Without the tripod joint, the drive in a car would be inconceivable: The relatively small component creates the power connection between the axle drive and the drive shaft. Why is this technology so important?
1. What characterizes the tripod joint?
How do you transmit forces between the axle drive and drive shaft – and with as little delay as possible? The automotive industry usually answers this question with the tripod joint (or constant velocity joint), because the relatively small component ensures a very uniform rotational movement and at the same time compensates for the spring movement of the vehicle. In addition, length compensation can even be achieved with sliding variants. This is made possible by an ingenious design, which is characterized by three recesses in the outer pot. It is located at the end of one of the shafts. On the other shaft, however, there are three pins with needle-bearing mounted shafts that move in the recesses. Overall, a maximum deflection angle of up to 30 degrees and a length compensation of 30 to 50 millimetres is achieved on this basis.
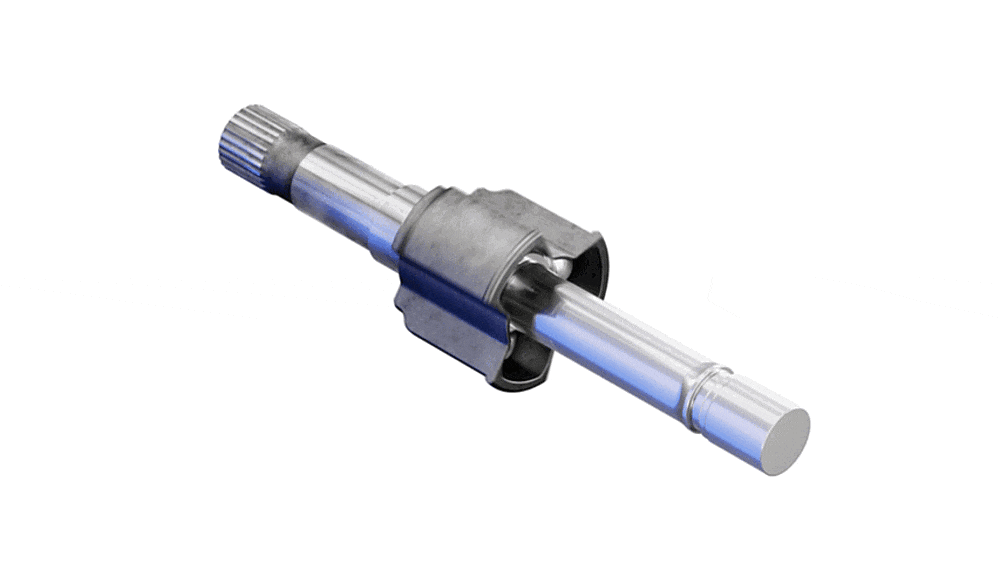
How the tripod joint works
2. Who invented it?
The first tripod joint was patented by the French company Glaenzer Spicer back in the 1960s and quickly established itself as a standard solution on the market. There are also various predecessors for comparable tasks – i.e. the transmission of force from one shaft to another. There are certain similarities, for example, with the Rzeppa CV joints, which were invented by Alfred Rzeppa in 1926 and rely on free-running balls in a cage.
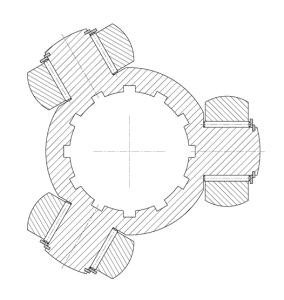
Cross-section of the three pivots including rollers – effectively one half of the tripod joint.
Source: By Martin Jediny – Own work, CC BY-SA 4.0, https://commons.wikimedia.org/w/index.php?curid=107706983
3. Are there any disadvantages?
The tripod joint has a central function in the car’s drivetrain. As a result, enormous forces act inside it – including constant load changes, which is often noticeable after a while. The rollers virtually work their way into the housing, resulting in greater play, which in turn causes annoying noises on bumpy surfaces or when cornering. In addition, the entire joint must be protected from dirt by a plastic sleeve and lubricated with a special grease.
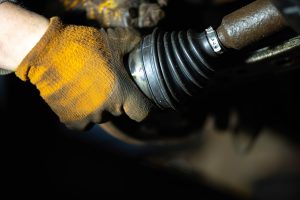
In view of the high loads, repairs to the tripod joint are always possible.
4. What does the future hold?
The aforementioned axial displaceability of the tripod joint in particular is a recurring focus for developers – with even greater displacement ranges being sought in some cases. In this way, the entire component has a kind of overload protection in extreme driving situations and increases the crash safety of the vehicle. Overall, however, the component remains important across all drive types: even in electric cars, the forces between the axle drive and drive shaft must be transmitted evenly.
5. What does all this mean for production?
It’s almost obvious. In view of the high machining demands, the central surfaces of the tripod joint are hardened and finalized with high precision – a task for EMAG. We develop manufacturing solutions that are specifically tailored to the requirements of tripod joints. The focus is not only on the machine itself. The entire process – machining technology, NC programming, tools, automation and energy consumption – is specifically optimized.