CV joints are indispensable, especially in vehicle construction. Their greatest strength: they transmit the rotational movement between two shafts completely uniformly. As a result, there is no “jerking” or similar, which would put unnecessary strain on all the components involved. We have compiled some fascinating information about this invention here.
1. What characterizes the construction?
At first glance, the CV joints look somewhat complicated – a network of balls, ball guides and a cage. At second glance, however, an ingenious design is revealed that transmits rotary movements evenly from the drive shaft to the output shaft. There are many designs, but this construction is the most common:
- A cup-shaped unit with flutes on the inside sits on one end of the shafts.
- The other end of the shafts has a crowned head piece with external grooves.
- Both components are geared profiles with balls in the flutes, allowing the shafts to flex smoothly while transmitting power.
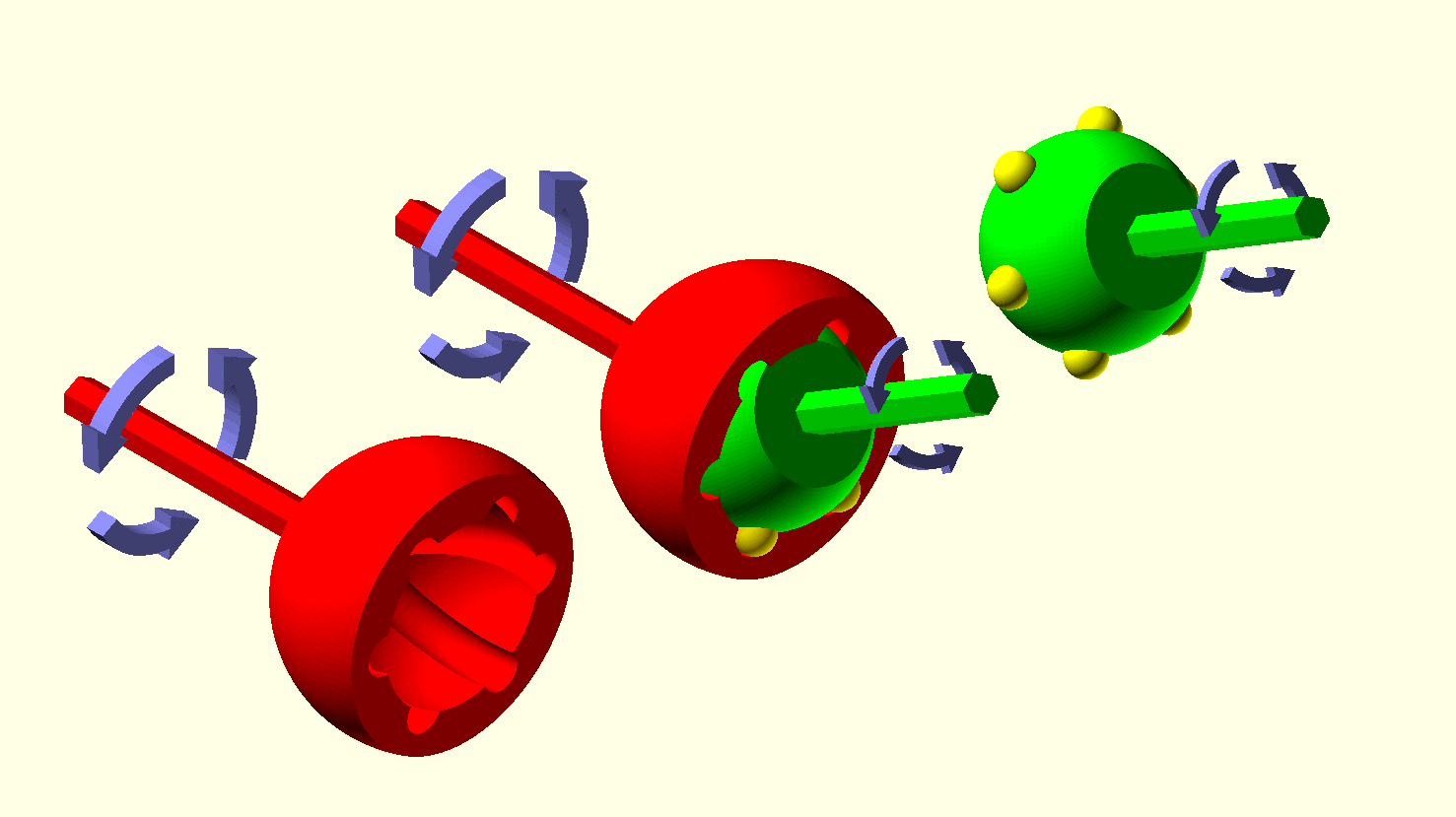
Universally applicable for even power transmission: the CV joints.
Source: By MichaelFrey – Own work, CC BY-SA 4.0, https://commons.wikimedia.org/w/index.php?curid=68021741 / https://creativecommons.org/licenses/by-sa/4.0, via Wikimedia Commons
2. Who invented it?
It is not uncommon to have to transmit rotary movements between two axes that are at a certain angle to each other. One of the earliest solutions for this was the invention of the universal joint by Gerolamo Cardano in the 16th century. It is used in the cardan shaft named after him – but with a decisive disadvantage: with larger articulation angles, the power transmission is no longer uniform.
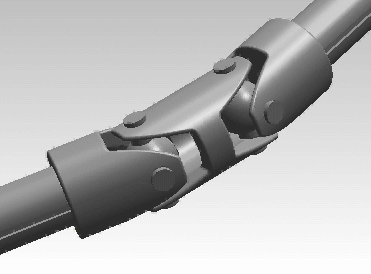
The universal joint is a type of precursor to the CV joints.
Source: Catsquisher, Public domain, via Wikimedia Commons
In 1926, Jean Albert Grégoire and Pierre Fenaille developed a shaft joint with an angular error-free drive – the first CV joints with a type of fork within the joint. It was needed for the first series-produced cars with front-wheel drive of the Tracta brand. To this day, some experts still refer to it as the “Tracta joint” when talking about certain CV joints.
Two years later, Ford developed the shape that is still most commonly used today, including the ball joint.
3. How sensitive is the whole thing?
It’s almost obvious: the small-scale construction with flutes and balls must not get dirty. For this reason, the entire technology is usually surrounded by a rubber axle boot, which can be clearly seen on the inside of the wheel. Incidentally, the whole thing is lubricated with a grease pack.
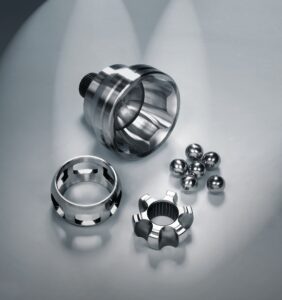
The components of the CV joints at a glance: Balls, cage, ball guides, axle journals and co.
4. Is servicing necessary?
Perhaps this is the most surprising fact about this topic: despite the small-scale design, the joints do not usually need servicing. Experts in car workshops tend to check whether the outer sleeve is cracked. Furthermore, the grease does not last forever. However, depending on the condition of the joint, it can also be “pressed in” from the outside.
5. And what does all this mean for industrial production?
The interaction between the ball groove (as a type of raceway) and the ball is physically complex. Forces act in all directions and the track must therefore be manufactured to an accuracy of just a few millimeters. The same applies to axle journals and joint cages.
Would you like to know which solutions are used here? Here you can see how cv joints can be machined on EMAG machines.