At first glance, it seems quite simple: brake pads press against the brake disk, friction is generated and the vehicle slows down – this is the basic function of the disc brake. In reality, however, a great deal of know-how goes into this car system. What is important in detail?
1. What characterizes the system in detail?
Disc brakes have been used in cars since the 1960s. They are more stable under continuous load than drum brakes. The system is controlled by hydraulics: when the driver presses the brake pedal, a hydraulic cylinder transfers brake fluid – separately in two pressure circuits, so that the entire system does not fail immediately in the event of punctual damage. As a result, pistons on the discs are activated and compress the brake pads. Interestingly, further developments to this seemingly simple system are complex. As a safety-critical component, the brake is subject to extensive design, testing and approval procedures, as the interaction between the brake disc and brake pad is demanding at a detailed physical level. Experts speak of two “friction partners”, which also indicates that both components are subject to wear. Incidentally, the maximum braking force is determined by the so-called static friction of the wheels – not by the brakes.
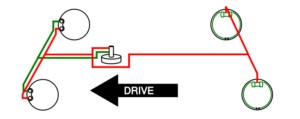
Cars usually have two pressure circuits so that the entire system does not fail in the event of localized damage.
Source: VentYl, Public domain, via Wikimedia Commons, https://upload.wikimedia.org/wikipedia/commons/4/46/Brzdy-S130.png
2. Who invented it?
The Brit Frederick W. Lanchester is considered the inventor of the disc brake for passenger cars. He applied for a patent in 1902, and his (still purely mechanical) technology was installed in vehicles from 1905. The first hydraulic brake system was developed by the American Malcolm Loughead, for which he applied for a patent in 1917. Another major step forward was the invention of the hard coating of brake discs, including the self-reinforcing brake system, by German engineer Herman Klaue in 1940. The first European production vehicle with disc brakes on all wheels was the Austin-Healey 100S roadster. It was built by BMC in England from 1953 to 1959.
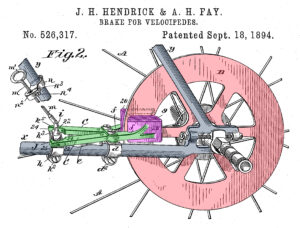
Patent for a disc brake for bicycles from 1894: The basic principle that is still valid today is used here.
Source: Joel H. Hendrick & Arthur H. Fay, Public domain, https://upload.wikimedia.org/wikipedia/commons/f/ff/1894-09-18-Patent-526317-Brake-for-Velocipedes-2a.jpg, via Wikimedia Commons
3. How is the system changing?
The EU’s planned Euro 7 standard changes the starting position. For the first time, the standard not only regulates emissions from combustion engines, but also the abrasion of brakes and tires. The car will therefore be considered as a whole, and particulate emissions from the braking system will have to be greatly reduced. Depending on the model, a car currently emits between 5 and 40 milligrams of particulate matter per kilometer (WLTP driving cycle). In future, the upper limit for all (!) vehicles will be just 7 milligrams. As a result, researchers are working on brake discs and brake pads, as their interaction generates particulate matter. The focus here is on the approach of coating conventional brake discs in such a way that corrosion, wear and fine dust hardly occur any more.
4. What role does e-mobility play?
In electric cars, the brakes are used less frequently because sufficient braking effect is generated during motor recuperation – and the unused brake disc may even begin to rust. In this context, it is interesting to note a TÜV report from 2023, which lists defects in the brakes of electric cars with an above-average frequency. The experts even speak of the brake pads “falling asleep” and recommend that e-car drivers regularly apply the brakes more forcefully.
5. What does all this mean for production?
Coating brake discs to reduce wear is not a new idea. However, there have been a number of problems to date – from high production costs and complex preparatory work to disruptive coating thicknesses. In this context, EMAG offers a new additive process in cooperation with HPL Technologies. In this process, material powder is specifically transported into the focus of a laser beam, where it melts while still in the air and hits the surface of the brake disc, which is also melted.
1 comment
This article provides a clear and concise explanation of how car disc brakes work. I found the breakdown of the different parts and their functions particularly helpful. It’s informative to learn how disc brakes offer improved stability compared to drum brakes. Overall, this blog post is a valuable resource for anyone interested in understanding car brake systems.