The e-bike market continues to boom – even if manufacturers have recently been unable to match the record figures from the pandemic. Nevertheless, around 1.6 million e-bikes were produced in Germany in 2023. In light of these large figures, it is particularly interesting to take a look at the central component: how exactly does the e-bike motor work, what characterizes its production and what changes are in store for the future?
1. Which engine are we talking about?
First of all, it must be emphasized that there are several types of motors for e-bikes. These include, for example, so-called hub motors, which are located in the middle of the front or rear wheel – with one major disadvantage: the handling is different compared to a normal bike. In this context, the mid-motor has established itself on the market. With its help, the e-bike rides like a “normal” bike.
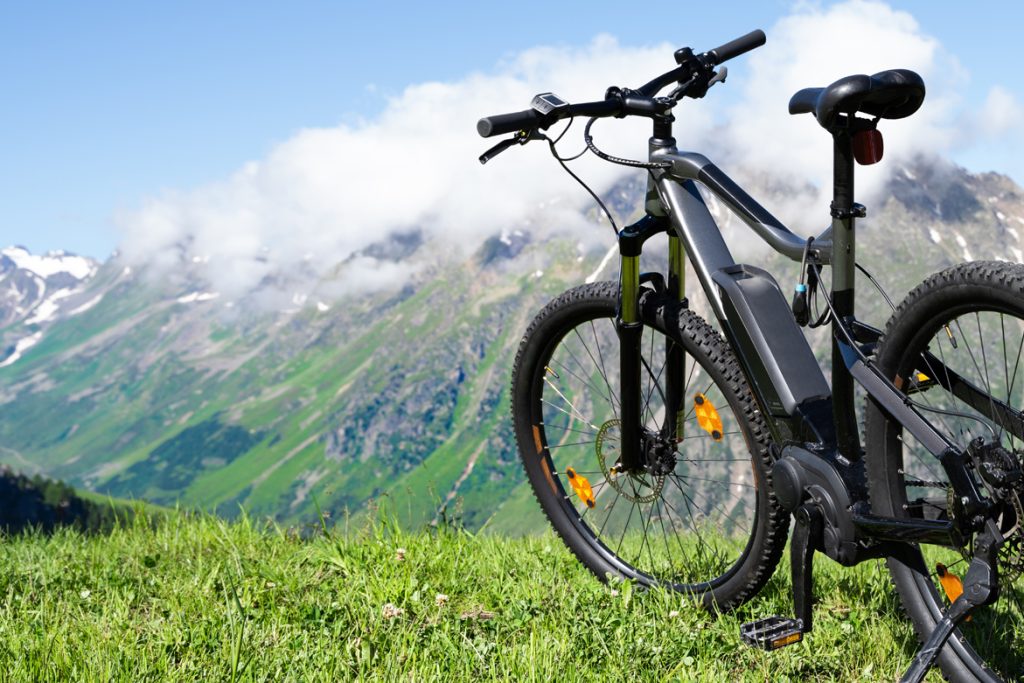
The e-bike motor has established itself, especially for high loads – such as mountain biking.
The motor control with motor speeds and torque sensory equipment ensures perfect pedal assistance – depending on the riding situation and settings. However, this also requires the mid-motor to be harmoniously integrated into the frame – in other words, the designers and developers have to design a special frame for this, which initially increases the design effort.
2. How is the mid-motor constructed?
E-bike motors consist (in simple terms) of a fixed stator and a moving rotor. As soon as voltage is applied, a magnetic field is created in the stator, which sets the rotor in motion. A constantly changing direction of current ensures that this movement continues. In e-bikes, so-called DC motors with magnets without carbon brushes are used, which increases durability. In most cases, this construction is located directly next to the crankshaft and supports the pedaling movement via a gearbox. Sensory equipment measures the motor speeds on the crankshaft and the torque on the chain. As a result, the e-bike motor can be controlled so that its torque always rises or falls in proportion to the rider’s pedaling force – which ensures an optimal riding experience. It is also interesting to take a look inside the entire motor, as it consists of relatively few components – including a few gears in the freewheel bearing, a control unit and the aforementioned bottom bracket shaft. The entire technology must be very stable.
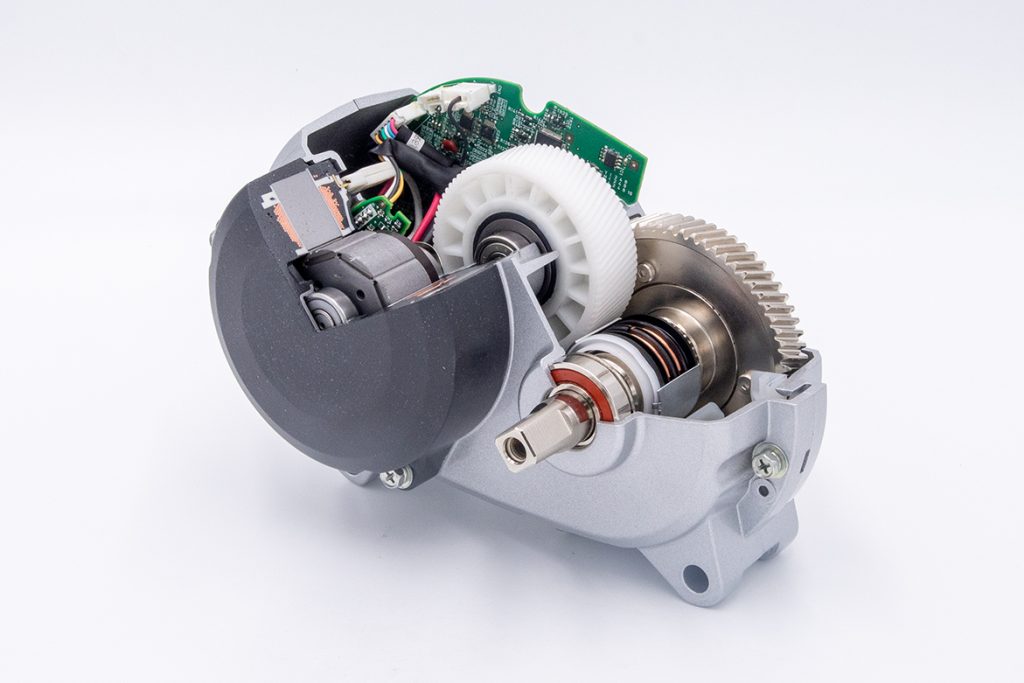
A cut e-bike motor showing components such as the stator, rotor and bottom bracket shaft.
3. What does all this mean for the production of components?
Stable components, a high degree of precision and enormously increasing quantities – in this context, production planners are currently focusing on the production of central components such as the bottom bracket shaft. The component actually has a fairly standard geometry (for example, with a spline at each end and a spline in the middle), but it has to be produced using three different hobbing processes. The first milling cutter makes a cut in the direction of the material. The second tool then mills the tooth profiles in the middle in synchronization. The third hobbing cutter is then used to produce the second spline.
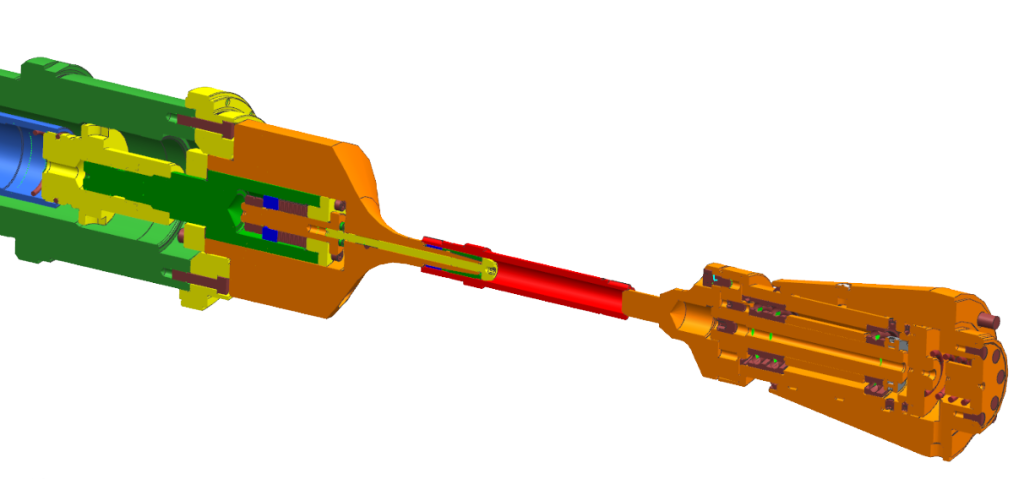
Gear cutting machining of an e-bike bottom bracket shaft. The shafts (shown here in red) are picked up once by the clamping device and then run through three different hobbing processes.
Overall, relatively small milling cutters with long shift paths are used – a complex task for the mechanical engineering involved, especially as the process must have a high level of process reliability. As an alternative, producers rely on electrochemical machining (ECM) – a process that is established in the aviation industry and in car construction. During the process, an electrolyte solution flows between the workpiece (the positive anode) and the tool (the negative cathode). This causes metal ions to detach from the workpiece. The process is completely contactless and ensures perfect surfaces for e-bike shafts.
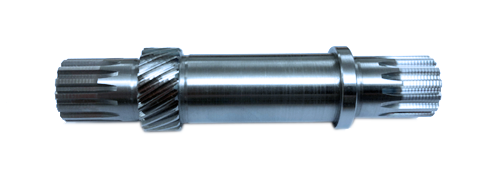
Small component – high load: The tooth profiles of the e-bike shaft require a rigid setup.
4. Where is the e-bike drive heading?
An interesting innovation in the e-bike motor is the chainless drive, which is used in cargo bikes, for example. It has no mechanical drive components such as chains, sprockets, pinions or belts. Instead, there is a “pedal generator” that produces electricity when pedaling, which in turn drives an electric motor on the rear wheel. In addition, manufacturers are generally working on perfectly networking all systems with each other – i.e. displays, batteries, sensors and smartphone apps in addition to the drive. As a result, it is possible to implement a “bicycle ABS” that controls the brake distribution between the front and rear wheels. It prevents the wheels from locking or slipping. Similarly interesting is a type of immobilizer as theft protection: if an unauthorized person (without a suitable digital key on the smartphone) wants to ride away on the bike, the motor assistance is not available and the bike is very sluggish.
5. Does the motor need servicing?
It’s not news that many bike components need regular servicing. Many owners do it all themselves – from checking the brakes and lubricating the chain to changing the tires. But what about the motor? There is also a need here. Professional workshops can read out errors via software, check the sensory equipment, grease the gearbox or even replace gears. Incidentally, this servicing is usually even mandatory for leased bikes.