The monthly number of new registrations of e-cars in Europe is currently increasing – and with it the required quantities for the e-drive components. The example of the supplier Linamar Technology Hungary shows how the production task behind this can be solved effectively. The e-drive specialists have recently invested in EMAG machines for the production of shafts and gears. A conversation with István Bíró, Project leader at Linamar Technology Hungary, about the new solution at the site in Békécsaba.
Mr. István Bíró, how would you describe your company’s know-how?
István Bíró: Linamar is a globally operating company. Among other things, we produce a large portfolio of components related to power generation and storage, electric drive systems and structural and chassis systems for e-vehicles. Our extensive engineering and manufacturing know-how make us a market leader here in terms of quality, system integration and time to market. One of Linamar’s central production sites for electric mobility is Linamar Technology Hungary. Among other things, we manufacture and assemble transmission components as well as aluminum housings and covers for a new e-car platform.
Why did you choose EMAG?
István Bíró: We have established various new production processes for the production processes around the new e-car platform. In the process, we were looking for a machine manufacturer in the market that offers a wide range of technologies. This is the case with EMAG. In addition, EMAG develops innovative solutions that help us to make our production processes leaner.
Where does EMAG technology come into play?
István Bíró: Specifically, we use the VL 6 and VT 2-4 vertical lathes for hard machining of various gears and the VLC 200 GT vertical turning and grinding center for machining shafts. We also have the ELC 160 for the laser welding machining of gears.
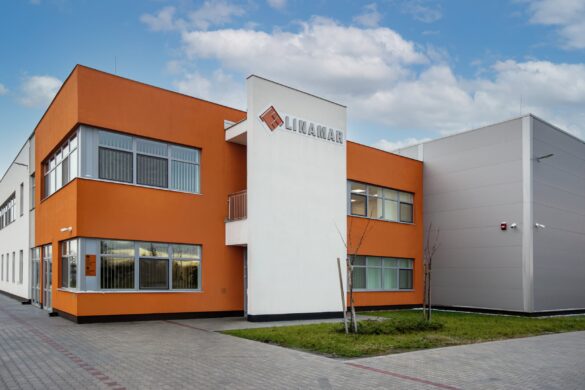
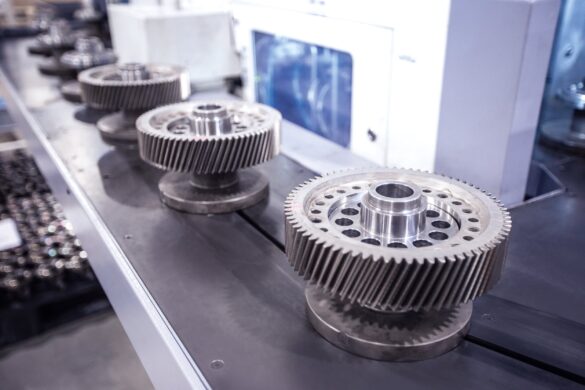

What experience have you gained with these solutions?
István Bíró: First of all, I must emphasize that the machines are very rigid and precise, as well as having good performance. Overall, we are talking about very high volumes here. In this respect, the process reliability of the overall solution is important. That is absolutely the case here.
Can you highlight a particular process in this context?
István Bíró: The VLC 200 GT turn-grind center is used for various gears. After the spindle has assumed its machining position, hard rough turning first starts. Only a residual allowance of a few micrometers then remains on the gear wheel. This ensures a significantly shortened grinding process with the grinding spindle in the VLC 200 GT. In this way, we can dispense with a further grinding operation.
What phase are you currently in with regard to establishing the new production processes, and what will happen in the next few months?
István Bíró: We are still in the start-up phase and produce around 60,000 parts per type and year. In the future, however, we will produce around 430,000 parts per type per year – around seven times as many. That is of course a huge increase, for which we are converting production – to one production cell per component type. Currently, we are still producing different types on one machine.
What is your conclusion after the first few months?
István Bíró: The machines ensure a very stable process. In addition, we have not yet fully exploited their potential. For example, we can reduce the measuring effort if we use the integrated measuring probes. Overall, we are very satisfied with the solution.
1 comment
With precision and consistency, the machines guarantee a reliable and stable process. Their meticulous performance ensures consistency, making them a cornerstone for dependability. This stability is not just a feature; it’s a commitment to excellence, reflecting the seamless synergy between technology and reliability in every operation.