The challenges for many contract manufactures and smaller manufacturing companies are increasing in the coming years – rising costs for purchasing raw materials, high energy prices and enormous OEM quality requirements point the way ahead. But there are also more and more production technology options for meeting these challenges intelligently. For example, various solutions from the latest generation of automation and robotics are highly interesting for many contract manufacturers. A conversation with Jürgen Maier, Head of the Turning Business Unit at EMAG, about the special possibilities of the EMAG approach.
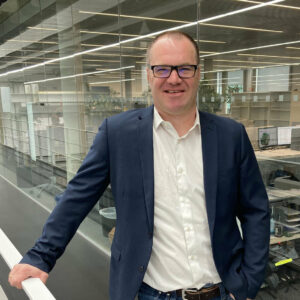
Jürgen Maier, Head of the Business Unit Turning at EMAG
Mr. Maier, why do contract manufacturers or smaller manufacturing companies rely on automation solutions?
There are many reasons. With the right automation, for example, you can make targeted labor savings in certain application areas, simplify production processes and, finally, reduce unit production costs. At the same time, it is quite easy, especially based on EMAG mechanical engineering, to develop individual solutions that ensure leaps in productivity.
What distinguishes EMAG mechanical engineering in this context?
Many of our machines feature pick-up technology – in other words, a type of internal automation that allows the machines to load themselves from a conveyor belt, for example. This approach can be combined very well with overarching automation systems, such as our TrackMotion system: a lift-and-turn carriage picks up raw-parts from a parts store and transports them to the machine at a speed of up to 150 meters per minute. Here, the pick-up spindle then simply takes over and feeds the part into the machining process. Very similar solutions are conceivable with robotic cells.
Which machines are suitable for this approach?
Very different machines with a wide range of technologies are available. The important thing here is that our “Modular Standard” or “Customized” machines have a uniform transfer height, software control and internal automation – the basic prerequisite for the amazingly simple link-up via TrackMotion.
Can you give us an example of how it is used by contract manufacturers?
There are very many applications. For example, the solutions of an Italian subcontracting company, which has a total of eleven VL machines from EMAG in operation in various production lines, are impressive. The lines are each completely link-up via TrackMotion from EMAG, with OP 10 and OP 20 running directly behind each other. The integrated solution not only guarantees high process reliability and quality, but also ensures economic growth, as the associated wheel/wheel hub production has thus become the most important area at this company.
Are there also solutions for one or two machines?
Yes, we also combine single machines with this automation solution – for example, a VL 3 DUO. The machine has two separate machining areas for OP 10 and OP 20. Each machining area is equipped with a powerful pick-up spindle and a turret with twelve tool positions. The TrackMotion automation system not only ensures fast parts transport between the parts storage and work areas, but also turns the components between OP 10 and OP 20.
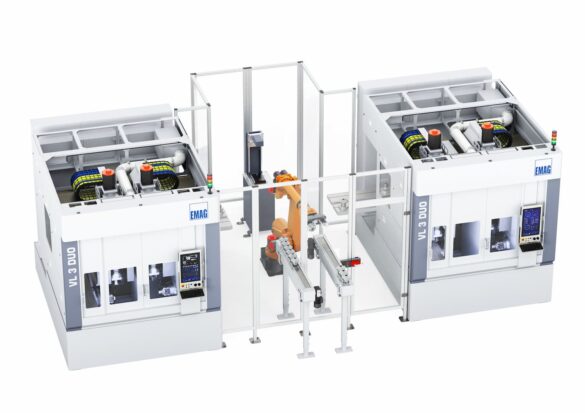
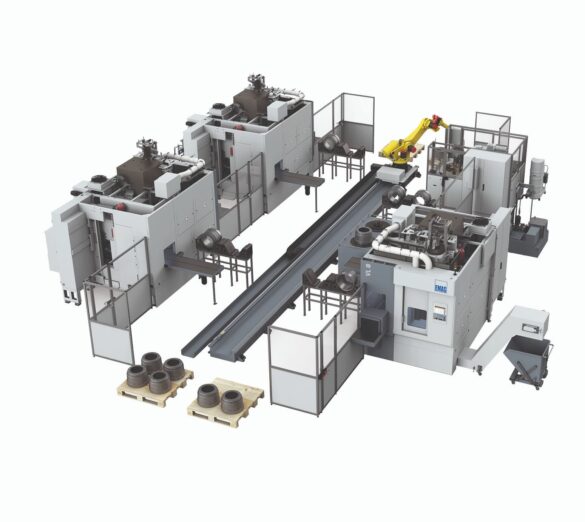
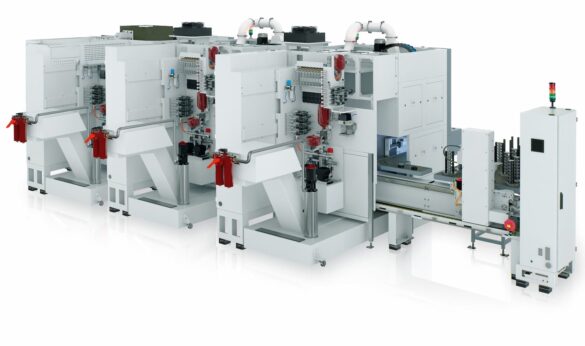
Finally, can you give us an example of the use of robots with EMAG machines?
Here, too, the focus is always on the requirements of the workpiece and the associated production process. The solutions are then very different depending on the task. The components are fed, for example, with infeed and outfeed conveyors, palletizers, drawers or by bin picking. The robot “operates” from these systems when it picks up new components or places finished ones, with each solution having different strengths and basic conditions. A good example of robot automation is the complete machining of truck drum brakes. Here, a robot is used for loading four VL 8 machines, whereby it can take the high component weight without any problems and then travels very quickly on a rail in front of the machines. The basic principle is thus like the “TrackMotion approach.”
How do you assess the market development of automation solutions for contract manufacture in the next few years?
This topic is becoming increasingly important because we provide extremely powerful and quickly adaptable systems. New machines, for example, can be integrated into the process at any time. Under these circumstances, contract manufacturers and suppliers in particular will also benefit. They produce faster, less error-prone and more cost-effectively.
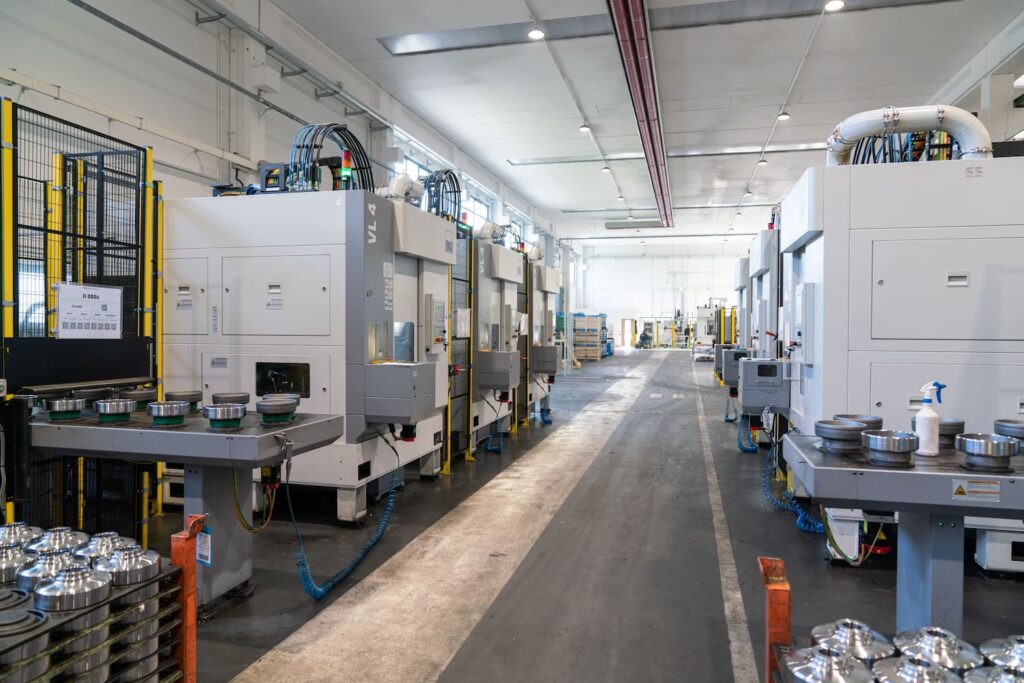
EMAG production lines at Pucktechnik. The TrackMotion automation system not only ensures fast parts transport here, but also turns the components between operations.