With the Health Check, EMAG offers its customers an IoT tool for the health assessment of feed axes and spindles in order to better plan their maintenance periods. In addition, EMAG is constantly developing this solution further, as Patrick Kaiser, data scientist at EMAG, emphasizes in the interview: “The experience and our service flow into this in a targeted manner.”
Mr. Kaiser, what role do IoT solutions generally play for EMAG?
They are becoming increasingly important – also and especially because they can be used to create real added value and tap into new optimization potential. And that is precisely our goal as a machine manufacturer. Consequently, we use data analysis and machine networking to make service more effective, for example.
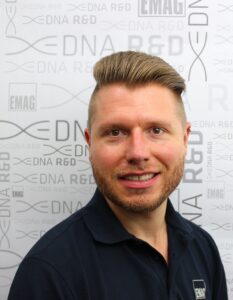
Patrick Kaiser, Data Scientist
Isn’t the implementation of these solutions always a big effort?
In recent years, we have worked very specifically on massively reducing this effort – with the development of EDNA. This is our software ecosystem for the development of IoT applications, which reduces the manual effort involved in their implementation. The Health Check – a semi-automatic health assessment and early warning system for feed axes and spindles on lathes – is now also based on this.
The term “predictive servicing” has been heard very often for years. What characterizes EMAG’s approach here?
First of all, it must be emphasized that the health check will be a combination of different techniques in the future – the design and development is currently underway. In future, there will be elements of predictive servicing as well as condition-based servicing and condition monitoring. In the former, the condition of the machine is determined using models. Condition-based servicing, on the other hand, always starts as soon as a threshold value is exceeded. With condition monitoring, certain conditions are documented and visualized, which in turn forms a basis for the organization of servicing. We bring it all together in one solution.
What does the practical implementation look like?
It all starts with 3D acceleration sensors, which we use to measure vibrations, and an industrial PC that is connected to the machine’s control system. It records this production and sensor data using the EDNA Cortex software. This is the technical basis for the Health Check. Depending on the variant of this solution, different apps are available for users, as there is a full version, which we simply call Health Check, as well as Health Check Lite.
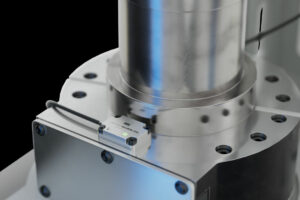
Vibrations are recorded with the help of 3D acceleration sensors.
What is the difference between the two versions?
With the full version, the measurements addressed are carried out automatically and transferred to EMAG, where a health assessment is carried out directly on the basis of models, which in turn are based on empirical knowledge. The result is displayed on dashboards within a few minutes and can be viewed by users via an app. At the customer’s request, a manual assessment can also be carried out by EMAG experts.
With Health Check Lite, the process does not take place automatically. Here, the user starts the program manually to record vibrations. The results are sent to EMAG by e-mail for detailed analysis. The Health Check Lite, therefore, has no direct access to the analysis software in the EMAG network. However, the subsequent evaluation is also based on models.
How can you imagine the results?
The health values of the feed axes and spindles are displayed in the form of prediction charts – a line graph with individual points, where each point represents a measurement. To calculate the final health values, we smooth the results to avoid unnecessary focus on outliers. At the end, the customer sees a trend that is easy to read. This creates a valuable early warning system for servicing – because the interpreted vibrations can indicate bearing play and damage, spindle vibrations at standstill or other interference frequencies, for example.
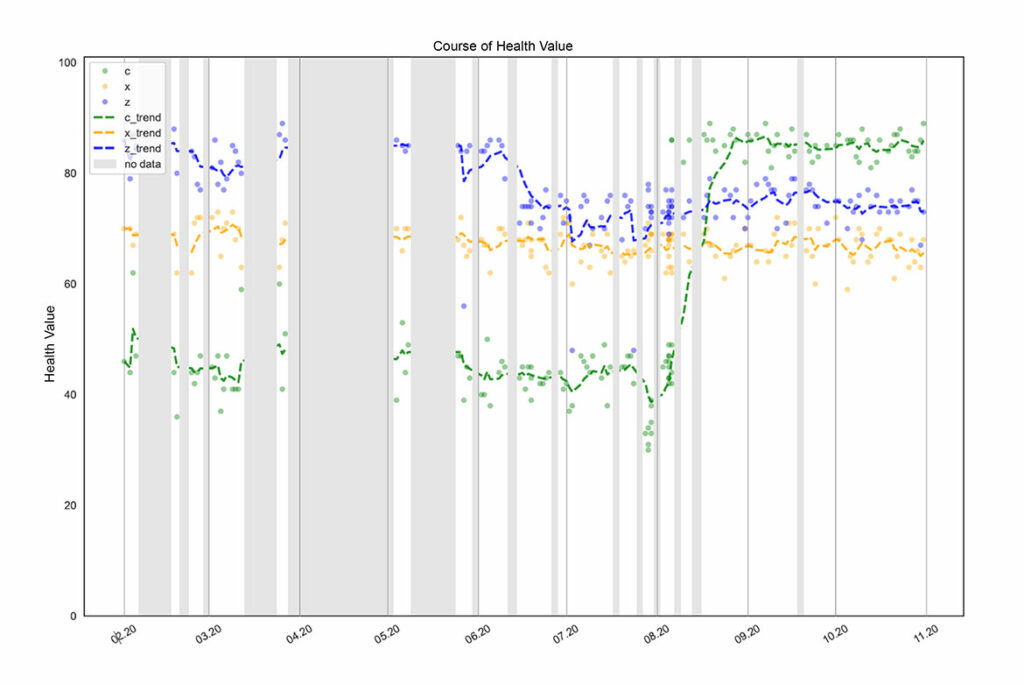
Example of a forecast chart in the EMAG Health Check
In the end, the question of current designs and developments remains: What’s new with the Health Check?
We are continuously optimizing this solution. The service’s experience and other findings from the ongoing use of the health check are incorporated. For example, we currently have a mobile health check on the roadmap, in which EMAG Service uses various sensory equipment to collect data on site at the user’s premises and evaluate it directly using AI. In this way, machines that are not yet “IoT ready” can also be checked in the future.
We are also currently working on a health check measuring kit. It could be used in the future if certain problems occur regularly on a machine. You can then simply use a mobile IPC to document measurements over a certain period of time – without the technician always being on site. The data collected is then analyzed and the cause rectified if necessary.
For more information visit also the EMAG Health Check on our website.