09/01/2020 - Oliver Hagenlocher - Press
VMC 450-5 MT Turning/Milling Center – Five Axes for Dramatically Shorter Machining Processes in the Production of Large Parts
Large components and complex geometries—in heavy machining, this combination is far from rare and is always synonymous with a high expenditure of time and rising costs. A primary reason for this is that the variety of machining processes required, from turning to gear cutting, are typically performed on different machines that are not completely linked with one another. Additionally, the variety of parts required at production sites is continuing to grow, meaning that different components must be processed on the machines all the time. As a result, the time required for operators to set up the machines continues to increase. With its VMC 450-5 MT vertical turning/milling center, EMAG Leipzig provides an impressive solution to break this cycle: All turning, milling, drilling and gear cutting processes are performed on a single machine, in one machining area. To achieve this, the machine is equipped with five axes – resulting in shorter throughput times, and minimizing the retooling effort, leading to improved component quality and diversity.
Images
A variety of applications are possible on the VMC 450-5 MT, including very large components for utility vehicles and industrial transmissions in shipbuilding, and railway construction or components for the agricultural and mining industries. Some of these components require several directional boreholes and surfaces or gearing that needs to be produced very precisely and free of faults. Additionally, a number of production sites require that the machinery is capable of producing a large variety of different versions of the component, quickly. Therefore, production planners are looking for a flexible solution that requires minimal effort in terms of set-up. The VMC 450-5 MT was developed to meet these challenges, as Georg Händel, Manager of Technical Sales “Heavy Parts” at EMAG, explains. “We rely on this multifunctional turning/milling center with five axes to develop production solutions for complex components with a maximum diameter of 450 millimeters (18 in). For this, turning is always the machine's main technology. The bottom-mounted, maintenance-free workpiece spindle is integrated in the newly developed, generously dimensioned Y-axis. Also available is a B-axis with a swivel angle of 195 degrees the includes the integrated turning/milling spindle. This swivel angle allows for the attachment of an additional stationary tool socket to the B-axis. With this system, maximum removal rates can be achieved in heavy machining even with interrupted cuts. The tool socket can be loaded by the tool magazine. The combination of axes allows for hobbing or skiving applications to be performed as well.” Turning, milling, drilling and gear cutting—all the technologies required to manufacture a complex component are included in the VMC 450-5 MT.
Planetary Carriers: From Six Machines to Three
The production of planetary carriers is the perfect example to demonstrate the advantages that this approach provides. Traditionally, this key transmission component in heavy machining runs through six different machines that are not completely linked—starting with two turning operations, continuing with broaching/gear hobbing and finishing with drilling and balancing. This means that the operator needs to retool six different machines at every batch change – negatively impacting the process reliability and productivity. Additionally, the entire production process is relatively slow and inflexible, because the component must always be transported to the next machine with a forklift.
However, the situation is very different when using the VMC 450-5 MT: During the main machining operation, the planetary carrier will now only run through two machines that are automated with a robot. The turning, drilling, milling and power skiving machining processes are flexibly distributed across two machines. The end result is a balanced process time and very high output rates. Of course, the balancing machine is also integrated into the EMAG automation cell. Workpiece labeling and cleaning can be performed simultaneously, so now the component is only picked up three times instead of six. ”Users benefit at all levels with this approach,” says Händel. “The low number of clamping operations improves component quality and process reliability. Given the perfectly coordinated machine operating cycles, downtimes are minimized and even energy consumption is dramatically reduced. We also include several measuring systems that provide for consistent quality management throughout the machining process. This allows us to produce planetary carriers more precisely, in less time, more economically and cost-effectively.” The tool magazine with up to 80 tool posts also plays an important role in production. It can store all the tools or twin tools (in case of wear) required for a variety of different component variants. The tool change is performed automatically and that is why the operator only needs to replace the clamping jaws when retooling—and that is done on the front of the machine, while a robot keeps loading workpieces through a side door without any downtime of the machine or line.
Customized Configuration
EMAG customizes the VMC 450-5 MT to fit the customer's preference from its standard modular system. For example, a variety of spindle versions, specific workpiece carriers or a tailstock options are available. That is why the VMC 450-5 MT truly is an all-purpose solution for a wide variety of workpieces. In addition, all EMAG customers benefit from a production solution with a small footprint. After all, the entire production process requires far fewer machines. “We’re breaking new ground with this 5-axis turning/milling center,” concludes Händel. “The machine was specifically designed with the goal to enable complete machining, including power skiving or gear hobbing, within heavy machining. This approach achieves significant gains in productivity. Regardless of whether the part is for trucks, construction and agricultural machines or even the aerospace industry—there is almost no industry that would not benefit from such a comprehensive machine construction package.”
Downloads
Contact
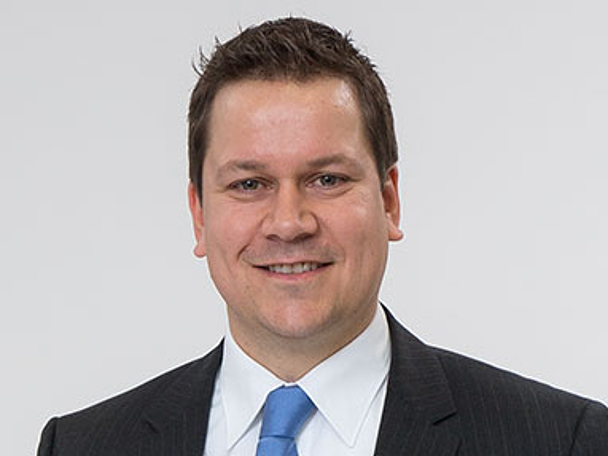
Oliver Hagenlocher
Area
Press and Communication