06/08/2019 - Oliver Hagenlocher - Stampa
EMO 2019 – Soluzioni in linea con il VL 1 TWIN: I costi per pezzo per ingranaggi planetari o ingranaggi conici si abbassano notevolmente
Pressione sui costi, elevati standard qualitativi e, non da ultimo, enormi quantità di pezzi – nella produzione di trasmissioni per l’industria automobilistica si contrappongono requisiti decisamente estremi. I volumi di produzione sono inoltre destinati ad aumentare nei prossimi anni. Secondo gli autori dell’attuale “Shell Pkw-Szenarien”, un noto studio di settore elaborato da Shell, entro il 2050 il parco auto mondiale potrebbe più che raddoppiare, arrivando a circa 2,5 miliardi di veicoli. È quasi inevitabile che i costi per pezzo siano al centro dell’attenzione dei pianificatori della produzione. Il problema è il seguente: come si possono produrre componenti tipici delle trasmissioni realizzati in serie come ingranaggi planetari o ingranaggi conici in modo sempre più efficiente? Il Gruppo EMAG fornisce una risposta adeguata a questa domanda sviluppando il centro di tornitura pick-up a doppio mandrino VL 1 TWIN. Questa soluzione consente di lavorare simultaneamente due componenti uguali nella stessa area di lavoro. Partendo da queste basi tecniche si aprono grandi opportunità: collegando due macchine in una linea è possibile eseguire la lavorazione dell’ingranaggio planetario da due lati – e con tempi di ciclo ridotti. In che cosa consiste esattamente una soluzione in linea per ingranaggi planetari o ingranaggi conici?
Immagini
Non è infrequente che in alcuni stabilimenti di produzione vengano realizzati ogni anno fino a un milione di ingranaggi planetari. Un semplice sguardo all’utilizzo dei componenti in un cosiddetto cambio automatico con convertitore di coppia ci spiega il perché, in quanto il corrispondente rotismo epicicloidale è in genere composto da quattro gruppi epicicloidali, ciascuno con tre ingranaggi planetari e una ruota planetaria. In totale si tratta quindi di 16 ingranaggi. È inoltre interessante il fatto che il cambio automatico con convertitore di coppia stia attualmente acquisendo una nuova importanza. Da un lato, questa soluzione per la trasmissione è tuttora più compatta, robusta e garantisce un maggiore comfort; dall’altro, alcuni produttori scelgono questa tecnologia anche per la progettazione di moderni propulsori ibridi. “Lo sviluppo del VL 1 TWIN si spiega in quest’ottica. La riduzione dei costi di produzione di ingranaggi planetari e ingranaggi conici è stata una priorità”, spiega Björn Svatek, Direttore vendite e marketing Modular Solutions presso EMAG. “Per questa ragione, con questa macchina a doppio mandrino abbiamo optato per una lavorazione simultanea di due componenti uguali nella stessa area di lavoro. Questa soluzione offre un rendimento elevato in tempi brevi. D’altro canto, un monitoraggio coerente dei costi ci ha consentito di ridurre notevolmente il costo per mandrino. Ciò contribuisce a costi per pezzo ridotti.”
Ingranaggio planetario: due pezzi finiti ogni 20 secondi
In che cosa consiste una possibile soluzione in linea VL-1-TWIN per la lavorazione su non temprato di ingranaggi planetari? Il processo viene essenzialmente completato in due macchine collegate attraverso il sistema di automazione TrackMotion. In questo caso il corrispondente TransLift (un carrello sollevatore ribaltatore con pinza elettrica) preleva contemporaneamente due pezzi grezzi dal nastro di alimentazione e li trasporta sulla prima macchina. I due mandrini pick-up della VL 1 TWIN ricevono i pezzi e li trasferiscono nell’area di lavoro. Segue la lavorazione di tornitura del primo lato del diametro interno ed esterno (OP 10 – OP 10). Diametro e lunghezza (direzione X/Z) dei due componenti possono essere corretti in modo indipendente l'uno dall'altra, perché le teste portamandrino sono in grado di traslare in modo indipendente tra loro. Questo è importante soprattutto dopo un cambio utensili per compensare scostamenti (ad esempio dopo il cambio degli inserti). Dopo il loro trasporto all’esterno dell’area di lavoro, il TransLift ruota i due componenti semilavorati di 180 gradi e li trasporta all’altro VL 1 TWIN. Qui viene eseguita la tornitura in piano del secondo lato del diametro esterno (OP 20 – OP 20). Al termine, mediante TrackMotion il componente finito passa sul nastro di sosta, che è in grado di prelevare fino a 400 pezzi finiti sulle unità degli impilatori integrate. Il processo completo viene terminato con un tempo di ciclo di circa 20 secondi per due componenti. Il tempo truciolo/truciolo è pari in media a soli 5 secondi. Questa enorme velocità è permessa da una serie di elementi tecnici della dotazione. I due mandrini pick-up presentano elevati valori di azionamento di 9,9 kW e 136 Nm a 40% rapp. inserzione. Allo stesso tempo, l’azionamento lineare resistente all’usura sull’asse X (in combinazione con sistemi di misurazione diretta della corsa) è caratterizzato da un’ accelerazione di 8 m/s2 – con una precisione elevata. In questo modo è possibile realizzare con sicurezza di processo gli accoppiamenti H6 del foro principale spesso richiesti.
Ingranaggio conico: alesatura, sgrossatura e finitura in un’unica macchina
A causa dell’aumento della pressione sui costi di produzione degli ingranaggi conici, tutti i processi devono avvenire con maggiore efficienza – la realizzazione tramite processo di forgiatura presenta in questo caso alcuni vantaggi: i moderni ingranaggi conici finiti lasciano spesso la fucina con una dentatura per ingranaggi conici già “rifinita”. In questo caso è necessario un solo processo di tornitura in una fase di serraggio. Con il tornio VL 1 TWIN, EMAG offre la soluzione ottimale per la lavorazione su non temprato parallela di due pezzi grezzi per la produzione di ingranaggi conici (OP 10 – OP 10). Le fasi di lavorazione vengono eseguite in successione nella macchina con un tempo di ciclo pari a soli 25 secondi: dopo l’alimentazione tramite TrackMotion o mandrino pick-up ha luogo l’alesatura centrale del componente mediante processo di foratura “dal pieno”, seguita dalla sgrossatura della calotta. Nella terza e quarta fase viene eseguita la finitura del foro e della calotta. Una speciale soluzione di serraggio riproduce in negativo la dentatura del componente e lo mantiene stabilmente in posizione per tutto il tempo. Per quanto riguarda il processo di foratura dal pieno, il basamento in Mineralit® è di fondamentale importanza, in quanto il cemento polimerico riduce le vibrazioni durante il processo di foratura, garantendo una maggiore precisione. Un sistema di misura – disponibile come opzione – per la misurazione dei pezzi tra l’area di lavoro e le stazioni pick-up aumenta inoltre la sicurezza di processo. È fondamentalmente possibile concatenare anche due VL 1 TWIN con un solo sistema TrackMotion e completare quindi lo stesso processo nelle due macchine (OP 10 – OP 10, OP 10 – OP 10). In questo caso è determinante che la pinza del TrackMotionsi muova con una velocità fino a150 metri al minuto e garantisca l’alimentazione e la rimozione del pezzo dalle macchine TWIN che lavorano in parallelo.
Soluzione perfetta per la produzione di trasmissioni
Nel complesso, l’approccio TWIN garantisce un notevole aumento di produttività per una serie di altri componenti – da segmenti a camme ad anelli di cuscinetti e flange. A seconda delle esigenze vengono realizzate linee di produzione multitecnologiche, a cui appartengono ad esempio anche dentatrici a creatore e sbavatrici EMAG. “Siamo convinti che il tornio VL 1 TWIN rappresenti una soluzione perfetta per l’aumento dei volumi produttivi e la crescente concorrenza nella produzione di trasmissioni”, afferma Björn Svatek. "Gli utilizzatori possono beneficiare di una riduzione dei costi, tempi di ciclo ridotti ed elevata sicurezza di processo. Intendiamo puntare sempre di più su questi vantaggi all’interno del mercato.”
Il tornio VL 1 TWIN dal vivo alla EMO 2019
Referenti
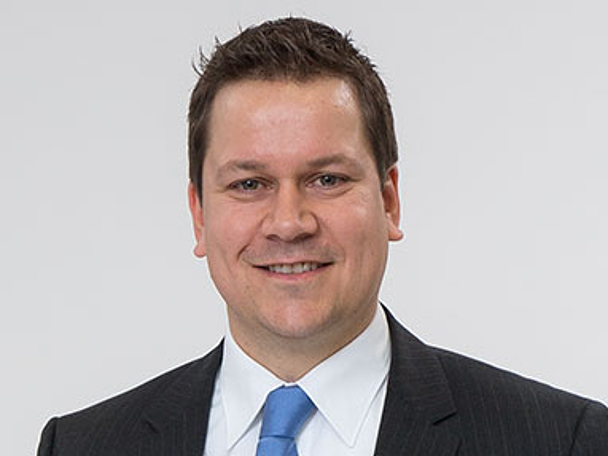
Oliver Hagenlocher
Zona
Press and Communication