08/06/2019 - Oliver Hagenlocher - Press
EMO 2019 – Complete Production Solutions with the VL 1 TWIN: Massively reduce unit costs for planetary and bevel gears
Cost pressure, high quality requirements and demand for huge output volumes—extremes collide in automotive transmission manufacturing. While meeting these demands, production quantities will also projected to continue to rise in the coming years. The authors of the current “Shell Pkw-Szenarien” (Shell Automotive Scenarios) estimate that the global car fleet could more than double to 2.5 billion vehicles by 2050. Consequently, the cost per piece almost inevitably moves as a primary focus for production planners: How can commonly mass-produced transmission components, such as planetary and bevel gears, be produced even more efficiently? The EMAG Group provides a customized answer to this question with the development of the twin-spindle pick-up turning center VL 1 TWIN. It machines two identical components simultaneously in the same machining area. This technology opens up a wide range of possibilities: When two machines are integrated into a line, the planetary gear can be machined from two sides—and all that within shorter cycle times. What exactly does the line solution for planetary and bevel gears look like?
Images
Producing up to one million planetary gears per year at a single production site is no rarity—simply looking at how the component is implemented into an automatic torque converter gives us the answer, since the corresponding planetary transmission mechanism generally consists of four sets of planetary gears with three planetary gears and one sun gear each. This amounts to a total of 16 gears. Another interesting point is that automatic torque converters are currently increasing in importance in the market. A primary reason for this is that they are still considered to be a more comfortable, compact and robust transmission solution. Secondly, some manufacturers rely on the technology for the design of modern hybrid drives. “The reason for developing the VL 1 TWIN becomes clearer with this information. Lower costs for the production of planetary and bevel gears were a primary concern during development,” explains Björn Svatek, Sales & Marketing Director Modular Solutions at EMAG. “That’s why we’re betting on the simultaneous machining of two identical components in a single machining area with this twin-spindle machine. This process will result in high output volumes with short lead times. Rigorous cost control has also allowed us to reduce the price per spindle considerably, which contributes to a low cost per piece.”
Planetary Gear: Two Finished Parts Every 20 Seconds
What exactly does a VL 1 TWIN line solution for soft machining of planetary gears look like? The process is generally run on two machines that are connected via a TrackMotion automation system. The associated TransLift (a lifting and rotating tool with an electric gripper) simultaneously picks up two raw parts from the conveyor and transports them to the first machine. The VL 1 TWIN’s two pick-up spindles then take over and move the components into the machining area. The turning operation follows on the first side of the inside and outside diameters (OP 10 – OP 10). The diameter and length (X/Z directions) of both workpieces can be adjusted independently of each other, since the headstocks can traverse autonomously. This is particularly important after a tool change to compensate for deviations (e.g. after replacing the indexable inserts). Once the two semi-finished components have been transported out of the machine compartment, the TransLift takes over again, turning the parts by 180 degrees and transporting them to the second VL 1 TWIN. This is where the second side of the outside diameter is face-turned (OP 20 – OP 20). The TrackMotion automation system then places the finished component on the conveyor belt, which can hold up to 400 finished parts on the integrated stacker units. The overall process is completed within about 20 seconds for two components. The average chip-to-chip time is just under 5 seconds. This tremendous pace is made possible by a series of technical configuration details: The two pick-up spindles feature high power values of 9.9 kW (13 hp) and 136 Nm (100 ft-lbs) at 40% duty cycle. At the same time, the wear-free linear drive in the X-axis (in combination with the direct distance measuring systems) has a high acceleration of 8 m/s2 (26 ft/s2) — including long-term accuracy. This allows for controlled manufacturing of the frequently required H6 fits of the main drill hole.
Bevel Gear: Drilling, Roughing and Finishing in a Single Machine
Due to the rising cost pressure for the production of bevel gears, all the processes must be executed with high efficiency—in this case, manufacturing with a forging process provides certain advantages: Modern manufactured bevel gears frequently leave the forge with already finish-machined bevel gear teeth. A turning process performed in a single clamping operation therefore is all that is required. This is where EMAG offers the optimal solution for parallel soft machining on two bevel gear blanks (OP 10 – OP 10) with its VL 1 TWIN. Four machining steps are executed consecutively in the machine and the full cycle time is only 25 seconds: Once the blanks are fed via TrackMotion or using a pick-up spindle, the central bore hole of the component is produced with a drilling process performed on the solid material, following which the rough-machining of the cup is initiated. The finishing of the bore hole and cup is performed in the third and fourth steps. A special clamping solution reproduces the negative image of the component’s gearing and holds it firmly in place the entire time. Considering the massive drilling process, the MINERALIT® polymer machine base is particularly important, since the polymer concrete reduces vibrations during the drilling process and ensures that the highest precision is achieved. A measuring system offered as an option to measure the workpiece between the machining area and the pick-up stations increases process reliability. It is also possible to link two VL 1 TWINs with just one TrackMotion system and then execute the same process in the machines (OP 10 – OP 10, OP 10 – OP 10). The fact that the TrackMotion gripper travels at a speed of up to 150 meters (492 ft) per minute and that it handles the travel to and from the TWIN machines working in parallel is crucial in this context.
Perfect Solution for Transmission Manufacturing
Overall, the TWIN approach allows for great increases in productivity for a whole series of components—from cam elements to bearing rings, all the way to flanges. Depending on the requirements, multi-technology production lines can be created that include things such as EMAG hobbing and deburring machines, for example. “We are convinced that the VL 1 TWIN is a perfect solution for the growing unit volumes and the increasing competition in transmission manufacturing,” says Björn Svatek. “Users benefit from lower unit costs, shorter cycle times and high process reliability. We want these advantages to play a stronger role in the market.”
The VL 1 TWIN live at the EMO 2019
Contact
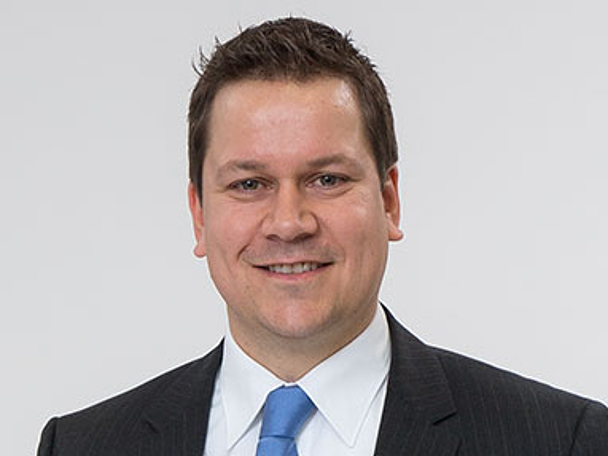
Oliver Hagenlocher
Area
Press and Communication