What does retrofit do? The short answer – many things are possible. Depending on the customer’s wishes, the retrofitted machine not only has new components, but it is also equipped with new automation or additional tool technology. A turning machine, for example, becomes a turning-grinding center. Here we present just two examples among many possible scenarios.
1st Example: Technology and Automation Upgrade
Before: The VSC 250 model is around 20 years old, heavily soiled and with technologically outdated electronics and cooling unit. In addition, the mechanical components are worn out. How can this “old-timer” be transformed into a state-of-the-art version of the VSC 250 and at the same time integrate new technology?
After: The process takes place step by step. First, EMAG experts disassemble the complete machine down to the base body. The spindle then goes to a special area where the assembly is disassembled and cleaned and wear parts are replaced. The same applies to the rest of the machine – worn components such as guide rails, feed drives and various hoses are replaced, and the enclosure and complete exterior painting are renewed. In the example shown here, however, the retrofit is even more comprehensive, with the photo on the right showing an intermediate step in the process. Here, the retrofit is around 50 percent complete. Once completed, the pure turning machine will be a turning-grinding center, so that these processes can be used in combination or individually, depending on the machining requirements. And that means it will have a new headstock suitable for turning and grinding, a turret and a new Siemens control system. The result is equivalent to a new machine.
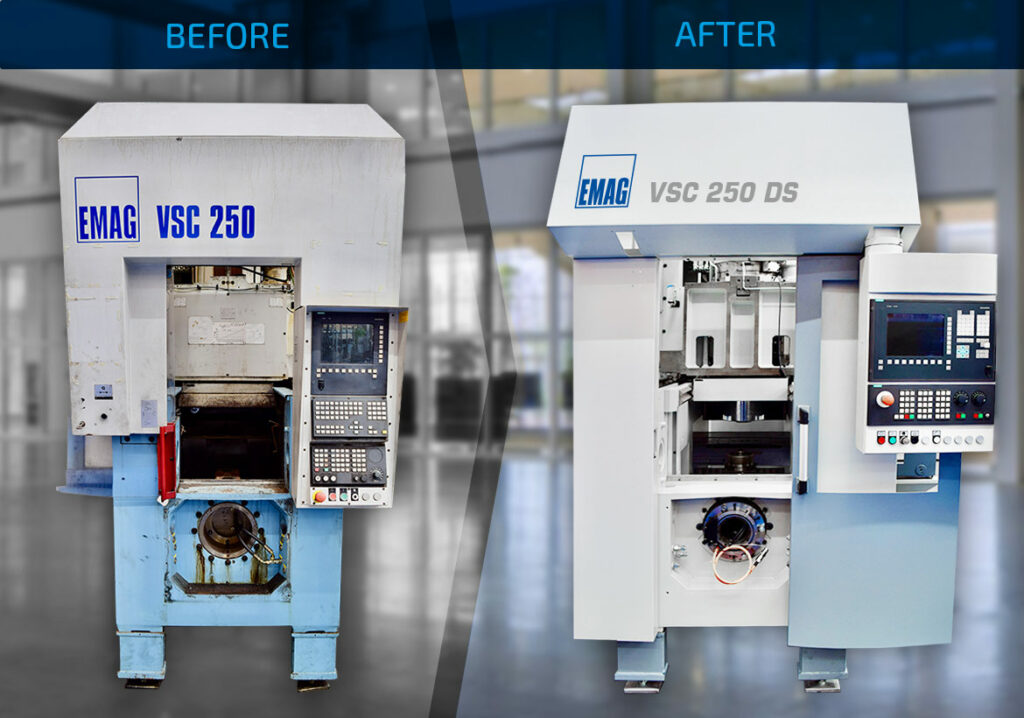
Two machines with (almost) the same name – but few similarities on the outside
2nd Example: Huge Development Steps
Before: The old Karstens K 11 machine from 1984 with its hydraulic drive and outdated geometry can practically no longer be used. Set-up is like a lottery game because the machine reacts to external influences, for example, and adjusts itself in the process and no longer works reliably.
After: Redesigning this technology in response to customer requests, EMAG Weiss included intuitive user interface, much shorter programming and set-up times and a modern machine enclosure with interlocked workpiece change door. In addition, the W 11 Evolution, shown here (the number is reminiscent of its predecessor), is expandable for external, internal and face-grinding processes. Servo-electric Z and X axes each guarantee highly accurate results. Manual processes for adjusting the headstock are a thing of the past. Nevertheless, operators who previously worked on the old machine still find their way around easily, because the basic design and various operating elements are comparable. The operator can, therefore, once again work economically and with less strain on single-item or small-batch production.
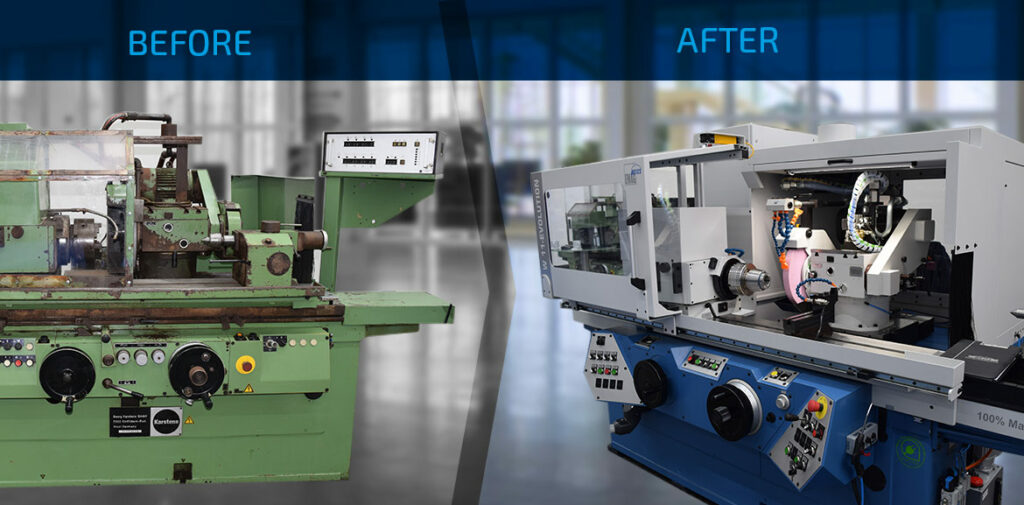
This result from “universal cylindrical grinding” is similarly impressive