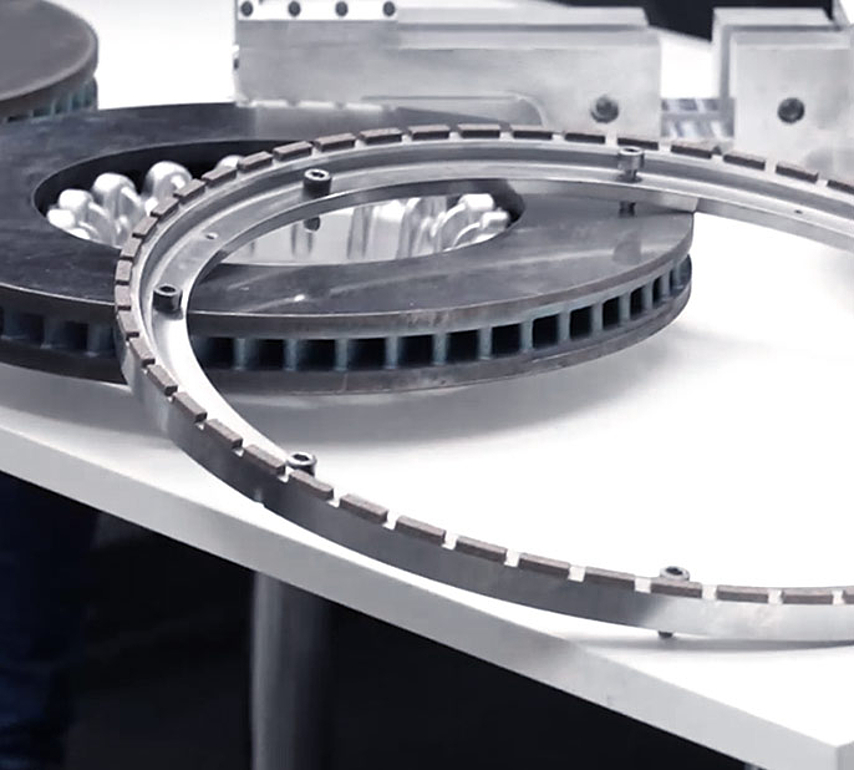
The grinding tool
The VLC 450 DG grinding tool sets new standards in the machining of brake discs. Designed as an interchangeable ring, it is characterized by its low weight of less than five kilograms, which makes it easy to handle. Tool change times are remarkably short at under ten minutes.
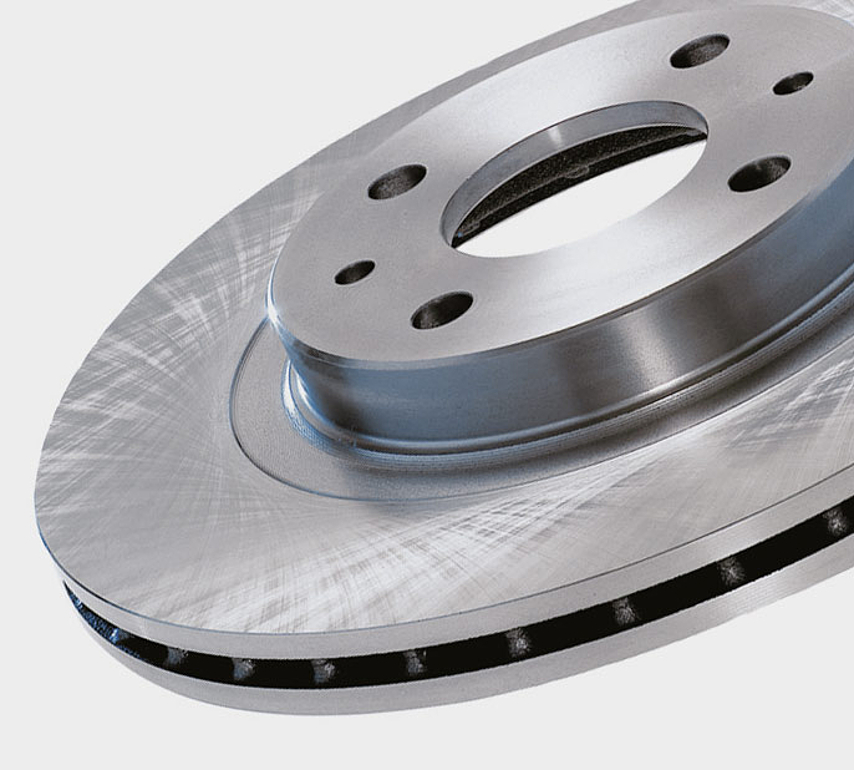
Direct quality control
Direct quality control is made possible by cross-sanding, making it easy to check the machine settings. The progression of the incoming and outgoing grain confirms that all axis angles are set correctly and that the machine delivers geometrically perfect results.
Advantages VLC 450 DG
- Reduce the risk of damage or wear to critical components (guides, measuring systems, etc.); these are located outside the work area.
- Simple link-up and line integration, automation of the loading and unloading process through vertical arrangement
- Good thermal stability of the machine thanks to integrated cooling concept
- Good vibration damping thanks to mineralite machine base
- The process cutting fluids used are a mineral oil-free solution.
Workpieces
The Right Manufacturing Solution for Every Workpiece
Technologies
Complex Manufacturing Systems from a Single Source thanks to a High Range of Technologies
Euro 7 standard mandates lower non-emissions particulate matter - the previous passenger car brake disc is to become obsolete and discontinued model.…