There is no “one” best method for cleaning or de-coating workpieces. After all, the choice of method comes down to basic conditions and objectives in the production process. In this sense, laser cleaning is not a one-to-one substitute for traditional washing either but does frequently have an advantage.
Laser cleaning is extremely energy efficient and fast.
When exactly is a component satisfactorily clean or de-coated? The question sounds clichéd. But it is crucial when it comes to the configuration of any cleaning process since the cleaning process should ideally be configured in such a way that precisely the right amount of energy and time is used to remove the soiling or coating in question in a specific way. A simple way of putting this is “no more than necessary.” An unnecessarily complex and expensive process would be the opposite of this.
Pinpoint cleaning
This is where laser cleaning comes into its own: it uses a focused laser beam that is moved over the area to be cleaned by a scanner (and machine axes, if needed). The parameters for this method, like the output and pulse frequency of the laser, its feed motion and track width as well as the machining time, can be flexibly configured and perfectly adapted to the degree of soiling and the desired level of cleanliness. In addition, only defined areas and geometries are cleaned or de-coated. All these factors ensure the best possible cleaning performance along with an optimized cycle time. The motto “no more than necessary” is therefore very apt for this application, which not least keeps running costs very low. Washing machines, on the other hand, are real “energy guzzlers.” They require a lot of maintenance and the liquids and filters need to be disposed of regularly. They also require additional drying and flushing processes that slow down the entire production process.
Series or batch solution?
What is more, laser cleaning is a serial process, while washing involves batches or cycles. As a result, laser cleaning means far fewer parts in the cleaning cycle and, unlike batch systems, no waiting times. This means the entire production process can be optimized and configured as a one-piece flow. On top of that, laser cleaning takes up less space. For example, the LC 4 machine from EMAG has a footprint of just 4.5 square meters. It can be integrated in end-to-end production lines and used alone. To this end, it features a turntable that is separate from the work area. It can be loaded and unloaded by means of an automation system (or just manually) without interrupting operation. Optionally, two components can be clamped simultaneously, while two others run through the cleaning process.
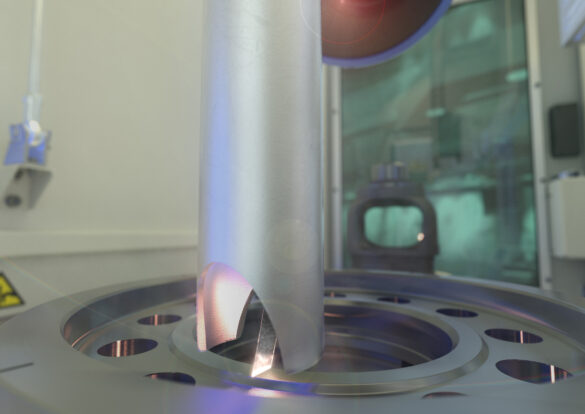
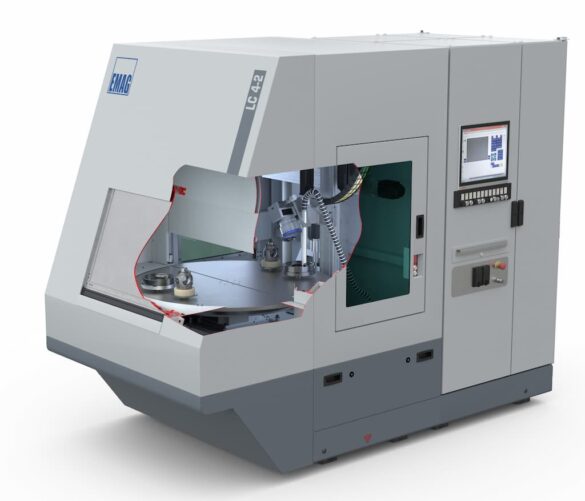
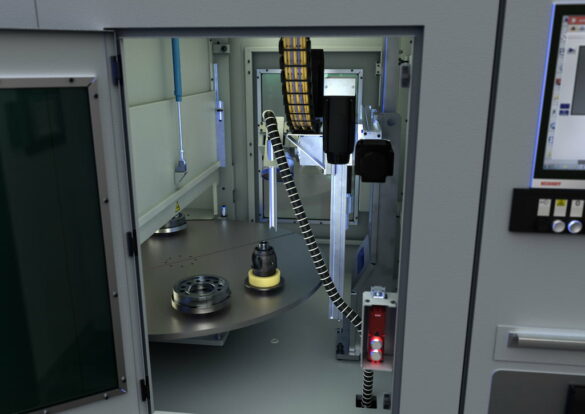
Type of soiling
Finally, it is interesting to take a look at the type of soiling. Laser cleaning is very well suited to removing thin layers of grease, coolants, and anti-corrosion coatings. The same goes for the alternative process of washing. However, some coolants, used in particular for minimal quantity lubrication, can cause problems during washing because of their chemical structure. This is not the case with laser cleaning. Chips and particles cannot be removed by laser. The washing process (with the addition of a chip strainer, for example) has an advantage here. On the other hand, laser is very well suited to removing paints, zinc-phosphate layers, cathodic dip coatings, powder coatings, oxides, and rust. Washing has virtually no effect in these areas of application.
EC Clean software from EMAG
Incidentally, the EC Clean software from EMAG used in the LC 4 machine plays an important role in the success of the laser cleaning process. With the help of this control software, laser cleaning becomes an easily managed process. All relevant settings like laser parameters, scanner parameters, geometry, feed rate, etc. are easily influenced with this solution. EC Clean assists the system operator with selecting settings. In concrete terms, this means the system operator can concentrate on a few settings like parts geometry, track width, and cleaning energy INSTEAD of becoming bogged down in complicated calculations. All other parameters are automatically calculated or taken from the internal technology database.
More information about Laser Cleaning Machine LC 4-2 you will find here…