What does retrofit do? The short answer – many things are possible. Depending on the customer’s wishes, the retrofitted machine not only has new components, but it is also equipped with new automation or additional tool technology. A turning machine, for example, becomes a turning-grinding center. Here we present just two examples among many possible scenarios.
Category:
Videos
1. Name
In a traditional automatic transmission, a torque converter is installed between the engine and transmission. This core component contains an impeller, turbine wheel and a guide wheel. Driven by the engine, the impeller blade catch oil in the housing which creates a flow that will delayed drive the turbine wheel. This principle ensures a smooth startup and separates the drive train from the engine’s vibrations (referred to as engine irregularities).
1. Why do cars even have differentials?
There are no cars that don’t have differentials in them—otherwise we would be driving through tight curves with the wheels spinning and tires screeching. This essential component is located in the center of the drive axle, where its function is to make sure that the two wheels can turn at different speeds when driving around curves, while nonetheless having exactly the same propulsive power. The torque of the motor is always divided in a fixed ratio.
By the way: All-wheel drive vehicles have a differential on each axle, plus a central differential that distributes the engine power between the axles in a given ratio.
The scroll-free turning of rotor shaft sheet metal housings has a number of advantages over the traditional turning process. For one, scroll-free turning provides significantly higher feed rates per revolution, leading to a reduction in overall cycle time. Machine time is also reduced by using the entire cutting edge of the tool – providing the additional benefit of improving tool life. This technology has also proven to achieve significantly better surface qualities.
https://youtu.be/hQh4gKpu_w0
The VL 1 TWIN has set the new standard for the high-output, simultaneous machining of workpieces with a maximum dimaeter of 75 mm (3 in). This turning center has two main spindles in one machining area that are able to simultaneously machine two identical workpieces – resulting in substantially increased output quantities, and lower unit costs.
High-strength materials, complex geometries, large unit volumes—the production of turbocharger shafts is one of the most challenging tasks in automotive manufacturing. With its new turn-key production system, EMAG has developed a holistic and complete solution. How exactly does it work?
https://youtu.be/QXkB5BWRywA
Large components and complex geometries—in heavy machining, this combination is far from being rare and always synonymous with a high expenditure of time and rising costs. The reason is that the various machining processes from turning to gear cutting are frequently performed in different machines that are not entirely interlinked with one another.
With its vertical turning/milling center VMC 450-5 MT, EMAG Leipzig breaks the vicious circle in an impressive manner: All turning, milling, drilling and gear cutting processes take place in a single machining area. To achieve this, the machine is equipped with five axes. This results in shorter throughput times and a minimal tooling effort—with increasing component quality and diversity.
How can commonly mass-produced transmission components, such as planetary gears be produced even more efficiently? The EMAG Group provides a customized answer to this question with the development of the twin-spindle pick-up turning center, VL 1 TWIN. It machines two identical components simultaneously in the same machining area. This technology opens up a wide range of possibilities: When two machines are combined in a line, the planetary gear can be machined from two sides—and all that is completed with shorter cycle times. What exactly does the line solution for planetary gears look like?
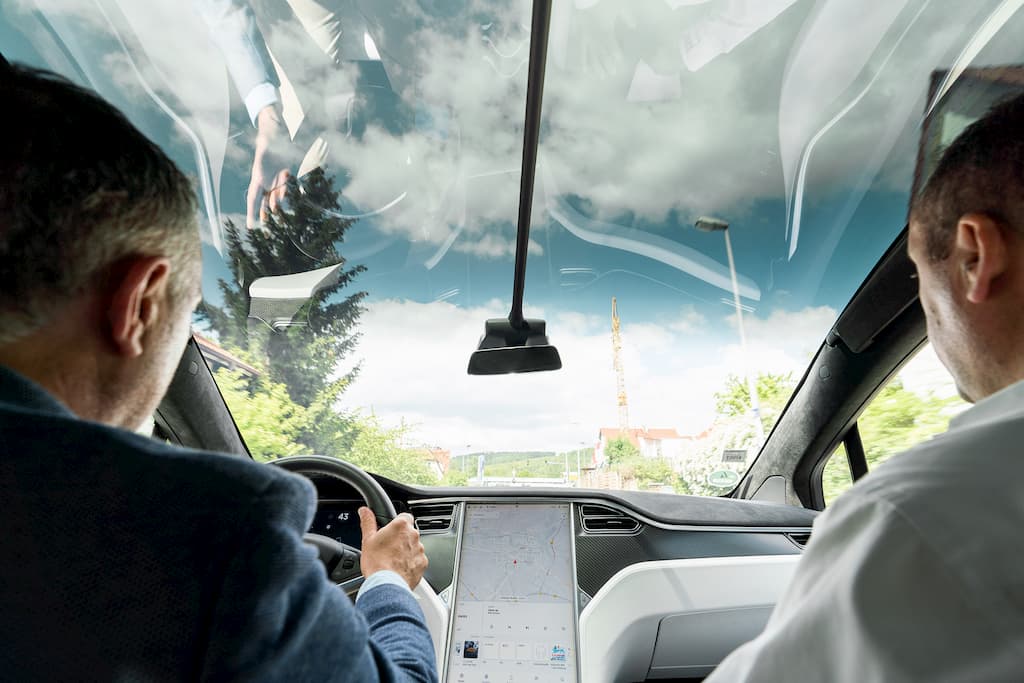
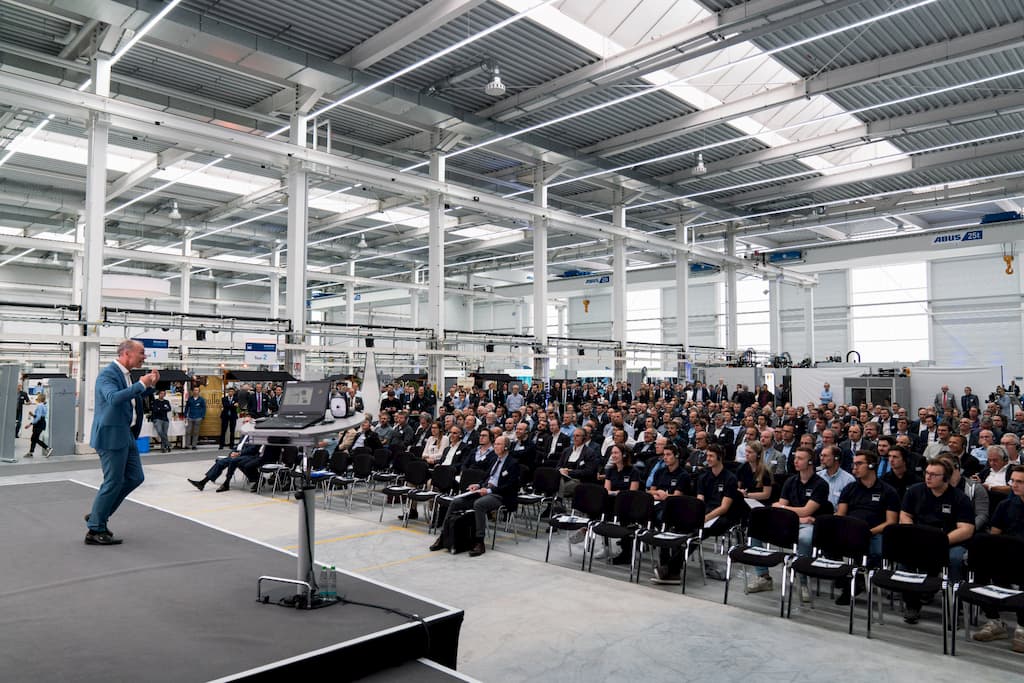
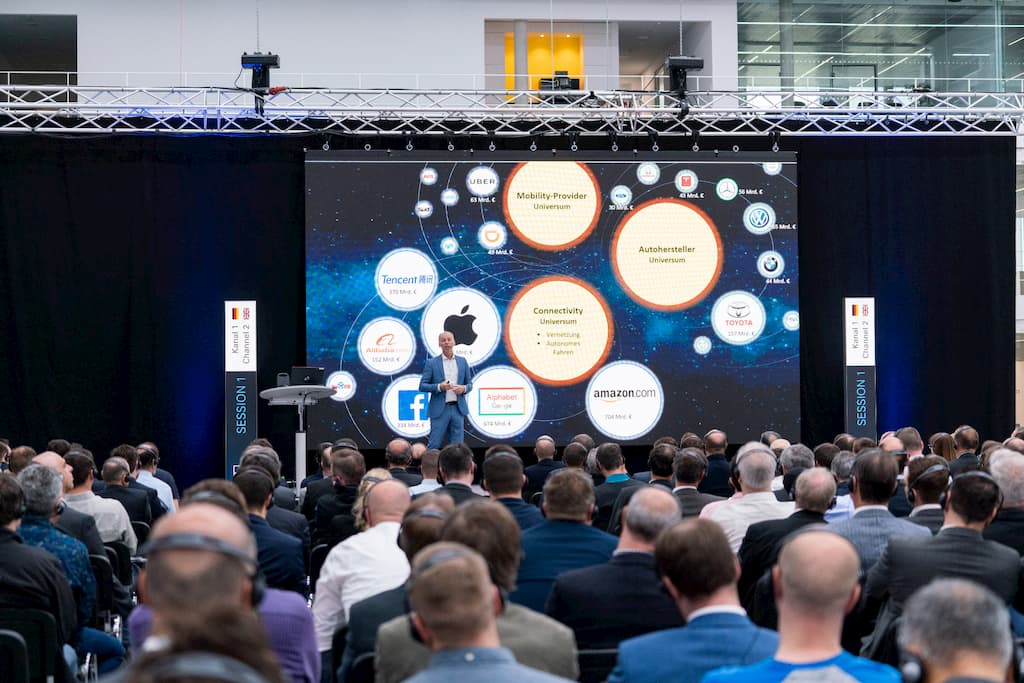
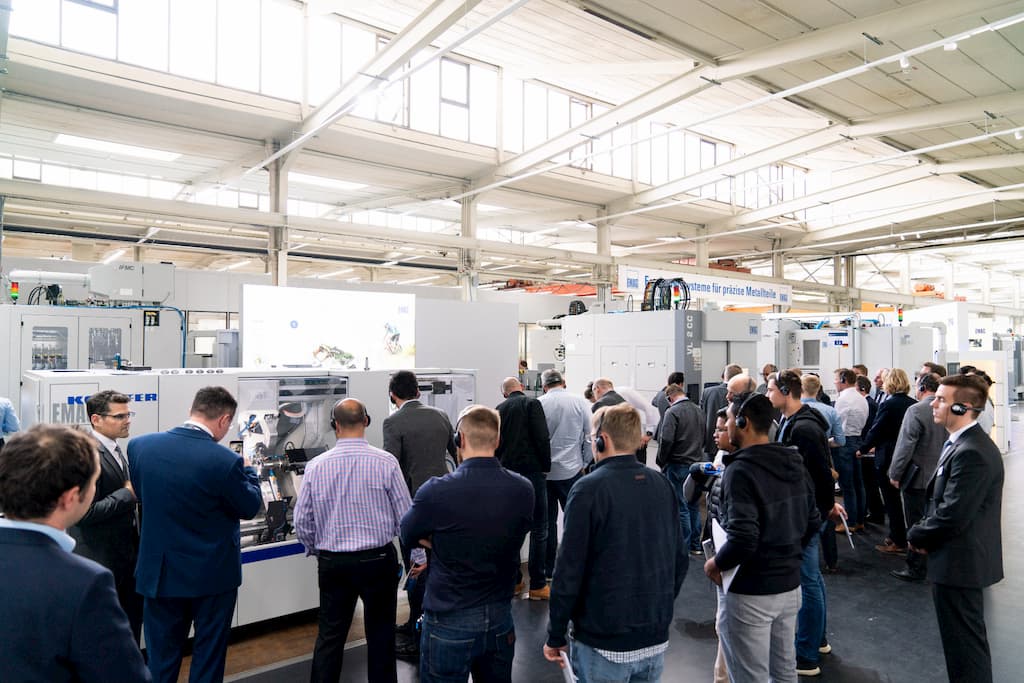
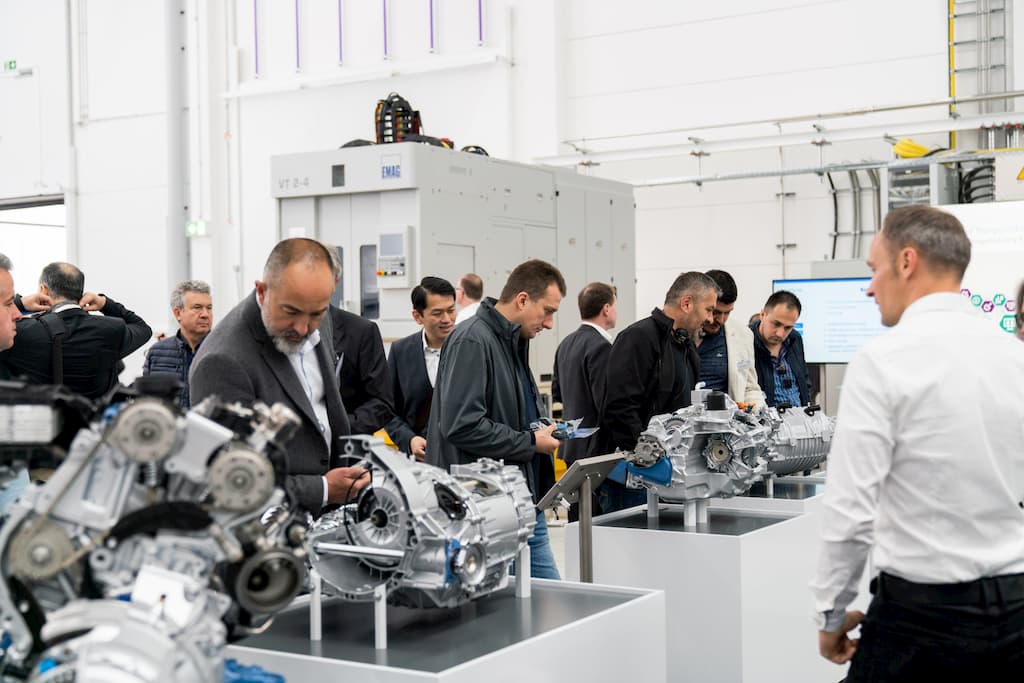
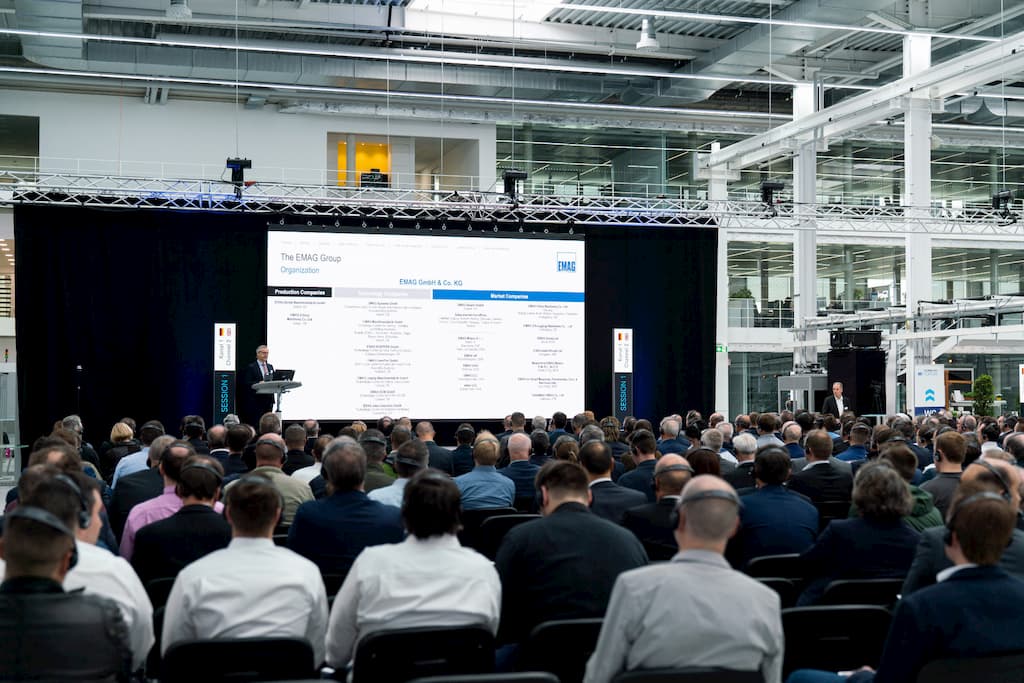
The transformation in the automotive industry is coming fast, and those affected should prepare now— this was the primary message at the 2019 EMAG Technology Forum. The event provided a lot of food for thought for attendees. Which key messages stood out?
- 1
- 2