08/08/2025 - Oliver Hagenlocher - Press
MSC 5 DUO: Front-loading CNC turning center for economical soft turning
In today's world, manufacturing companies are facing major challenges: increasing cost pressure, a shortage of skilled workers and rising energy costs. This combination requires machine tools that generate more output with less manpower and are energy-efficient at the same time. The MSC 5 DUO from EMAG was developed in response to these requirements and will be officially presented for the first time at EMO 2025 in Hanover.
Images
Machine concept with a focus on productivity and cost-effectiveness
The MSC 5 DUO is a two-spindle front-loaded CNC turning center designed for automated batch production. As components of the EMAG Classic series, it is characterized by an optimal ratio of functionality and capital investments. The machine focuses on high-productivity soft turning and combines proven EMAG technologies with cost-optimized basic equipment.
Peter Gröner, Product Manager of the Turning Business Unit at EMAG, explains this approach: "The Classic series stands for optimized basic machines at attractive capital investments. While our modular and customer-specific machines offer a wider range of options and customization possibilities, with the Classic machines we concentrate on what is absolutely necessary."
The economic benefits for users are obvious: The MSC 5 DUO costs significantly less per spindle than comparable models from higher product lines, but offers the same productivity for standard soft turning applications.
Split-bed design as the basis for precision
The split-bed design forms the foundation for precision machining results. This design of the machine base mechanically decouples the two work areas from each other and thus prevents the transmission of vibrations during simultaneous machining. This ensures constant dimensional accuracy on both spindles, even during demanding machining processes.
Powerful main spindles for a wide range of applications
The main spindles of the MSC 5 DUO have been designed for a wide range of applications. With a maximum motor speeds of 4,500 rpm and a standard spindle power of 5.5 kW in continuous operation or 7.5 kW for up to 30 minutes, there is sufficient reserve power available for demanding machining tasks. A more powerful version with 7.5 kW in continuous operation and 11 kW for 30 minutes is available as an option.
The constant torque in the speed range from 1,125 to 4,500 rpm is particularly important for consistent machining results. It ensures constant cutting performance for different materials and machining requirements. The A2-5 spindle nose can accommodate various chucks up to 210 mm in diameter.
The thermally optimized spindle bearing with precision bearings ensures maximum concentricity, while an intelligent cooling concept with active temperature monitoring guarantees constant machining conditions even in continuous operation.
Highly dynamic turret with BMT interface
The servo-controlled turrets form the heart of the MSC 5 DUO. Eight tool positions are available as standard, with an optional extension to twelve positions. Compared to conventional VDI- holders, the BMT tool interface offers significantly higher rigidity, which has a positive effect on machining quality and tool life.
This interface enables the mounting of boring bars up to 40 mm in diameter for internal machining as well as tools with a 25 x 25 mm shank for external machining. The servo-controlled indexing in combination with hydraulic clamping ensures short tool change times and high positioning accuracy.
Efficient gantry loading system for minimal non-productive time
A decisive productivity factor in batch production is the reduction of non-productive times. The 3-axis gantry loading system of the MSC 5 DUO, which is fully integrated into the machine control system, automatically loads and unloads the workpieces. Parts handling is fast and precise thanks to the use of servo motors in all axes. The workpiece turner integrated as standard enables the complete machining of workpieces from both sides within one machine, which considerably simplifies the material flow and significantly reduces lead times in production.
Compact stack storage system for autonomous production
Another important aspect is the compact stacking storage system (stacker system), which is integrated directly into the machine. This system for raw and finished parts requires no additional space and can be flexibly adapted to different workpiece geometries. Depending on the size of the workpiece, sufficient components can be stored for several hours of autonomous production, which is particularly important in low-manned production. The compact design also saves valuable production space - a cost factor that should not be underestimated in modern manufacturing operations.
Process optimization through intelligent control
The MSC 5 DUO is equipped with a FANUC 0i-TF Plus controller, which is specially designed for turning applications.
A central advantage for the user is the possibility of parallel programming during machining. The operator can prepare the next program while the machine is still producing. The control system also offers extensive process monitoring options.
The MSC 5 DUO is designed for integration into digital manufacturing environments. It can be easily connected to MES and ERP systems via standardized interfaces and supports the collection of production and machine data for process optimization.
The MSC 5 DUO is the answer to current market requirements in machining production. It combines twin-spindle machining with an integrated automation system, thereby achieving high productivity at attractive capital investments. The concept of the MSC 5 DUO with its integrated automation system is ideal for use in automated production lines in which several machines are linked to form a process chain.
As Peter Gröner emphasizes: "It is important to us that we do not create complexity for the sake of complexity. The MSC 5 DUO offers precisely the technical functions that our customers need for their specific production tasks - no more and no less. We consider this focus on the essentials to be a decisive factor."
Contact
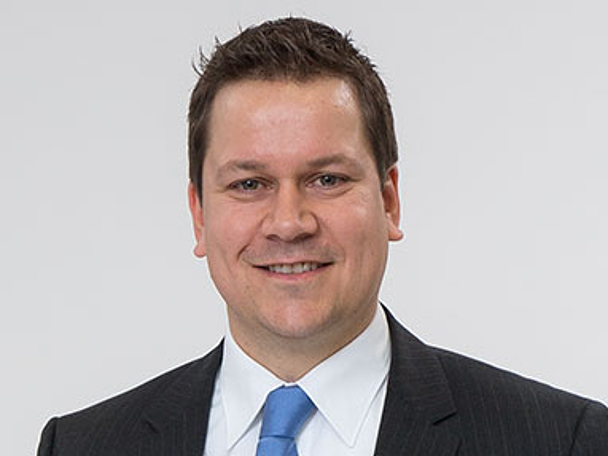
Oliver Hagenlocher
Area
Press and Communication