01/09/2020 - Oliver Hagenlocher - Stampa
Centro di tornitura/fresatura VMC 450-5 MT – cinque assi
Componenti di grandi dimensioni e geometrie complesse: questa combinazione non è una rarità ed è sempre sinonimo di tempi elevati e aumento dei costi. Il motivo risiede nel fatto che i diversi processi di lavorazione, dalla tornitura alla dentatura, vengono spesso eseguiti su macchine diverse non concatenate in modo completo le une alle altre. A ciò si aggiunge l’aumento del numero di lotti da lavorare negli stabilimenti di produzione. Ovvero la necessità di lavorare componenti sempre diversi sulle varie macchine. Di conseguenza, i tempi richiesti per il riattrezzamento da parte dell’operatore sono sempre maggiori. Con il centro di tornitura/fresatura VMC 450-5 MT, EMAG Leipzig Maschinenfabrik tutti i processi di tornitura, fresatura, alesatura e dentatura vengono eseguiti in un’unica zona di lavoro grazie ai 5 assi con i quali è equipaggiata la macchina. Il risultato sono tempi ciclo più brevi e costi di equipaggiamento minimi, accompagnati da un aumento della qualità.
Immagini
Le possibilità di applicazione della VMC 450-5 MT sono numerose in quanto, da un lato, molti pezzi su larga scala destinati a veicoli commerciali o trasmissioni industriali, ai settori della cantieristica, dell’agricoltura ed estrattivo sono eccezionalmente complessi. Presentano ad esempio numerosi fori, superfici o dentature inclinati che devono essere realizzati con estrema precisione e senza errori. Dall’altro in molti stabilimenti di produzione vengono realizzate rapidamente diverse varianti dei componenti. I pianificatori della produzione sono quindi alla ricerca di soluzioni flessibili con costi di equipaggiamento ridotti. La VMC 450-5 MT è stata appositamente sviluppata per queste esigenze, come spiega Georg Händel, Manager Technical Sales “Heavy Parts” presso EMAG. “Con lo sviluppo di soluzioni di produzione per componenti complessi con diametro fino a 450 mm ci siamo affidati a questo centro di tornitura/fresatura multifunzionale a cinque assi. La tornitura rappresenta sempre la tecnologia produttiva principale. Il mandrino portapezzo posizionato in basso, esente da manutenzione, è integrato nel nuovo asse Y. È inoltre disponibile un asse B con angolo di rotazione di 195° con mandrino di tornitura/fresatura integrato. Questo angolo di rotazione permette di collocare un portautensili aggiuntivo fisso sull’asse B. Ciò consente di ottenere le massime velocità di asportazione nella lavorazione pesante ad asportazione di truciolo, anche nel taglio interrotto. Il portautensili può essere caricato attraverso il magazzino utensili. La combinazione degli assi consente di eseguire applicazioni per la dentatura a creatore oppure il power skiving.” Tornitura, fresatura, alesatura e dentatura senza compromessi – sulla VMC 450-5 MT sono presenti tutte le tecnologie necessarie per la realizzazione di un componente complesso.
Portasatelliti: sei macchine diventano tre
L’ottimo esempio del portasatelliti mostra quali vantaggi offra sul piano pratico questo approccio. Nella lavorazione pesante ad asportazione truciolo, in genere questo componente centrale del cambio passa attraverso sei diverse macchine che non sono concatenate in modo completo – dai due processi iniziali di tornitura alla brocciatura/dentatura a creatore fino all’alesatura e all’equilibratura finali. Quando si esegue un cambio lotto, l’operatore deve quindi preparare sei macchine diverse, pertanto la sicurezza di processo e la produttività ne risentono. Inoltre l’intero processo è relativamente lungo e poco flessibile perché i componenti devono essere trasportati alla macchina successiva mediante carrello elevatore.
La situazione cambia se si utilizza la VMC 450-5 MT: durante la lavorazione principale il portasatelliti passerà solo attraverso due macchine, automatizzate con un robot. I processi di lavorazione tornitura, alesatura, fresatura e power skiving vengono ripartiti in modo flessibile su entrambe le macchine. ll risultato è un tempo di lavorazione compensato e un elevatissimo rendimento. L'equilibratrice viene ovviamente integrata nella cella di automazione EMAG. La marcatura e il lavaggio dei pezzi possono essere eseguiti parallelamente. Nel complesso, il componente viene prelevato solo tre volte (invece delle sei precedenti). “Gli utilizzatori beneficiano di questo approccio a tutti i livelli”, afferma Händel. “Il numero limitato di fasi di serraggio fa aumentare la qualità dei componenti e la sicurezza di processo, i tempi di inattività sono ridotti al minimo grazie a una sincronizzazione delle macchine perfettamente coordinate e anche il consumo energetico è notevolmente inferiore. Inoltre diversi sistemi di misura garantiscono una gestione continua della qualità. Questo significa che la produzione viene eseguita in modo più preciso, rapido ed economico e quindi nel complesso con costi inferiori.” Non da ultimo, il magazzino utensili con fino a 80 posizioni riveste un ruolo di primo piano. Qui è possibile depositare tutti gli utensili e gli utensili gemelli (in caso di usura) necessari per numerose varianti dei componenti. Il cambio utensili viene eseguito in modo automatico, quindi durante il riattrezzamento l’operatore deve sostituire solo le griffe. Questa operazione viene effettuata dal lato anteriore, mentre il caricamento dei pezzi tramite robot può proseguire senza fermi macchina o fermi linea attraverso un portello laterale.
Configurazione personalizzata
Nel complesso EMAG configura la VMC 450-5 MT in modo personalizzato in base alle richieste del cliente partendo dalla struttura modulare standard. Sono ad esempio disponibili diverse varianti di mandrino, portapezzi specifici oppure una contropunta. Per queste ragioni la VMC 450-5 MT rappresenta una vera soluzione multifunzionale per i più svariati pezzi. Inoltre i clienti EMAG beneficiano sempre di una soluzione produttiva con un ingombro ridotto. Infine, l’intero processo di produzione richiede molte meno macchine. “Con questo centro di tornitura/fresatura a 5 assi creiamo il futuro”, conclude Händel. “La macchina è stata espressamente concepita con l’obiettivo di consentire una lavorazione completa inclusi dentatura a creatore o power skiving. Questo approccio assicura un aumento della produttività. Che si debbano produrre pezzi per automezzi pesanti, per macchine edili e agricole oppure per l’industria aeronautica – non esistono praticamente settori che non beneficino di questo pacchetto completo per l’industria meccanica.”
Download
Referenti
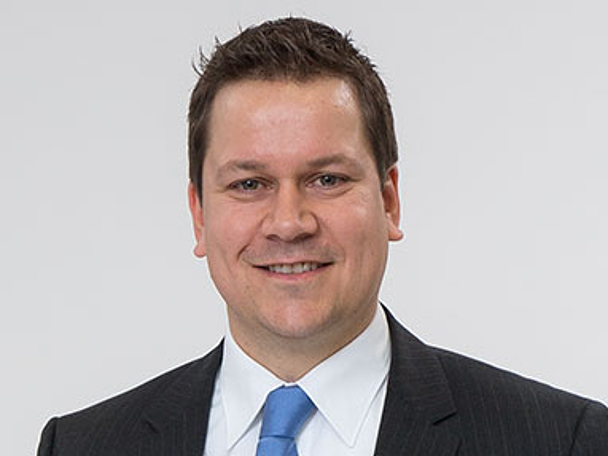
Oliver Hagenlocher
Zona
Press and Communication