For the past several years, EMAG has offered a turning machine for high-productivity turned parts production, the VL 3 DUO. We spoke to Björn Svatek, Director Global Sales, about the advantages and special features of this machine concept.
Mr. Svatek, what are the most important features of the VL 3 DUO?
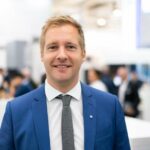
Björn Svatek, Director Global Sales at EMAG
With a component range of ⌀ 150 x 110 mm in height, the VL 3 DUO impresses with its compact design, which enables high productivity in the smallest footprint. A key element is the twin-spindle design, which enables both simultaneous machining and OP 10 / OP 20 processes. Thanks to the two 12-station turrets and the powerful spindles, fast and precision machining of workpieces is possible. The vertical design and good accessibility of the work area also minimize set-up times and thus improve the efficiency of the entire production process. Also worth mentioning is the high rigidity of the machine base made of mineralite, which is manufactured in the company’s own foundry.
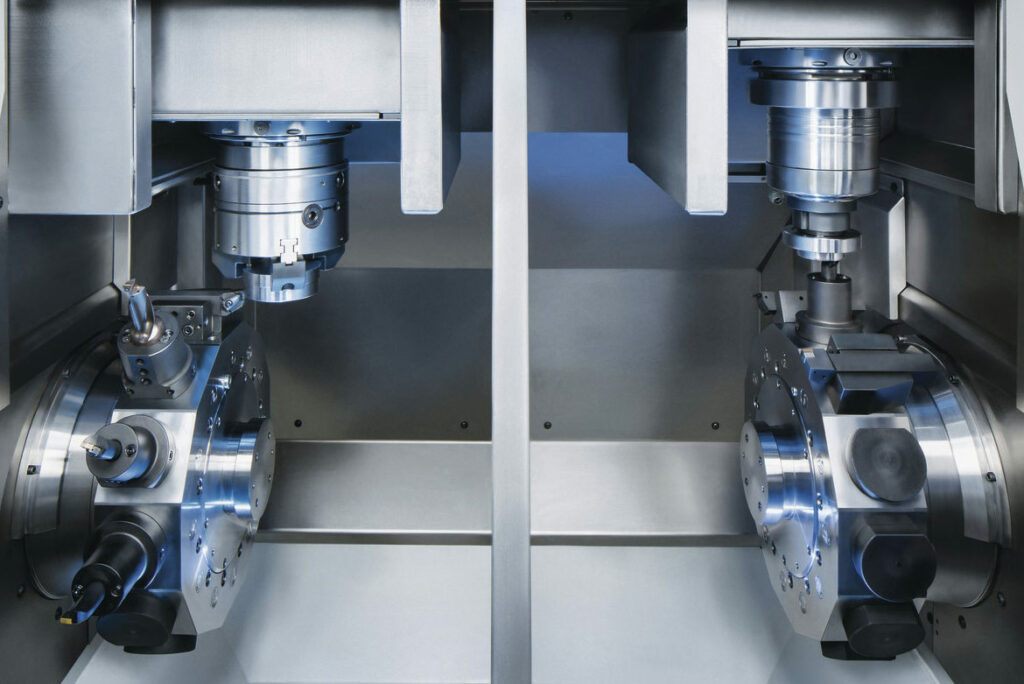
The heart of the machine: The unique double spindle concept of the VL 3 DUO enables simultaneous machining processes for maximum efficiency.
What makes the material Mineralit® so special and why is it so important for the VL 3 DUO?
The mineralite material used in the VL 3 offers several advantages that make it special and play an important role in the performance and efficiency of the machine.
One of the outstanding advantages of mineralite is its vibration damping effect, which is up to ten times better than that of conventional cast iron. This contributes significantly to the reduction of vibrations, resulting in longer tool life. Vibration is a major factor in tool wear; so the improved damping helps to reduce tool costs and maintain machining precision over a longer period of time.
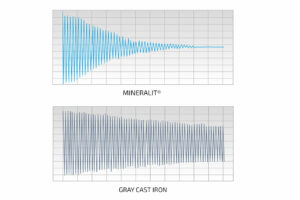
The machine base of the VL 3 DUO made of mineralite dampens up to ten times better than conventional cast iron, reduces vibrations and thus increases the service life of the tools and the precision of machining.
Mineralite is also characterized by a lower thermal sensitivity. This property ensures greater dimensional accuracy and stability of the machine under different operating conditions, which crucial in precision manufacturing.
Another important aspect of Mineralit is its resource efficiency. Compared to cast iron, the machine base body made of mineralite requires 43% less fossil raw materials during production and no corrosion protection is required. The production of mineralite is also more energy-efficient, as the casting process requires around 64% less energy than a comparable machine body made of cast iron.
The performance of a lathe is the decisive factor in production – what values are achieved by the VL 3 DUO?
The powerful, water-cooled motor spindles are key features of the VL 3 DUO. With an output of 32 kW and a torque of 255 Nm, demanding machining processes is possible, which qualifies the machine for both precision and heavy-duty machining. Compared to other machines, the VL 3 DUO thus offers superior performance that is suitable for both batch production and part families.
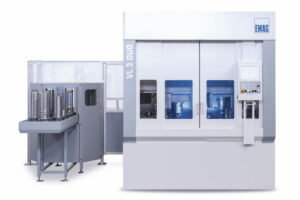
Double-spindle vertical pick-up turning machine VL 3 DUO with workpiece storage.
Can you give us some more information about the TrackMotion automation system? What are the advantages of the system and why does it fit so well with the VL 3 DUO?
The TrackMotion automation system is a central element of the VL 3 DUO and plays a key role in increasing the efficiency and flexibility of the production processes. This system was specially developed for the automated transport of workpieces between the processing stations and the workpiece storage, allowing the machine to produce largely autonomously.
The TrackMotion system is characterized by a simple but effective design. It essentially consists of two components: the “Track” rail system and the “TransLift” lifting turner that can be moved on it. The TransLift is a key element that gives the system its flexibility. It not only transports the workpieces, but can also turn them. It is also equipped with a Z-axis. This functionality enables the use of stackers (parts storage) for the infeed and outfeed of components or the integration of exhibition and marking stations along the rail with different heights.
Another advantage of the TrackMotion system is its space-saving arrangement. The rail is mounted directly behind the work area of the machines, with the energy container of the modular machines being offset from the rest of the machine body. This “tunnel” behind the machines enables parts to be transported quickly on the rail. The close integration of automation and machine enables the realization of manufacturing solutions with a wide range of EMAG technologies such as turning, hobbing, and deburring in the smallest footprint, particularly advantageous for production environments with limited space.
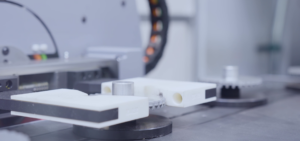
The TrackMotion system is characterized by fast and precision parts handling in production.
Finally, I would be interested to know which sectors and specific applications suit the VL 3 DUO?
The VL 3 DUO is ideal for industries that require high precision and efficiency in mass production, such as the automotive and supplier industry. It is particularly suitable for the production of transmission parts, flanges and components for the electric drive train. However, due to its flexibility and high performance, the VL 3 DUO is also interesting to smaller contract manufacturers.