13.03.2024 - Oliver Hagenlocher - Presse
EMAG arbeitet an der „Grünen Fertigung“: Alle Hebel für mehr Energieeffizienz in Bewegung setzen
Wie wichtig ist aktuell das Thema „klimaneutrale Produktion“ für die Industrie? Eine beeindruckende Antwort ergab zuletzt eine Umfrage des Verbands Deutscher Maschinen- und Anlagenbau (VDMA) unter seinen Mitgliedsfirmen. Demnach haben sich mehr als drei Viertel der Unternehmen eigene Klimaziele gesetzt, wobei einige bereits den CO2-Fußabdruck ihrer hergestellten Produktionsmittel messen. Wie sich dieser Wert gezielt mit Maschinenbau-Know-how verkleinern lässt, zeigt aktuell EMAG auf. Eine ganzheitliche Analyse steht am Anfang – auch und gerade bei älteren Maschinen.
Bilder
Die Zielsetzung ist ebenso einfach formuliert wie anspruchsvoll im Detail: Wer zukünftig klimaneutral produzieren will, benötigt rundum energieeffiziente Maschinen, die möglichst wenig Strom benötigen. Aber wie verringert man den Verbrauch einer komplexen Werkzeugmaschine und ihrer Peripheriegeräte, in denen sich eine Vielzahl von Prozessen abspielen? „Es gibt auf diese Frage viele Detail-Antworten“, erklärt Konrad Heimbach, Lead Engineer Energieeffizienz bei EMAG. „Insgesamt haben wir aber sechs Themenfelder für mehr Energieeffizienz definiert – von der Wahl des richtigen Fertigungsverfahrens und Maschinenkonzepts über effiziente Komponenten bis zur Optimierung von Energiemanagement und der Etablierung von KI-basierten Strategien.“
Auf das Verfahren kommt es an
Bereits beim ersten Themenfeld – der Wahl des Werkzeugverfahrens – zeigen sich dabei erstaunliche Unterschiede. So haben die süddeutschen Spezialisten beispielsweise den Energiebedarf der drei Verfahren „Hartdrehen“, „Schäldrehen“ und „Schleifen“ miteinander verglichen, wobei jeweils das gleiche Bauteil mit der gleichen Zielsetzung bearbeitet wurde. Ergebnis: Der auftretende Energiebedarf pro zerspantes Volumen ist extrem unterschiedlich. So benötigt man für das Schleifen 663 J/mm3, für das Hartdrehen 220 J/mm3 und für das Schäldrehen sogar nur 57 J/mm3. Mit anderen Worten heißt das: Bei bestimmten Aufgaben sollte man den Energiebedarf unbedingt im Blick behalten, wenn das Verfahren ausgewählt wird – es macht einen riesigen Unterschied, der nicht zuletzt auch die Stückkosten beeinflusst.
Ganz ähnliche Effekte zeigen sich bei unterschiedlichen Maschinenkonzepten. Gerade die Automatisierbarkeit beeinflusst den Energieverbrauch dabei massiv, denn jedes zusätzliche Werkstück-Handling benötigt Energie. „Im Umkehrschluss sorgen Maschinen, die sich einfach in den Produktionsfluss integrieren lassen, für einen sinkenden Verbrauch. Wir erreichen das etwa durch integrierte Teilespeicher und einfache Be- und Entladungsmöglichkeiten“, erläutert Heimbach. Besonders sparsam sind darüber hinaus EMAG Lösungen, bei denen externe Technologie eingespart wird. So hat etwa eine Duo-Maschine nur einen Satz Peripheriegeräte und verbraucht somit weniger Energie als zwei Single-Maschinen mit jeweils eigener Peripherie. Vergleichbare Energieeinsparungen zeigen sich, wenn man mehrere Fertigungsverfahren auf einer Maschine kombiniert. Dann sinkt zum einen der Aufwand rund um das Handling ab und man benötigt weniger Peripheriegeräte (mit jeweils eigenem Stromverbrauch).
Runter mit dem Verbrauch per Retrofit
Insgesamt hat EMAG bei seinen Analysen und Nachhaltigkeitsstrategien nicht nur die Neuentwicklung von Maschinen im Blick, wie verschiedene Kundenbeispiele unter der Überschrift „Retrofit“ deutlich machen. „Die Energieeffizienz von älteren Maschinen ist kein unverrückbarer Status Quo – im Gegenteil: Mit relativ einfachen Maßnahmen lassen sich die Verbräuche massiv senken“, sagt dazu Heimbach. Beeindruckend ist hier etwa das Beispiel der Wellen-Drehmaschine VTC 250, die bei einem Kunden seit 2008 im Einsatz ist. Wie groß sind die Energieeinsparpotenziale einer solchen Lösung? Um darauf eine Antwort geben zu können, erstellt EMAG zunächst ein sogenanntes Energieflussdiagramm, das die Verbräuche von Antriebsverbund, Kühlung, Hydraulik und Schmierung detailliert offenlegt. Im Fall der rund 15 Jahre alten VTC 250 zeigte die Untersuchung drei Bereiche auf, in denen die Maschine nicht mehr auf dem Stand der Technik ist: Hydraulikaggregat, KSS-Pumpe und Kühlaggregat. Alle drei Einheiten wurden getauscht. Im Endergebnis spart der Anwender rund 18.000 kWh pro Jahr oder 6,7 Tonnen CO2 ein. Das ist mehr als der Verbrauch von zwei Einfamilienhäusern pro Jahr. Interessant ist dabei, dass der Einbau direkt beim Kunden erfolgt und nur eineinhalb Tage dauert. Die anfallenden Kosten amortisieren sich im Beispielfall bereits nach rund 2,5 Jahren inklusive staatlicher Förderung.
Einzelne Komponenten im Fokus
Interessant ist in diesem Zusammenhang gerade für die Nutzer von älteren EMAG Maschinen eine umfassende Studie von EMAG zu den konkreten Einsparpotenzialen per Retrofit. Die Maschinenbauer haben sich alle Bereiche ihrer Produktionslösungen angeschaut und die jeweils neueste Generation einer Komponente mit der jeweils älteren Technologie verglichen. Ergebnis: Insgesamt lassen sich per Retrofit bis zu 47 Prozent des Verbrauchs einsparen, wenn man alle Maßnahmen ergreift. Das größte Einsparpotenzial offenbart sich dabei im Bereich von Kühlgeräten (9,6 Prozent) und der Hydraulik (8 Prozent). Darüber hinaus arbeitet EMAG gerade sehr umfangreich an der KI-basierten Optimierung des Fertigungsprozesses. Daten sollen dabei mithelfen, die Qualität zu steigern oder die Verfügbarkeit der Maschinen zu verbessern. Außerdem sollen Anwender die Verbrauchsdaten ihrer Maschinen per Energy Monitor immer im Blick behalten. „In der Folge kann man einen Bezug herstellen zwischen Energiedaten und dem Zustand der Maschine sowie Kennwerte bilden wie den Energieverbrauch pro Schicht oder den Energieverbrauch pro Werkstück. Unübliche Abweichungen fallen direkt auf und werden somit schneller abgestellt, was am Ende wieder in die Energiebilanz einzahlt“, erklärt Heimbach abschließend. „Wir haben uns zum Ziel gesetzt, alle Stellschrauben für eine nachhaltige Produktion zu nutzen. Der Weg hat gerade erst begonnen.“
Ansprechpartner
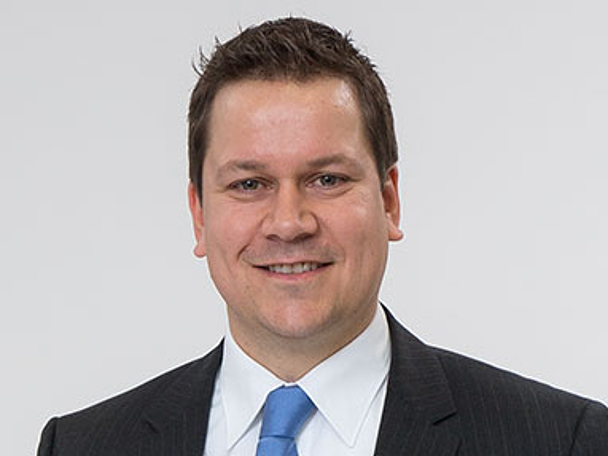
Oliver Hagenlocher
Bereich
Presse und Kommunikation