MR Components, a medium-sized company from Grigno, Italy, has significantly increased its production capacity and simultaneously improved quality by introducing intelligent automation with EMAG machines. The company, which specializes in the production of parts for differential and planetary gears, now produces around 80,000 components per month, with some of the machines running unmanned in the evenings. In conversation with Alessandro Reguzzo, owner and Managing Director of MR Components, we were able to find out more about the company’s production philosophy and design and development.
Hello Mr. Reguzzo, tell us a little about yourself and your company MR Components.
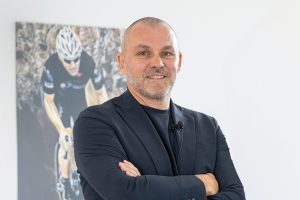
Alessandro Reguzzo, founder and Managing Director of MR Components
I am Alessandro Reguzzo, 51 years old and I took the step from employee to entrepreneur at the age of 21. It all started in 1995 when I got my first CNC lathe. At first, I worked for a few companies in the region and gradually my business grew.
Where did you start working?
I started as an apprentice in a nearby company and discovered my passion for precision manufacturing there.
At the age of 21, you decided to buy a CNC lathe and start up in a garage?
Yes, many people thought I was crazy, but I was convinced I was doing the right thing. At the age of 21, I went to the bank, took out a loan and started working in a garage with a CNC lathe. The companies I worked for quickly put their trust in me, perhaps because they saw my passion. Within three years, I already had three CNC lathes.
Who supported you when you set up the company and who were your first customers?
My first customers were various craftsmen from the region, including some racing car builders. At first, I made spare parts for local companies, but after a while I also found larger customers in the north of Veneto.
How has your company developed over the years?
I worked in a garage the size of this office for five years. Then I moved into a small hall and built my first production hall of 2,500 m² in 2006. In January 2024, we moved into our new 6,000 m² building. It is modern and state of the art.
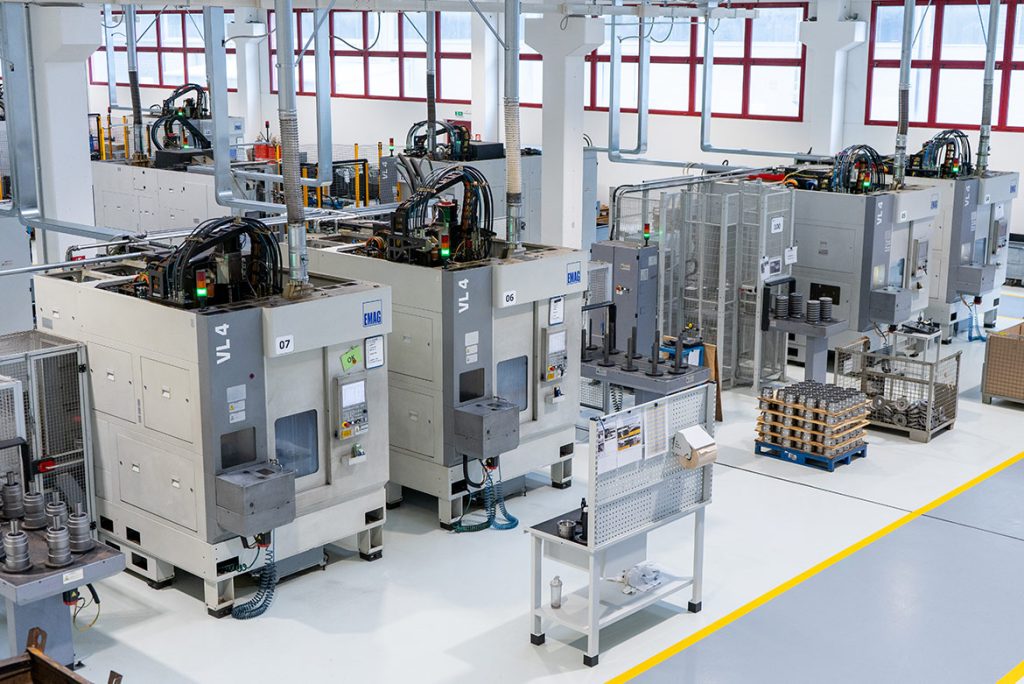
Two VL 4 manufacturing systems at MR Components, each linked-up with a TrackMotion and stacker cell, in a modern and highly automated production hall. MR Components continuously invests in the latest technologies for the best quality.
How many employees do you have today and what is the composition of your team?
We have around 50 employees, ten of whom work in the office in the quality department and in technology. The others work in production. We produce around 80,000 components per month.
What exactly do you produce?
Our two main business areas are the manufacture of components for differential gears and planetary gears. The differential gear parts are supplied complete and ready for installation to our customers. The other product line, which is mainly manufactured on EMAG machines, is planetary gear parts. These are supplied to various Italian customers and above all abroad, with German customers being important customers.
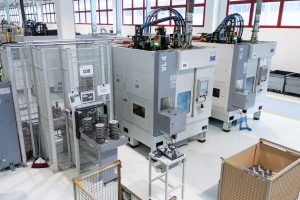
One of the production lines at MR Components with VL 4 machines equipped with TrackMotion automation. This enables unmanned operation in the evening hours.
Can you briefly explain your production philosophy?
In the beginning, we worked with conventional machines, especially horizontal lathes. Automated production then began with simple Taiwanese vertical lathes, which were within our financial means at the time. After a short time, we realized that the use of automated machines was the key to speeding up production. The main advantage of these machines is that they run automatically and can, therefore, work unmanned. This distinguishes them fundamentally from conventional lathes.
In 2011, we purchased our first two VL 7s from EMAG, which was a game changer for us. Above all, we learned to appreciate the advantages of the integrated measuring probe and the associated in-process control of all components. The stable design and high quality of the machine components are also essential in batch production in order to stand out from the competition.
Today, all our EMAG machines are equipped with measuring probes so that we can check all components 100 percent. In addition to in-process control, we carry out further quality controls with various measuring devices. We also have a measuring room equipped with two Zeiss and other measuring machines, so that we can always supply our customers with an optimum product. As you can see, quality is our top priority! We currently have a reject rate of just 0.2 percent for 80,000 components, which shows that we are well positioned.
It is noticeable that mainly partially or fully automated machines are used, why?
In my company, we use different types of manufacturing systems to meet the respective production requirements.
In one of our lines, we work with VL 7 machines, where the operator manually places the workpieces on the automation belt. This process has proven to be particularly effective for very simple workpieces or more complex workpieces with small quantities.
In other production lines, we work with VL 4 machines that are equipped with TrackMotion automation. The automation here is very fast and we have greater autonomy, so we can also run the machines in unmanned operation. We work in two shifts and let the machines continue to run autonomously for 2 to 4 hours in the evening, depending on the storage capacity of the raw and finished parts.
We have other manufacturing systems, also with VL 4 and VL 6 machines, which are automated using robots. The decision was made to use a system with robots here, as many components have to undergo other operations in addition to turning, such as marking, which we can carry out very easily and flexibly with the robot.
Overall, these different manufacturing systems enable us to react flexibly to the respective production requirements and ensure high quality and efficiency.
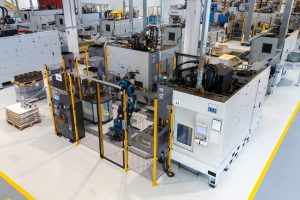
A robot at work on a production system from MR Components. Thanks to automation, additional operations such as marking can be carried out flexibly and easily.
Does this system allow you to utilize production time even during company closing times, so that the machines continue to run for 2 to 4 hours, depending on the workpiece, while you and your employees are already going home?
Yes, exactly. I have the certainty that if I check all components 100 percent, the machine will automatically stop production if a part is faulty. That way I avoid rejects and make optimum use of production time. That’s a big advantage, because nowadays it’s really difficult to find staff for the night shift. In this way, we have found a way to do without the critical night shift and still benefit from the extra production hours – that’s why we call this time “free” hours.
We are able to produce batches of 100 to 30,000 components per month. Our batches vary greatly as we have equipped our company to serve different customers with different requirements. We are flexible enough to handle both small and large orders efficiently and on time.
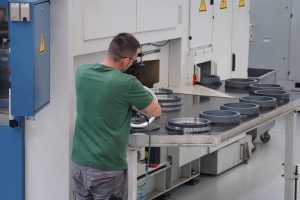
Thanks to intelligent automation, the machines at MR Components continue to run even during closing times, making productive use of the night hours.
What does your team look like and what role does it play in your company?
I consider myself very lucky to have such a strong team at my side. Our long-standing employees in particular, some of whom have been with the company for 20 years, have always believed in me and my vision. They have made a significant contribution to the success of the company, for which I am very grateful. We worked together on the idea of highly automated production. Even though it seemed complex at first, the advantages became obvious over time and we are benefiting from it today. In times of a shortage of skilled workers, a well-coordinated team that accompanies the entire production process is worth its weight in gold. This allows us to guarantee high-quality production and manufacture very economically, even with fewer staff.
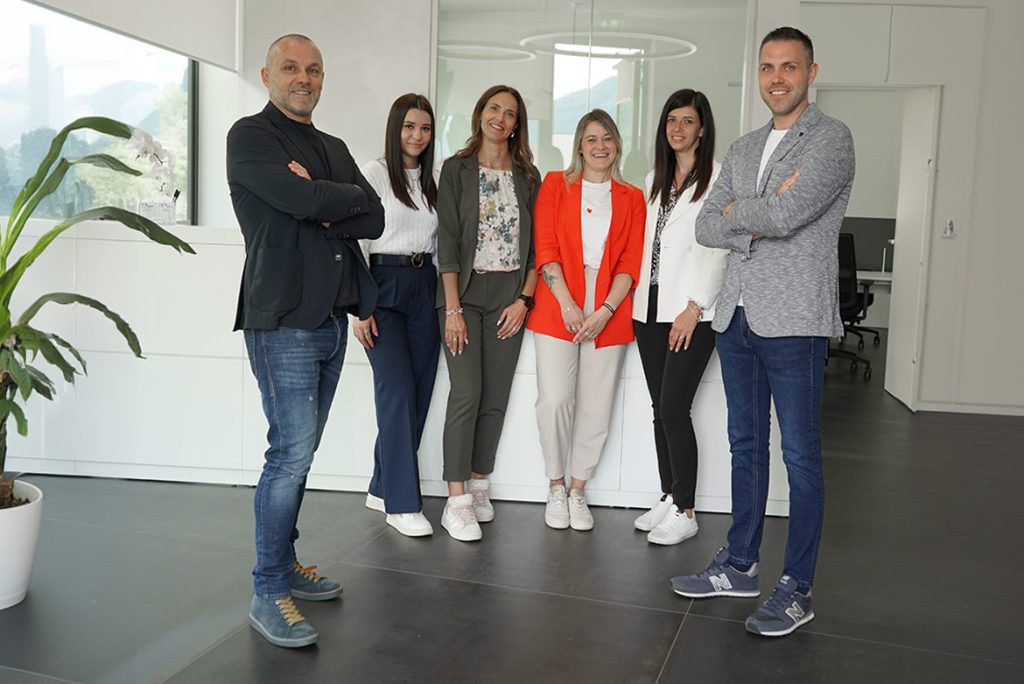
Proud of what has been achieved: Alessandro Reguzzo (left) with members of his team. The company is growing continuously and offers its employees a modern and future-oriented working environment.
What are your plans for the future?
We currently have several projects in the pipeline, including a major project for an international customer. Here, components with a diameter of up to 450 mm are to be machined. To ensure efficient and precision production, we are planning to use two VL 8 machines in combination with robots. This will enable us to supply our customer with a finished component that has been completely manufactured on our machines. We would also like to further develop the technologies of gear cutting and assembly in order to be able to offer our customers even more comprehensive solutions.
What about servicing and maintenance of your machines?
Smooth service is crucial for our production. We have an internal department that takes care of proper and extraordinary servicing. In addition, we work with external service providers to ensure that our machines are always in perfect condition. With a production of 80,000 components per month, we cannot afford any downtime.
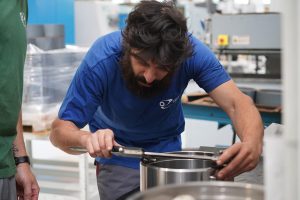
Quality control is a crucial step at MR Components. It ensures that every component meets the highest precision requirements.
Thank you very much for this comprehensive insight into your company.