02/24/2020 - Oliver Hagenlocher - Press
EMAG Receives “Outstanding Supplier” Award from Sisamex
The EMAG Group and Sisamex, a member of the Mexican Quimmco Group, have been production partners for over 20-years. At its plants in Monterrey, Sisamex produces a large variety of workpieces for trucks, agricultural and utility vehicles for many renowned manufacturers. Since 1997, Sisamex and EMAG have worked together to install a variety of EMAG machines and technologies including soft and hard turning, grinding, hardening and laser welding systems. This decades-long collaboration and the installation of their newest manufacturing line for the laser welding of truck differential cases clinched the decision by Sisamex to honor EMAG with its Supplier Award.
Images
High-Productivity Solution for Truck Differentials
How can the production of a truck differential be optimized? This question was the starting point for the development of the award-winning manufacturing solution. “Lightweight design for the truck industry”—this phrase sounds rather unusual. Typically, this is associated with the production of cars, where almost every component must become smaller and lighter to reduce the combustion engine’s consumption or to enable electric cars to travel greater distances in one charge. In the past, when “lightweight design” was discussed for utility vehicles, it meant a lighter superstructure and cabins. Drive train components were not event considered because they were exposed to extreme permanent loads, meaning that their stability was always critical. Now that EMAG LaserTec has developed a solution that will not only reduce the weight of truck differentials, but also simultaneously increase the parts stability, the process for producing parts for utility vehicles has changed dramatically.
EMAG LaserTec: Experts in Laser Welding of Transmission Parts
Laser welding has become essential for the production of a variety of engine and transmission parts. Welded joints have now replaced the old screwed connections in many places. With the introduction of laser welding technology, parts can now be made lighter and more cost-effective because screwed connections were very expensive. With Sisamex, the challenge was to transfer this principle to truck differentials – and EMAG LaserTec passed with flying colors. Using laser welding technology, production experts were able to eliminate 40 screw connections, allowing the drive train to lose several pounds and dramatically reduce manufacturing costs – a win-win situation. Dr. Andreas Mootz, Managing Director of EMAG LaserTec, explains: “Having a high level of expertise as a system provider was an absolutely crucial factor for our contact at Sisamex. We develop complete process chains revolving around laser welding, which in principle vastly simplifies planning on the customer end and simultaneously guarantees safe and effective processes.”
A Perfectly Timed System for Truck Differentials
Even though EMAG LaserTec had a lot of experience in machining differentials in trucks, this knowledge cannot be directly applied for the production of differentials in utility vehicles. The dimensions and weights of the workpieces are different, and require the system to be re-worked when it comes to handling. Before production starts, truck differentials consist of three separate workpieces: two case parts as well as the ring gear. These parts weigh up to 130 kilos (287 lbs) and have a diameter of up to 600 millimeters (24 in). Furthermore, the experts at EMAG LaserTec had to overcome a few process-related challenges—after all, the weld seams are cast steel/case-hardened steel connections with great hardening depth, which are welded with an 8 kW (11 hp) solid-state laser and with welding additives. The dimensions of the manufacturing system itself are also impressive: The whole system consists of two laser-cleaning stations, a heating station, a joining station, the ELC 600, and the ultrasonic testing station, linked by a complex feeding technology and two industrial robots. “With our complete system, we have easily overcome all of the presented challenges and mastered the requirements – as is proven with us receiving this award from Sisamex,” said Dr. Mootz.
“I’m really pleased to have received this award,” adds Markus Hessbrüggen, CEO of EMAG Group, who accepted the award on behalf of the Group. “To me, the award is above all a distinction for the capacity to innovate that is inherent in all members of the EMAG Group. At the same time, the award also stands for the many years of trustful and amicable cooperation that connects us at a very personal level with the people at Sisamex. That is why I would like to express my deep gratitude on behalf of all EMAG employees.”
Contact
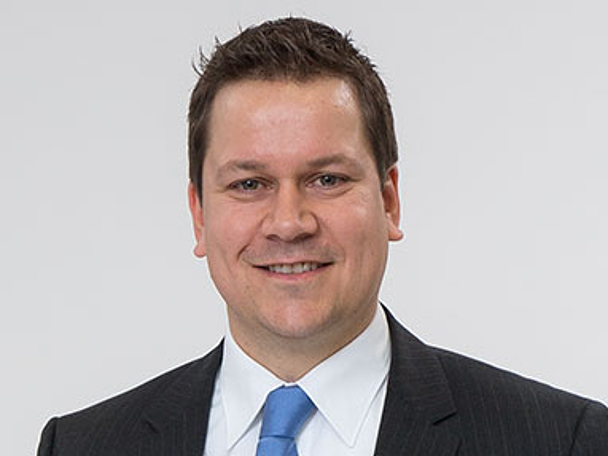
Oliver Hagenlocher
Area
Press and Communication