“Our customers are faced with the task of manufacturing complex components to the highest quality and in the shortest possible time. As a product manager, I support them in optimizing their production processes. With our new robot cells, we offer tailor-made solutions that not only increase productivity, but also improve working conditions. For us, automation is not just about technology, but about looking at the entire value chain.” Jan Gotthold, Product Manager in the EDNA Automation team, gives insight into the new robot cells from EMAG. In the following interview he explains why they offer real added value for many applications.
EMAG now offers a wide range of different robot cells. How do the MRC robot cells differ from the CRC and SCS cells?
The SCS 4 is purely a basket stacking cell. It receives the basket stacks on floor rollers and handles the complete logistics – from the provision of the baskets for loading and unloading to the storage of the gauge baskets as well as the discharge of the loaded baskets. Thanks to its internal buffer spaces, it offers a very high degree of autonomy and can be used for both raw or finished parts and their logistics.
The CRC (Compact Robot Cell) is, as the name suggests, a small robot-based automation solution for loading and unloading our machines. The workpieces are fed via a drawer system to which our customers’ workpiece carriers can be adapted. The CRC offers the possibility of a completely cycle time-parallel pallet change by the worker and is, therefore, ideally suited for handling small to medium-sized workpieces with short processing times.
The MRC (Modular Robot Cell) is the CRC’s big sister, so to speak, and is characterized by greater flexibility and modularity. Workpieces can be fed here in different containers. An optional camera module can even be used to remove raw-parts from the bulk material. It is also possible to combine different container types. For example, raw-parts such as saw cuts are fed as bulk material in a mesh box and the finished parts are stacked in wire baskets. Additional functions can also be easily integrated into the cell.
EMAG already has a large number of automation systems and has often used robots in manufacturing systems in the past. What are the new robot cells needed for?
The new cells are all platform-based. This makes them crane- and forklift-compatible. This means that our customers benefit from shorter installation and commissioning times on site. We have also explicitly placed great emphasis on universality in the design and development of the MRC. This enables us to achieve shorter project throughput times and, therefore, a significant reduction in delivery times. Since the modular robot cells are highly standardized, they are attractively priced.
What are MRC robot cells used for?
The cells are primarily used for loading and unloading, but also for the link-up of our processing machines. Furthermore, the MRC offers space for the integration of additional secondary processes such as buffering, deburring, blowing off, measuring, marking, etc.
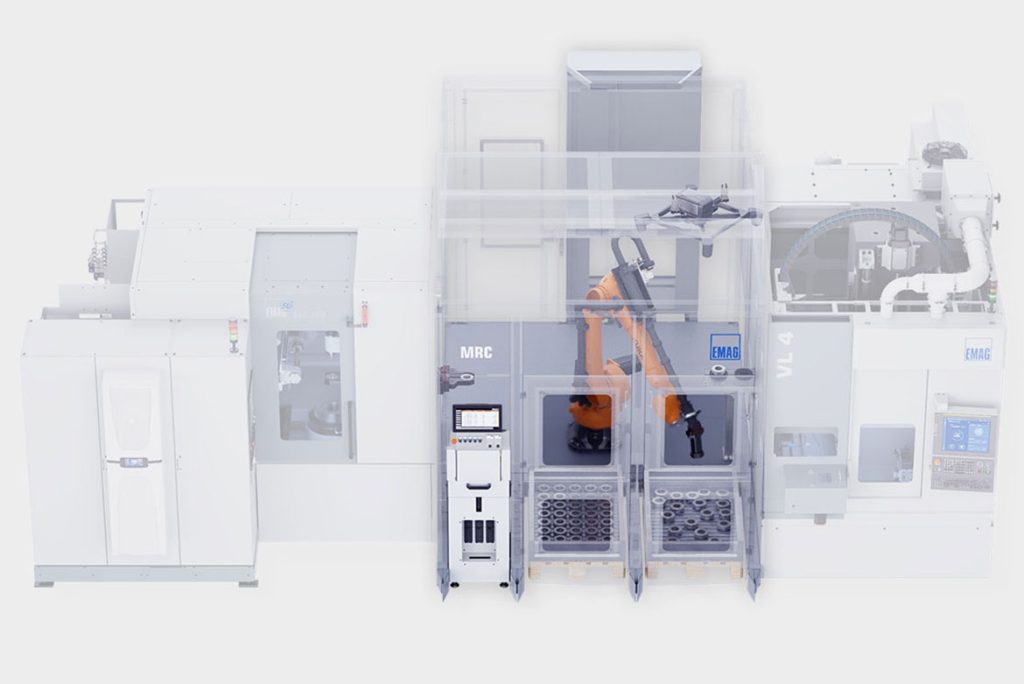
The MRC robot cell from EMAG is characterized by its versatility. In addition to the core functions of loading and unloading machine tools, it offers the option of seamlessly integrating a range of additional functions. These additional functions extend the range of applications and significantly increase the efficiency of the overall system.
What added value do EMAG robot cells offer our customers?
The same as you are already familiar with from our established automation solutions such as TrackMotion and our modular portal system: You receive a complete, CE-compliant manufacturing system from a single source and have just one contact for machining and automation. This eliminates a high level of administrative effort and the responsibilities are clear during commissioning on site. We are then the point of contact for all matters relating to the manufacturing system. Our customers also benefit from our efficient and global service during subsequent operation.
EMAG is known for machine tools, where does our expertise in robotics and parts handling come from?
As already mentioned, we at EMAG have had good and established automation solutions in our portfolio for a long time. Our line gantries are still the right solution for many applications. The same applies to our TrackMotion Automation, which already has 3 handling axes (horizontal, vertical and rotation). With the additional 3 axes of a traditional articulated arm robot, we can move away from the linear arrangement and gain more flexibility in the layout design. A robot is also much more tolerant in terms of the alignment of the individual processes to each other thanks to its 6-axis kinematics.
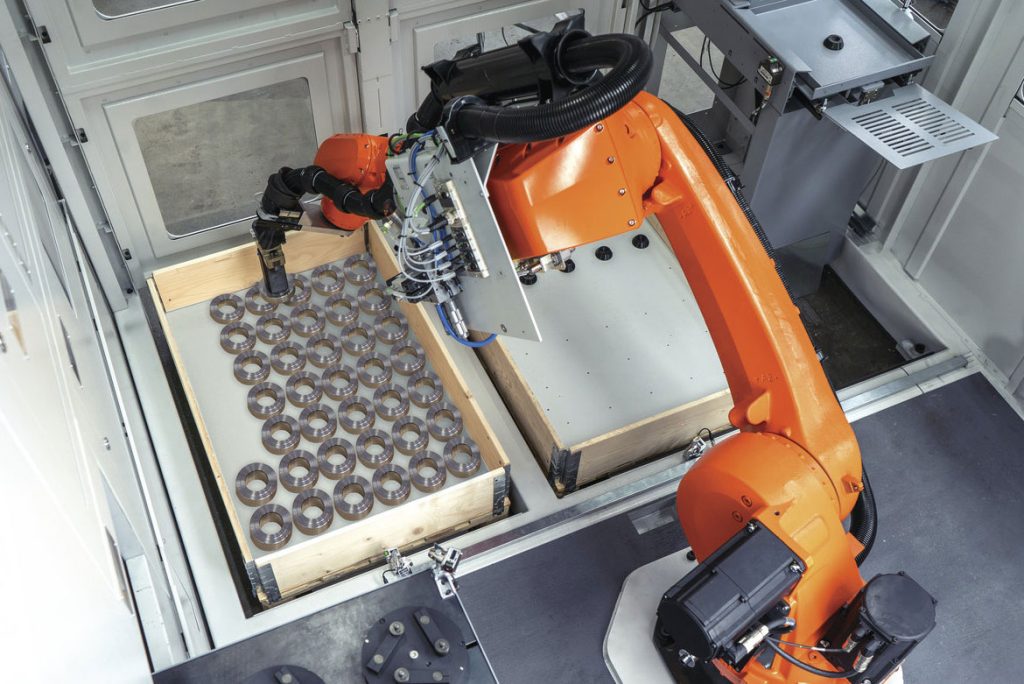
The MRC cell can remove workpieces from various containers such as mesh boxes, wire baskets and pallets and feed them to the machine tools.
What advantages does EMAG have over its competitors?
We have defined interfaces between the machine and automation internally, which are completely under our control. This makes us not supplier-dependent. Thanks to close project coordination, we know the production and workpiece requirements of our customers very well and also the pitfalls that may arise. This enables us to optimally design the machines and automation solutions to meet the requirements.
But these are just the technical aspects. Automation is also becoming increasingly important in organizational terms due to increasing digitalization. Order management and the connection to process control systems is often carried out via the automation, which is located above the machines in the production pyramid. Being able to operate this level directly offers our customers real added value, as we can make the information from the machines and automation available very easily. The key words here are interface reduction and standardization.
What additional potential do the new robot cells offer?
At the AMB, we demonstrated direct loading into the spindle of a VLC 200 with our CRC. With the robot cell, the classic O-belt or shuttle can be dispensed with on the one hand, and on the other hand we achieve significantly shorter workpiece changeover times and, thus, even higher output quantities thanks to the twin-gripper.
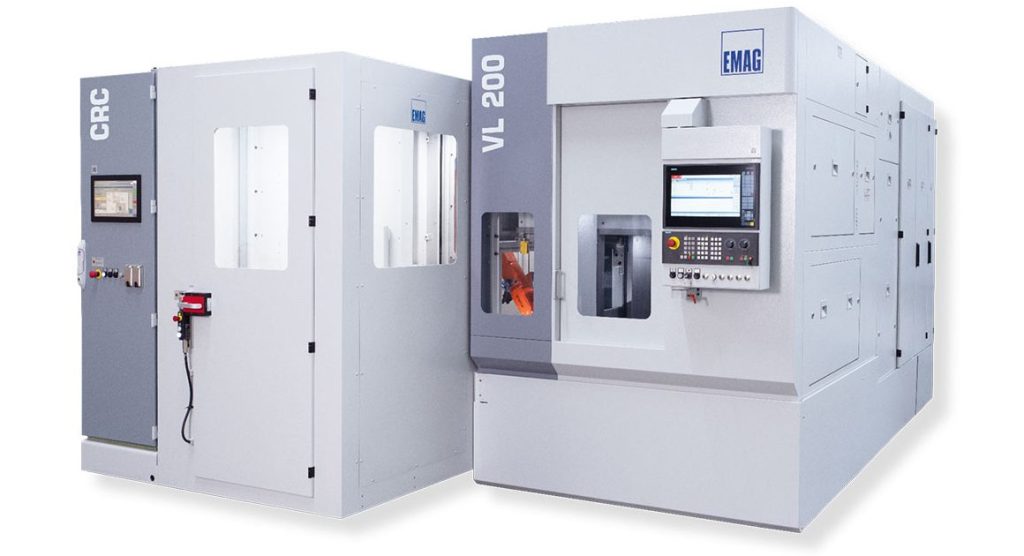
The CRC stacking cell is perfect for components with a diameter of up to 200 mm. It is loaded using workpiece carriers, which are housed in drawers and can carry up to 45 kg per drawer. A robot handles the components and loads and unloads the machines. The machine operator is only responsible for changing the workpiece carriers. This takes place simultaneous to the machine’s main time in order to ensure a continuous production flow.
There is also great potential for automation in the area of internal logistics. In many places, manual industrial trucks are being replaced by AGVs (automated guided vehicles). For this type of loading, our MRC offers an intelligent concept that does not require a safety-related interface to the AGV, which in turn significantly reduces the integration effort.
Furthermore, the robot can take on additional activities beyond simply loading and unloading the machine. This can be (almost) anything from blowing off and measuring to labeling.
Why is bin picking a particularly interesting automation process in production?
Bin picking offers real added value, especially at the very beginning of the value chain. Raw-parts such as cast blanks or saw cuts are usually transported as bulk goods in boxes. Camera-assisted bin picking eliminates the need for tedious manual or time-consuming mechanical pre-separation.
What role does AI play in robotics?
So far, we have been working in the field of classic industrial automation. I see great potential there in the area of workpiece recognition in order to minimize set-up times and, for example, to automatically generate gripping positions for new workpieces from already known components. This topic will become really exciting in connection with humanoid robots, which will increasingly find their way into production environments sooner or later.