08/06/2019 - Oliver Hagenlocher - 보도자료
EMO 2019 - VL 1 TWIN 장착 라인 솔루션: 유성 기어 또는 베벨 기어의 단가를 혁신적으로 절감하다
비용 압박, 높은 품질 요구 사항, 그리고 특히 그 무엇보다 엄청난 양 - 승용차 기어 제작에서는 이러한 극한 상황들이 서로 부딪칩니다. 여기에 심지어 앞으로 몇 년 후 생산량이 더 증가할 것으로 예상됩니다. 이에 따라 최신 “Shell 승용차 시나리오"의 저자들은 꽤 높은 가능성으로 전 세계 승용차의 수가 2050년까지 25억대로, 즉 2배 넘게 늘 것이라 예상합니다. 이 상황에서 거의 필연적으로 ‘생산 단가(Cost per piece)’가 생산 계획자의 주요 관심사가 됩니다: 유성 기어나 베벨 기어 같이 변속기와 관련하여 대량으로 생산되는 대표적인 부품을 어떻게 보다 더 효율적으로 생산할 수 있을까요? EMAG 그룹은 이중 스핀들 픽업 선반 VL 1 TWIN을 개발함으로써 이러한 질문에 대한 맞춤형 솔루션을 제시합니다. 이 픽업 선반은 단 하나의 작업 공간 내에서 두 개의 동일한 부품을 동시에 가공합니다. 이러한 기술을 기반으로 하여 폭넓은 가능성이 열립니다: 장비 두 대가 한 라인에 연결된다면, 짧은 사이클 타임으로 양측에서 유성 기어 가공이 가능해집니다. 유성 기어 또는 베벨 기어에 대한 라인 솔루션은 정확히 무엇일까요?
이미지
유성 기어를 한 생산 현장에 연간 백만 개 까지 생산하는 것은 드문 일이 아닙니다. 이미 소위 말하는 자동 변속기에서 부품의 사용에 대해 잠깐 생각해보면 이를 이해할 수 있습니다. 왜냐하면 이에 속하는 유성 변속기는 대부분 각각 세 개의 유성 기어와 한 개의 선 기어를 포함하는 네 개의 유성 기어 세트로 이루어져 있기 때문입니다. 즉 여기에 총 16개의 유성 기어가 존재합니다. 더 나아가 흥미로운 점은 그 자동 변속 장치의 중요성이 최근 새로이 대두된다는 것 입니다. 이러한 자동 변속기는 전과 마찬가지로 편리하고 컴팩트하면서도 견고한 기어 솔루션입니다. 또한 몇몇 생산업체도 현대식 하이브리드 기어 생산 시 이 기술을 적용하고 있습니다. “VL 1 TWIN 개발에는 이러한 배경이 숨겨 져 있습니다. 유성 기어와 베벨 기어의 생산 시 비용 절감에 가장 주력했습니다”라고 비욘 스바텍(Björn Svatek) EMAG의 모듈식 솔루션 영업 및 마케팅 담당자는 설명합니다. “따라서 이 이중 스핀들 장비의 경우 한 작업 공간에서 두 개의 동일한 부품을 동시에 가공하는 데 사용합니다. 이는 짧은 시간에 높은 생산량을 이끌어 냅니다. 다른 한 편으로, 우리는 일관된 비용 관리를 통해 스핀들 당 가격을 현저히 낮추었습니다. 이를 통해 낮은 ‘생산 단가’가 가능해 집니다.”
유성 기어: 20초 당 두 개의 완성 부품
앞선 유성 기어의 연질 가공용으로 가능한 VL-1 TWIN 라인 솔루션은 정확히 어떻게 작동합니까? 기본적으로 이 과정은 TrackMotion 자동화 시스템을 통해 서로 연결된 장비 두 대에서 수행됩니다. 여기서 여기에 속하는 TransLift(운송 리프트, 전동 그리퍼 장착 리프팅-벤딩 카트)가 공급 벨트에서 동시에 두 개의 미가공 부품을 들어 첫 번째 장비로 운반합니다. 여기서 VL 1 TWIN의 두 개의 픽업 스핀들이 이를 넘겨 받고 부품들을 작업 공간으로 보냅니다. 이후 내경 및 외경의 첫 번째 면의 선삭 가공이 이어집니다(OP 10 – OP 10). 스핀들 케이스가 독립하여 이동할 수 있기 때문에 두 부품의 직경과 길이(X/Y 방향)가 이 때 서로 별도로 수정된다는 점입니다. 이는 공구 교체 후 편차(예: 전향 절삭판 변경 후)를 보정하기 위해 특히 중요합니다. 기계실에서 운반된 후 TransLift가 다시 인계받아 뒤집어 두 개의 반가공 부품을 180도 뒤집어 다른 VL 1 TWIN으로 운반합니다. 여기서 외경의 두 번째 면이 다듬어집니다(OP 20 - OP 20). 마지막으로 완성된 부품은 TrackMotion을 통해 보관 벨트에 장착되며, 이는 통합 스태커 유닛에 최대 400개의 완성품을 수용할 수 있습니다. 전체 프로세스는 두 개의 부품에 대해 약 20초의 사이클 타임으로 진행됩니다. 여기서 평균 Chip to Chip 시간은 5초 미만에 불과합니다. 일련의 기술적 세부 사양으로 이 엄청난 속도를 실현합니다: 따라서 두 개의 픽업 스핀들은 40% ED에서 9.9kW 및 136Nm의 높은 드라이브 값을 갖습니다. 동시에 이 내마모성이 우수한 X축 리니어 모터는(직접 거리 측정 시스템과 결합에서) 연속 정밀성을 포함하여 8 m/s2의 높은 가속도를 자랑합니다. 이를 통해 자주 필요한 메인 구멍의 H6 핏을 안정적으로 생산할 수 있습니다.
베벨 기어: 한 장비에서 천공, 황삭 및 마무리 공정
베벨 기어의 생산 시 비용 부담이 늘어남에 따라 전체 공정을 고효율로 수행해야 하며, 단조 공정을 통한 생산은 여기에서 빛을 발합니다: 현대적으로 제작된 베벨 기어는 종종 단조 작업실을 이미 "완성되어” 나옵니다. 이 경우 한 번의 클램핑으로 오직 한 번의 선삭 공정만이 필요합니다. 여기서 EMAG은 VL 1 TWIN으로 두 개의 베벨 기어 공작 재료 에서 평행 연질 가공을 위한 최적의 솔루션을 제공합니다(OP 10 – OP 10). 장비에서 4개의 처리 단계를 연속으로 실행하고 사이클 타임은 약 25초밖에 되지 않습니다: TrackMotion 또는 픽업 스핀들을 통해 공급된 후, 부품의 중심 구멍이 “완전히 들어가는” 보링 공정을 통해 생성되면, 구결의 황삭이 시작됩니다. 세 번째와 네 번째 단계에서는 보링과 구결의 마무리 공정이 수행됩니다. 특수 클램핑 솔루션은 부품의 기어를 반대로 형성하고 이를 항상 안정된 위치에 유지합니다. 대규모 보링 공정을 고려하여 Mineralit®로 제작한 기계 본체는 특수한 역할을 수행합니다. 폴리머 콘크리트가 보링 공정 시 진동을 줄이고 추가적인 정밀도를 보장하기 때문입니다. 공장물 측정을 위한 옵션형 측정 시스템은 작업 공간과 픽업 스테이션 사이에 위치하며 공정 안정성을 향상시킵니다. 기본적으로 오직 하나의 TrackMotion 시스템에 두 개의 VL 1 TWIN을 연결하고 장비에서 동일한 프로세스를 수행하는 것 역시 가능합니다(OP 10 – OP 10, OP 10 – OP 10). 여기서 중요한 것은 TrackMotion 그리퍼가 분당 최대 150m/분의 속도로 움직이고 평행하게 작동하는 TWIN 장치에서 왕복 운송을 보장하는 것 입니다.
변속기 제조를 위한 완벽한 솔루션
전체적으로 TWIN 방식은 캠 피스에서 베어링 링을 거쳐 플랜지에 이르는 일련의 다양한 부품에서 비약적인 생산성 증가를 가능하게 합니다. 요구 사항에 따라 다양한 기술의 생산 라인이 등장했으며, 예를 들어 EMAG 호빙 및 디버링 머신 역시 이에 속합니다. “우리는 VL 1 TWIN이 늘어나는 생산량과 변속기 제조에서 치열해지는 경쟁에 대한 완벽한 솔루션임을 확신합니다”고 비욘 스바텍은 말합니다. “사용자는 단가의 감소, 짧은 사이클 타임 및 높은 공정 안정성의 이점을 누릴 수 있습니다. 우리는 이러한 이점을 시장에 더 많이 도입할 것입니다.”
담당자
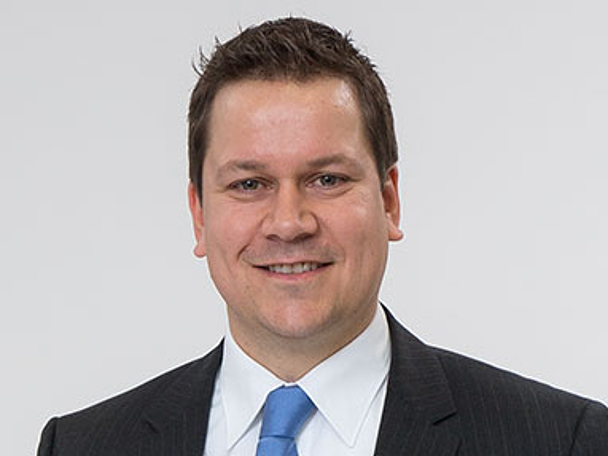