The gear skiving process, also known as power skiving, is becoming increasingly popular with many users in the manufacture of gear components. This is no coincidence: compared to the shaping process, it is significantly faster and also offers more flexibility than hobbing and broaching. However, for a long time it was considered relatively complex. In this context, the VSC 400 PS represents a turning point – the application of power skiving is significantly simplified, as only minimal data is required from the operator, eliminating the need for extensive expertise in gear cutting. To take a closer look at the technology behind the VSC 400 PS and its impact on the industry, we interviewed Daniel Nille, Head of Technology Development for EMAG Power Skiving.
Mr. Nille, the VSC 400 PS seems to set a new standard in gear production. Can you explain what makes this machine so special?
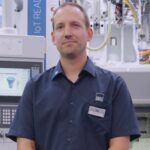
Daniel Nille, Head of technology development EMAG Power Skiving
Of course. The VSC 400 PS is a prime example of how innovations can decisively advance even such a mature process as gear manufacturing. By integrating power skiving and turning technologies in one machine, we offer a solution that significantly increases both the flexibility and efficiency of production. By using up to four skiving tools and six turning tools, our customers can produce even complex tooth profiles in a single setup, which increases productivity enormously.
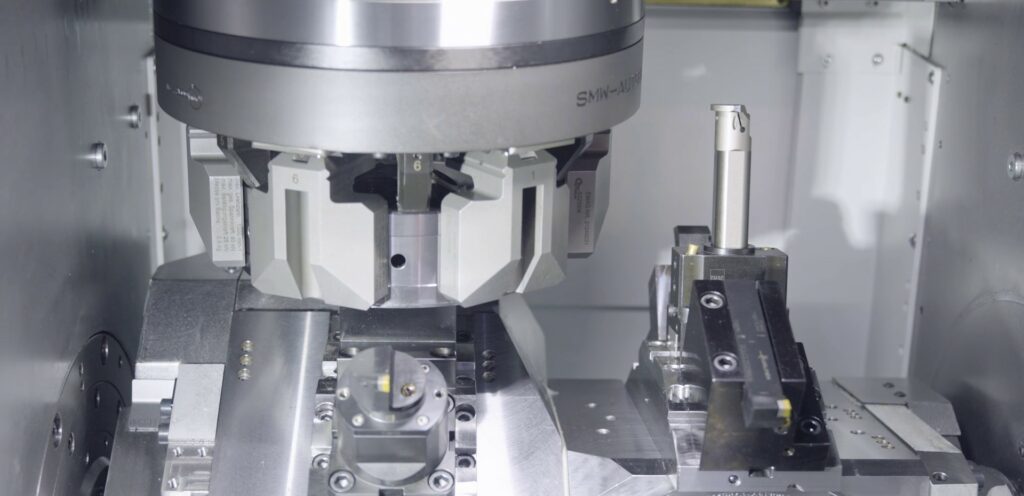
VSC 400 PS with four different power skiving tools on two spindles. It can also accommodate up to six turning tools.
Power skiving has long been considered a complex process. How did EMAG overcome this hurdle with the VSC 400 PS?
We have significantly simplified the operation of the machine. Power skiving used to require a lot of know-how and experience. With the VSC 400 PS, the operator only has to make a few entries, such as the gear data of the component and the tool data. The EMAG user interface provides interactive support and automatically calculates the entire machining program. This not only makes the process simpler, but also significantly faster and less error-prone.
What specific advantages does the combination of power skiving and turning offer?
This combination enables unparalleled flexibility and efficiency in production. Various machining processes from rough-machining, finish-machining and deburring to complex gear cutting operations can be carried out in a single setup and on a single machine. This not only saves time, but also investment and tool costs. In addition, the unchanged setup ensures perfect concentricity between the tooth profiles and the bearing seats, for example. Thanks to the two integrated tool spindles, several tooth profiles can also be produced in a position-oriented manner without any problems.
What component range does the machine cover and in which industries is it used?
The areas of application for the VSC 400 PS extend across various key industries in which internal and external gears play a central role. For example in the automotive industry, gear skiving technology is used more and more due to the increased demands placed on the noise development of gearboxes. Here, precision is crucial in the production of ring gears for planetary gearboxes, but also for other tooth profiles. In the aviation industry, the demands on the quality of components are particularly high. Gearboxes and various aircraft parts have to withstand extreme loads. With its precision gear machining, the VSC 400 PS helps to ensure that these components meet the high safety and performance standards. In the machine and hydraulics industry, the machine is used to produce gears for pumps and compressors. As you can see, the machine has a very wide range of applications and we are constantly finding new uses together with our customers.
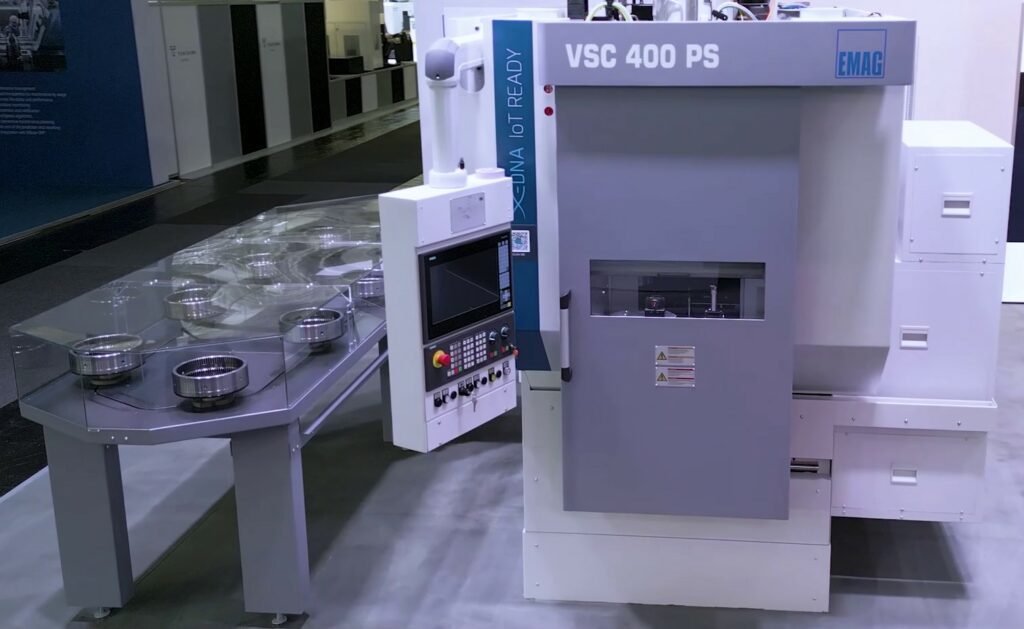
The VSC 400 PS is designed for components with a maximum diameter of 340 mm and a maximum height of 420 mm, making it suitable for a wide range of applications.
Where do you see the future of gear manufacturing? What’s next for the VSC 400 PS?
In my opinion, the future of gear manufacturing lies in the integration and automation of processes. We haven’t even talked about automation yet. Thanks to its pick-up automation, the VSC 400 PS is an automated gear cutting machine by design. This makes it very easy to integrate into production lines or existing systems. Completely new gear cutting lines can also be set up with this machine. EMAG offers a very wide range of turning, gear cutting and grinding machines that can be linked-up with each other via TrackMotion, shuttle automation, gantry loaders or even belt automation. This is another strength of our concept: our solutions can always be individually adapted to the requirements of our customers.