Mack Rides roller coasters can be found all over the world. The company based in Waldkirch near Freiburg is a global player in the amusement industry and produces complete solutions in-house, including rails, vehicles, decorations, animations and much more. On board for the rail production: induction technology from EMAG eldec. It ensures precise heat treatment prior to final alignment of the components. A conversation with Marcel Martinetz, head of equipment design, about the special know-how of his company and the associated production solutions.
Tag:
induction heating
EMAG eldec is breaking new ground in the production of inductors for induction heating and relies on the latest manufacturing methods, such as additive manufacturing.
We discussed the advantages this provides and the new opportunities this opens up with Kadir Yilmazli, who is responsible for ongoing development in this area as a development engineer for additive manufacturing at EMAG eldec.
Fans are used in a number of production processes—they play a key role, for example, in extracting gases, cooling down materials or transporting solids at the heart of ventilation systems. Elektror airsystems, headquartered in Ostfildern, Germany, and with two production sites in Waghäusel (Germany) and Chorzów (Poland), is one of the international leaders in the manufacturing of industrial fans and side channel compressors. About 60,000 devices are produced here every year. For the production of its electric motors, used in a variety of fans, the Waghäusel site has been relying on UNI HEAT from EMAG eldec since May 2018: The system ensures precise induction heating of the empty stator housing before the joining process. An interview with Roland Sand, Head of the Production team at Elektror airsystems, about choosing the right supplier, the collaboration with EMAG eldec and the meaning of process reliability follows below:
Welding processes in the automotive industry pose a special challenge for production planners. The process must be performed within seconds and without any negative impact on the material – anything but a trivial requirement when one considers the high process temperatures. Pre-heating before welding, therefore, takes a key role. The component is heated precisely to the required process temperature of around 160 to 180 degrees Celsius. This prevents unwanted heating of the material structure in the heat-affected zone, the area directly surrounding the weld. Pre-heating effectively prevents the formation of cracks in the component after welding.
Induction heating is ideally suited for setting up automated production processes. The technology is easy to integrate into the overall process flow and enables the machining of very large part quantities quickly, precisely and safely. Hardening, joining, brazing and pre-heating are examples of applications that benefit from this flexible technology.
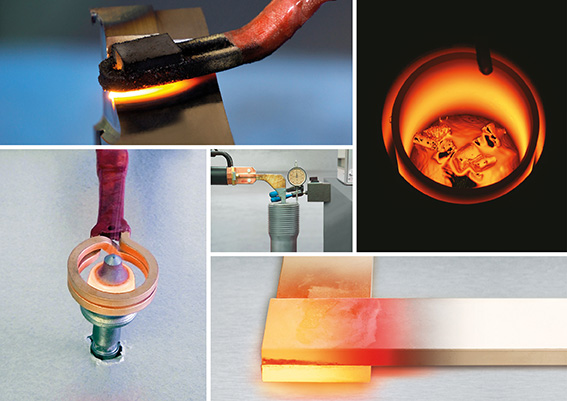
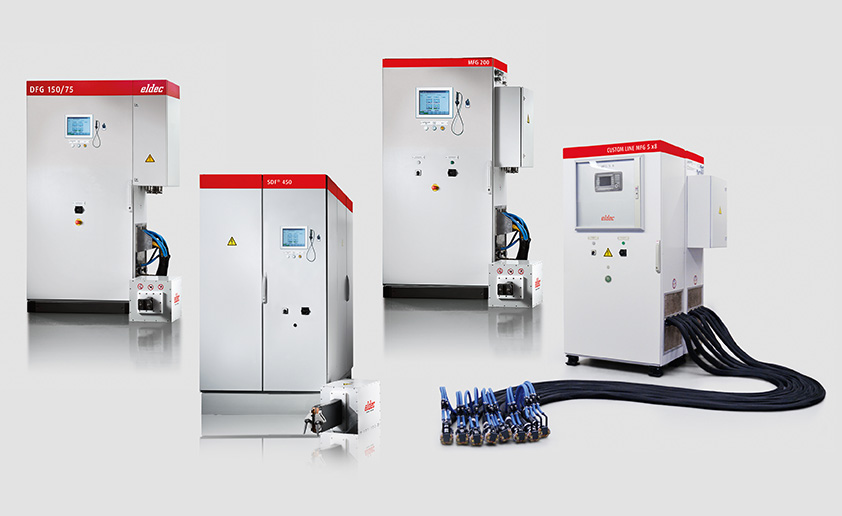
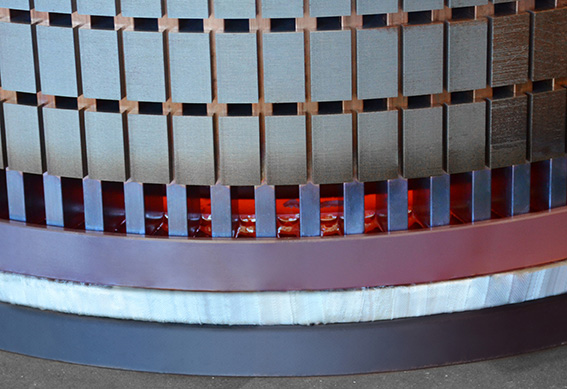
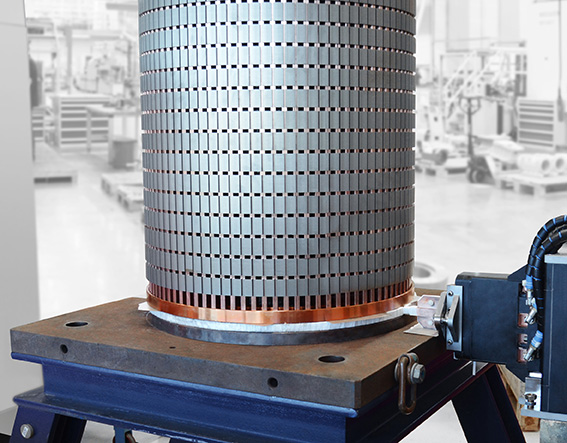
eldec CUSTOM LINE generators: customized energy source for perfect induction heating
by Markus Isgro
“Customized” is the key word when it comes to delivering a perfect production solution for building systems and machinery. Each technology is individually tailored to the customer’s environment, guaranteeing a highly efficient and optimally configured process. Induction heating in particular is one of the technologies that requires customization because the quality of the customer’s process depends on a whole range of very specific details. As the energy source, the generator plays an important role here. The experts at EMAG subsidiary eldec, based in Dornstetten, Germany, know this very well.
Experts are predicting an increased production of cars with electric motors. Though most of these cars will be hybrids, the increase in production will still pose a challenge to production planners. The question is how to process these larger quantities?
Inductor building is a key growth sector for eldec for a combination of reasons. First, more and more companies — in industries such as automobile production or aerospace — are discovering the vast potential of induction heating. Increasingly complex parts are being heated, hardened, or annealed. Second, these developments call for specialized expertise in inductor building.
For more than 30 years, eldec has developed and built inductors that perfectly match the geometry of the workpiece.
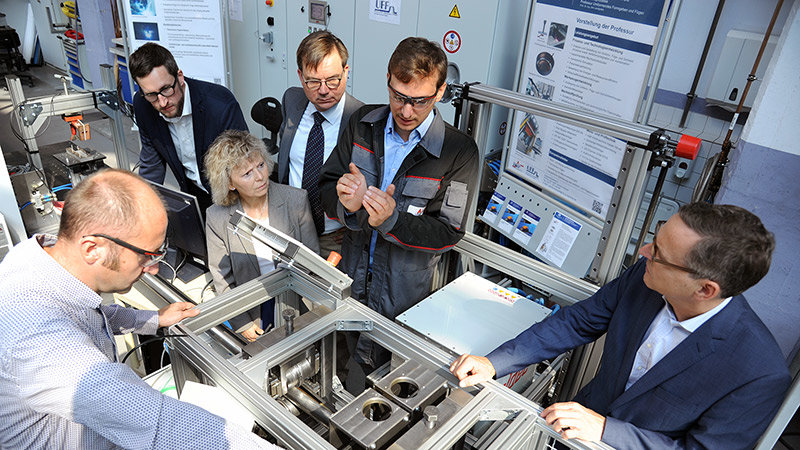
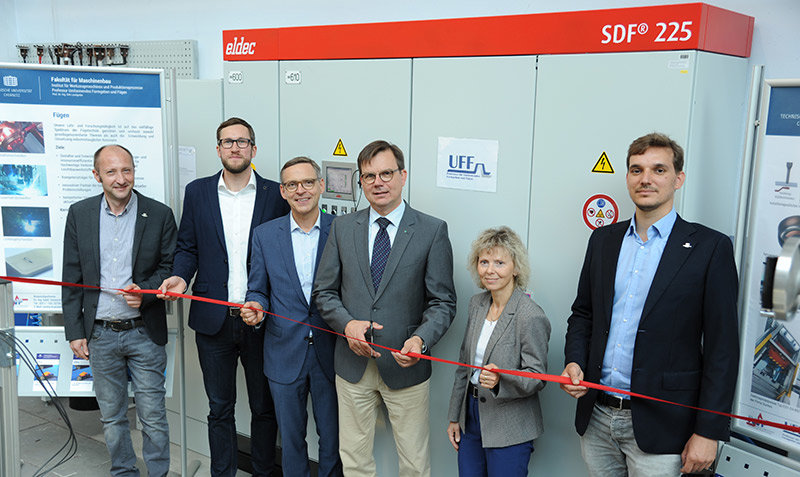
Effective and resource-saving: Targeted heating and joining of modern material combinations
by Markus Isgro
The academic department of Forming and Joining at TU Chemnitz is expanding its systems technologies for research into complex welding, heat treatment, and forming tasks
Since 29 June 2018, the academic department of Forming and Joining at TU Chemnitz has been using a new induction generator that enables the heating of semi-finished goods consisting of several layers of different materials by applying different frequencies in a targeted manner. This may be useful in particular for the production of plated pipes in the chemical industry or in power plants. 62,000 tons of pipes are produced for these sectors per year in Germany alone.