03/13/2024 - Oliver Hagenlocher - Press
EMAG is working on "green manufacturing": Pulling out all the stops for greater energy efficiency
How important is the topic of "climate-neutral production" for industry at this moment? A recent survey conducted by the German Engineering Federation (VDMA) among its member companies provided an impressive answer. According to the survey, more than three quarters of companies have set their own climate targets, with some already measuring the CO2 footprint of their manufactured production equipment. EMAG is currently demonstrating how this value can be significantly reduced with mechanical and electromechanical engineering expertise. A holistic analysis is the first step - especially for older machines.
Images
The objective is as simply formulated as it is demanding in detail: If you want to produce in a climate-neutral way in the future, you need all-round energy-efficient machines that require as little electricity as possible. But how do you reduce the consumption of a complex machine tool and its peripheral devices, in which a large number of processes take place? "There are many detailed answers to this question," explains Konrad Heimbach, Lead Engineer Energy Efficiency at EMAG. "However, we have defined a total of six topics for greater energy efficiency - from choosing the right manufacturing process and machine concept to efficient components, optimizing energy management and establishing AI-based strategies."
It all depends on the process
The first topic - the choice of tool process - already revealed astonishing differences. For example, the southern German specialists at EMAG compared the energy requirements of the three processes "hard turning", "scroll-free turning" and "grinding", whereby the same component was machined with the same objective in each case. The result: The energy requirement per machined volume is extremely different. For example, 663 J/mm3 is required for grinding, 220 J/mm3 for hard turning and only 57 J/mm3 for scroll-free turning. In other words, it is important to keep the energy requirement in mind when selecting a specific process - it makes a huge difference, not least in terms of unit production costs.
Very similar effects can be seen with different machine concepts. Automation, for example, has a massive impact on energy consumption, as each additional workpiece handling requires energy. "Conversely, machines that can be easily integrated into the production flow reduce consumption. We achieve this through integrated parts storage and simple loading and unloading options, for example," explains Heimbach. EMAG solutions that save on external technology are also particularly economical. For example, a Duo machine has only one set of peripheral(s) and therefore consumes less energy than two single machines, each with its own peripheral(s). Comparable energy savings can be achieved by combining several production processes on one machine. On the one hand, this reduces handling costs and requires fewer peripheral devices (each with their own power consumption).
Reduce consumption with a retrofit
Overall, EMAG's analyses and sustainability strategies do not only focus on the development of new machines, as various customer examples under the heading "Retrofit" make clear. "The energy efficiency of older machines is not an immovable status quo. On the contrary, energy consumption can be massively reduced with relatively simple measures," says Heimbach. An impressive example of this is the VTC 250 shaft lathe, which has been in use at a customer since 2008. How great is the energy-saving potential for such a retrofit solution? To answer this question, EMAG first creates an energy flow diagram that details the consumption of the drive system, cooling system, hydraulics and lubrication. In the case of the 15-year old VTC 250, the analysis revealed three areas in which the machine was no longer state of the art: the hydraulic unit, the cooling lubricant pump and the cooling unit. All three units were replaced. The end result is that the user saves around 18,000 kWh per year or 6.7 tons of CO2 . That is more than the annual consumption of two detached houses. Interestingly, the retrofit installation is carried out directly at the customer's premises in only one and a half days and the costs incurred are amortized after around 2.5 years, including the state subsidy.
Focus on individual components
Of particular interest to users of older EMAG machines in this context is a comprehensive study by EMAG on the specific savings potential offered by retrofitting. The machine manufacturers looked at all areas of their production solutions and compared the latest generation of each component with the older technology. The result: Overall, retrofitting can save up to 47 percent of consumption if all measures are taken. The greatest savings potential is found in the area of cooling units (9.6 percent) and hydraulics (8 percent).
In addition, EMAG is currently working extensively on AI-based optimization of the production process. Data should help to increase quality or improve the availability of machines. Users will also be able to keep an eye on the consumption data of their machines at all times using the EMAG Energy Monitor. "As a result, a link can be established between energy data and the condition of the machine, as well as key values such as energy consumption per shift or energy consumption per workpiece. Unusual deviations are immediately apparent and can therefore be rectified more quickly, which ultimately contributes to the energy balance," concludes Heimbach. "We have set the goal for ourselves to use all the levers for sustainable production. The journey has only just begun."
Contact
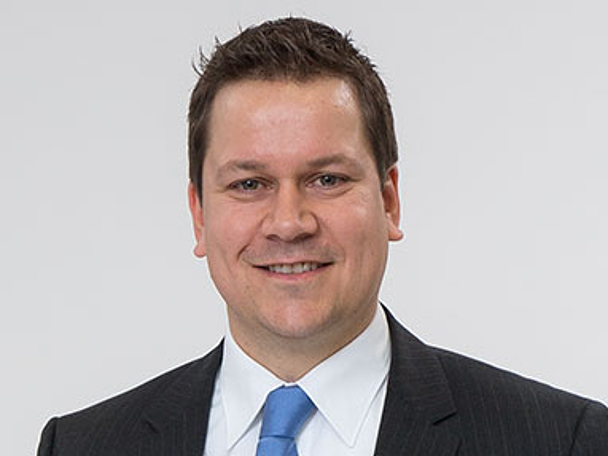
Oliver Hagenlocher
Area
Press and Communication