08/01/2023 - Oliver Hagenlocher - Press
ELC 6 from EMAG LaserTec: Perfecting the welding process for rotor shafts
Sales of electric cars are on the rise - and at an enormous pace worldwide. The International Energy Agency (IEA), for example, estimates that 14 million e-vehicles will be sold this year, representing a 35 percent increase in sales compared with the previous year. This means that they already account for almost one-fifth of the total car market. As a result, production planners are focusing on the manufacture of key components of the e-motor, such as the rotor shaft. They are looking for innovative solutions "from a single source," with which the component can be machined particularly efficiently and reliably in ever larger quantities. EMAG LaserTec is currently setting an example in the market with its ELC 6 laser welding machine. In the machine, joining, preheating and welding processes are compactly combined on an assembled rotor shaft with its rotary table system ensuring optimum cycle times. Visitors to the EMO trade show in Hanover, Germany, from September 18-23, can find out exactly what this manufacturing system looks like and what possibilities it offers at the EMAG Group's booth in Hall 17, C 34.
Images
Advances in e-mobility, including hollow designs of components, allow great freedom in design, lighten the weight and lower material costs for assembled rotor shafts. At the same time, this "heart" of the electric motor has to withstand particularly high loads, as motor speeds of up to 20,000 rpm are now possible. Compared to a camshaft in a combustion engine, for example, this value is many times higher! Thus, the production of assembled rotor shafts is always about manufacturing tolerance - even minimal imbalances must be avoided at all costs, because they would endanger the service life of the engine. In addition, the process must result in a highly stable component.
In this context, what is the most efficient way to reliably produce increasing quantities in the face of an expanding market? One answer to this question leads directly to the innovative technology of EMAG LaserTec, because the company, based in Heubach near Aalen, has an impressive track record with laser welding, which is indispensable in "building" the two-piece rotor shaft. All the leading automotive manufacturers have the associated systems with the abbreviation "ELC" (EMAG Laser Cell) in use in various application areas. The key to success is a high level of competence as a system supplier: EMAG LaserTec knows the entire production sequence of the respective components and develops the complete process chain on this basis. On the customer side, the planning of new or the expansion of existing production facilities is therefore massively simplified. In addition, the whole process is based on EMAG's modular mechanical engineering, which includes a large number of proven components. Therefore, these plants and their processes are exceptionally stable and efficient in every detail.
All processes in rapid change
It is precisely this quality that the southern German laser specialists have been bringing to the production of assembled rotor shafts for some time now. The ELC 6 machine is at the center of this - a highly efficient solution for joining the two halves of the component, with part handling, preheating and joining as well as welding taking place in quick succession and perfectly timed by the rotary table. The precisely metered, concentrated energy of the laser beam permits high welding speeds with minimal distortion on the welded component. A look at the details reveals the performance of the machine, which was specially developed for powertrain components with circumferential welds:
- Before the individual parts are loaded into the ELC 6, the workpieces are laser cleaned. For this purpose, EMAG LaserTec offers the LC 4 laser cleaning machine, which can be optimally link-up with the ELC 6, thus ensuring seamless line integration.
- In the next step in ELC 6 (preheating and joining), the induction technology first ensures an ideal processing temperature on the component before the two components are joined.
- Before welding, the weld seam position is checked and the component position is readjusted. The contour is scanned with precision and the data is communicated to the welding optics and the NC axes.
- During the subsequent welding process, the vertically arranged workpiece rotates, while the laser optics only move radially towards the workpiece. The welding process with its focused energy thus takes place virtually from the side at the circumferential weld. A pyrometer controls the process temperature.
- After welding, the component is transported out of the machine by a swiveling motion of the rotary table and unloaded by a robot.
Overall, this solution has an enormous production speed - partly because the machine with its rotary table is loaded and unloaded during welding (and thus cycle time-concurrent). In addition, the individual subprocesses are perfectly synchronized. The "fixed optics/moving workpiece" principle ensures a high level of operational reliability. In addition, EMAG LaserTec designs this solution very flexibly for customers in terms of technology, output and automation, whereby workpieces up to a maximum height of 300 millimeters can be machined in the ELC 6.
The whole solution from a single source
In principle, EMAG scores with a comprehensive technology portfolio in this field of application, because the machine builders have already developed various solutions, for example, for the subsequent joining of the rotor shaft and rotor-sheet package as well as the high-precision overturning of this package. The same applies to the turning, gear cutting and grinding of the two individual rotor shaft parts before welding. When it comes to the automation technology that ensures transport between the machines, EMAG adapts to the customer's ideas. For example, line gantries, stacking cells, accumulating conveyors or EMAG's own TrackMotion system are used - in any case, the overall system benefits from the uniformity of the machines used with their optimized interfaces. The end result is complete solutions for the customer. EMAG is the only contact required during planning, implementation and servicing. Technological competence and experience guarantee a perfect process chain with extreme speed and high safety.
Contact
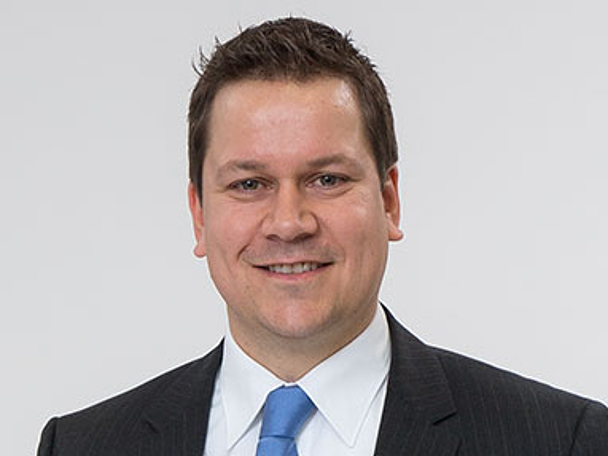
Oliver Hagenlocher
Area
Press and Communication