Planetary gears have been around for over 200 years – the first one was used in a steam engine at the beginning of the 19th century. The technology is still indispensable in cars, for example. What distinguishes the whole thing in detail and what are the differences in design?
1. How does the basic principle work?
It is rare for a complex technology to have such a beautiful and appropriate name, because the planetary gear is similar to the structure of our solar system: several planetary gears (connected by a carrier plate) surround a central sun gear. In addition, there is a ring gear which, to a certain extent, surrounds this construction. In this way, loads can be distributed over several wheels and high torques can be transmitted despite the compact design. This is the basic principle, as there are actually a large number of movement and design variants.
Experts usually differentiate between so-called two-shaft and three-shaft operation. In the first case, one of the three shafts is stationary, while the other two are responsible for the input and output. If the planetary gear carrier (including the planetary gears) is not moving, for example, the movement of the inner (smaller) sun is transferred to the movement of the outer (larger) ring gear – a translation into slow speed. Conversely, the speed increases.
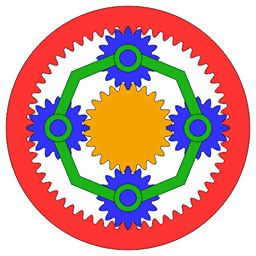
With the sun wheel and the planetary gears, two axes are in motion here.
Source: https://commons.wikimedia.org/wiki/File:Epicyclic_Gearing_Stationary_Ring.gif | Jahobr, CC0, via Wikimedia Commons
In three-shaft operation, all shafts move as a result. For example, two shafts provide the drive and one provides the output. Experts refer to this as a “summation gearbox” because forces from different shafts are combined, so to speak. In the opposite case, a “transfer case” is created.
2. What does the solution in the car look like?
In many automatic car transmissions, several planetary gearboxes are arranged in series, whereby clutches can be used to influence which shaft is rigid and which shafts act as input and output. All desired gears of the car can be “generated” on this basis by shifting gears. The so-called Ravigneaux set is also frequently used, which has another sun gear as the fourth shaft and an additional set of planetary gears. More gears can be elicited from this basic design – which in turn means that fewer sets are required per automatic transmission.

Exemplary animation of a planetary gear.
Source: https://commons.wikimedia.org/wiki/File:Planetary_Gear_Animation.gif | Laser light, CC0, via Wikimedia Commons
3. Who invented it?
William Murdoch is generally regarded as the father of the (simple) planetary gear. Around 1800, as an employee of James Watt, he worked on converting the movement of a steam engine into a controlled movement. This resulted in the first planetary gearbox, which incidentally drove a forging hammer.
Walter Gordon Wilson – one of the directors of the British car brand Wilson-Pilcher – also played an important role in the history of this technology. In 1928, he was involved in the invention of the Wilson gearbox, which had three separate planetary gears and was therefore a forerunner of the design often used today. It was used from 1932 to 1952 – including in two Bugatti models.
4. Are there advantages and disadvantages?
Overall, planetary gearboxes have a very compact design and the construction utilizes the respective torque very effectively. Moreover, the various gears can be controlled without interrupting the gear run or the power flow. A general disadvantage can be seen in production: the design is quite complex, which results in higher costs. The same applies to any repairs, as several gears usually have to be replaced.
5. What does all this mean for production?
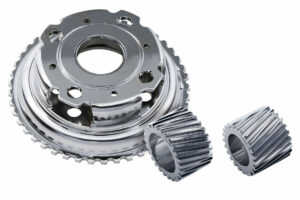
The components of the planetary gearbox (Planetary carrier, sun gear, planetary gear) can be machined with EMAG machines.
The technology is used in a large number of modern automatic transmissions, which is ultimately synonymous with large quantities of the required gears – low unit production costs and high gear quality are always a prerequisite. Take the planetary gears, for example: To ensure effective processes, their machining is carried out in a line solution with two VL 1 Twin machines from EMAG. The overall process takes place with a cycle time of around 20 seconds for two components. The average chip-to-chip time is just under 5 seconds.