Faster than shaping, more flexible than hobbing and broaching – in this context, power skiving is a highly effective alternative for gear production. With the new VSC 400 PS machine, EMAG puts the crown on this approach by providing up to four power skiving tools and six turning tools, ensuring highly effective combination machining. And, its operation is simple. A conversation with Daniel Nille, Head of Technology Development at EMAG Maschinenfabrik, discusses the possibilities of this approach and the potential returns of investment.
Mr. Nille, where is power skiving used?
The process is very flexible. It can be used to manufacture internal and external gears. It is around 50 percent faster than gear shaping and also more flexible than gear hobbing because it can also be used to produce internal gears. In addition, hobbing requires a relatively long runout on the component, which can be significantly shorter with power skiving. In any case, the result is high gear quality. Under these circumstances, power skiving is often the best solution.
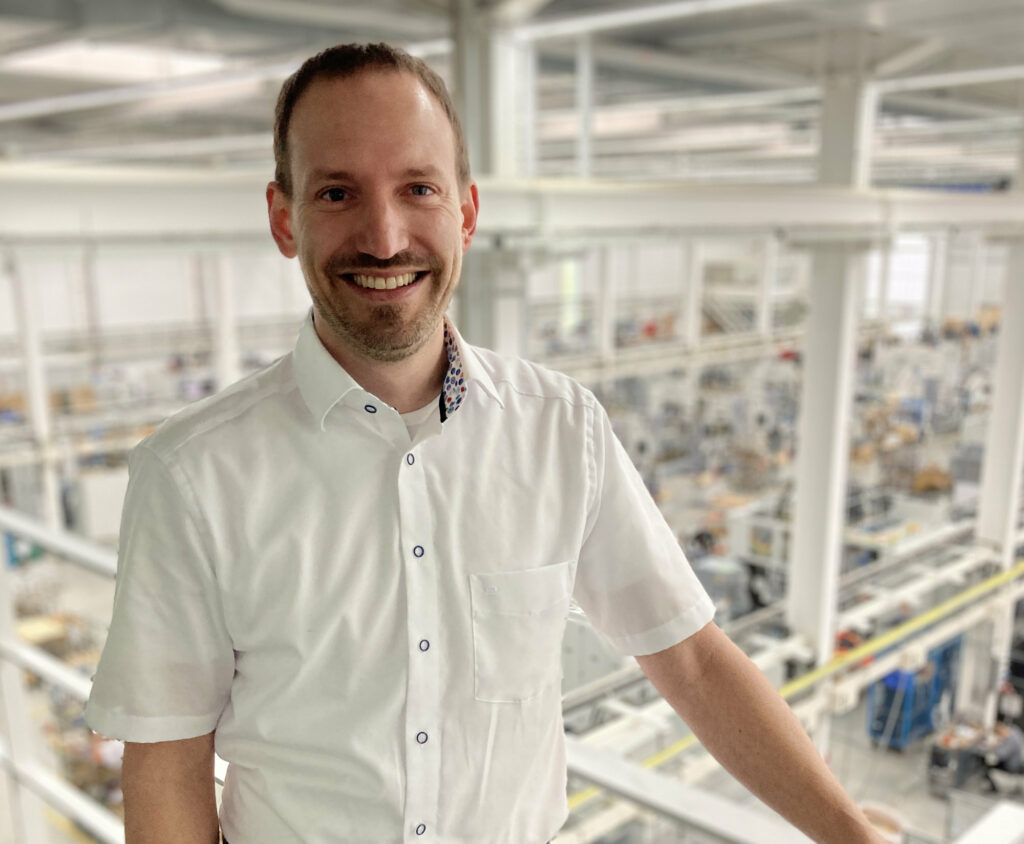
Daniel Nille, Head of Technology Development at EMAG Maschinenfabrik
What approach are you now taking with the new VSC 400 PS machine?
First, I must emphasize that it has been developed specifically for power skiving based on a proven machine, and we have designed the entire process to be very flexible and fast. As a result, the machine has two spindles, each with two power skiving tools and up to six turning tools. As a result, pre-turning and subsequent power skiving can be carried out in rapid alternation and in a single setup. It is also conceivable to carry out rough-machining and subsequent finish-machining – each with different power skiving tools – in quick succession. A third possibility would be to produce four different external and internal gearings with four different tools. This benefits component quality because the position of the tooth profiles can be perfectly aligned with each other. So, you can see that the possibilities of the VSC 400 PS are immense.
What advantage does this combination machining have for users – couldn’t different machines simply be used here?
Theoretically, this would be possible – but only with major disadvantages. After all, the investments are higher this way. In addition, the combination process in one machine is much faster, because pre-turning and power skiving or the production of different tooth profiles take place in a fast change. This speed ultimately ensures significantly lower unit production costs. In addition, combination machining naturally also has considerable advantages for component quality. For example, the tooth profiles can be produced in one setup with the gear cutting and thus have the best possible concentricity with respect to each other.
It is also possible, for example, to deburr the tooth profiles directly in the same setup.
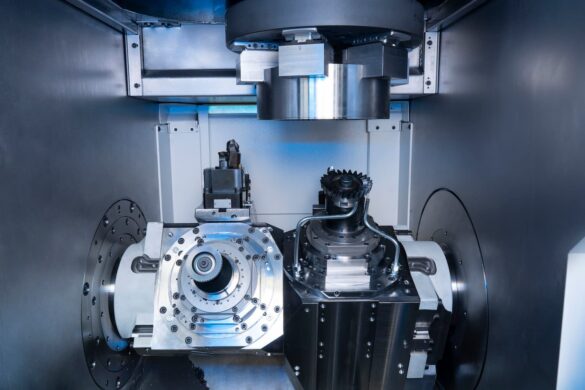
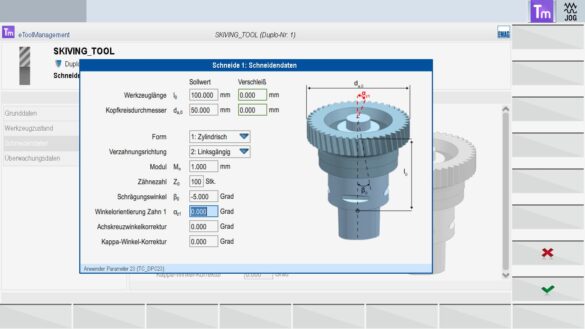
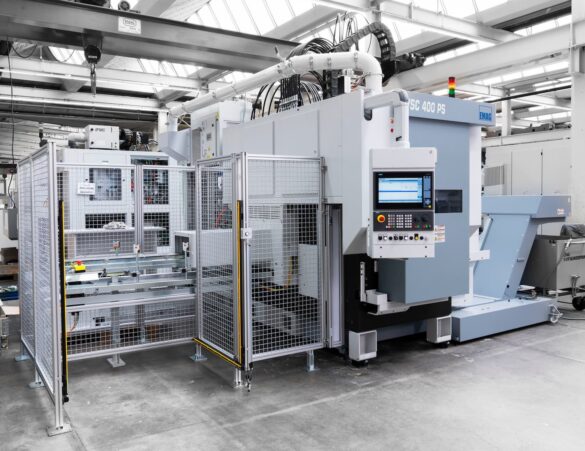
How demanding is the operation of the machine?
We have placed a great deal of emphasis on massively simplifying the entire operation. As a result, there is hardly any need to be familiar with the process. Basically, the operator only enters the desired gear tooth values of the component, the values of the available tool data sheet and the cutting values, and our intuitive user interface greatly simplifies this work. The machine does the rest. It independently calculates the entire machining program for the power skiving process. In addition, the gear cutting can be corrected quite simply by entering the tooth values already measured. Here, the operator is supported by interactive images and automatic safety prompts.
How important are the technical details of the machine for the efficiency of the process?
I have already mentioned the numerous variants for tooling. In addition, the B-axis allows a large variance of axis cross angles – this is more or less the feed angle of the tool, which is always arranged at a slight angle to the component during power skiving. It is due to this inclined position that the actual cut is made. In addition, the symmetrical design of the machine ensures a closed force flow and optimum thermal behavior, which in turn benefits the accuracy on the workpiece. In addition, the hydrostatic guideway ensures that vibrations are dampened. As a result, significantly longer tool lives are achieved.
In addition, a specially tuned electronic gearbox is used in the machine, which ensures a very precise transmission ratio between the tool and the workpiece, even for smaller components. In this way, very high cutting speeds can be reliably achieved in combination with HSS or carbide tools.
What market opportunities do you see for the whole approach?
We expect growing market opportunities. Thanks to the further development of power skiving tools in recent years, this process has become much more attractive and is being used more and more in industry. For example, it can be increasingly used in the production of internal gears for planetary gearboxes (which are required for many electric motors). In addition, the process enables more efficient production of demanding component geometries.
More Information Power Skiving