The brake disc is one of the most important safety-relevant components in passenger and commercial vehicles. The production of brake discs is, therefore, a demanding field of application that requires the highest precision. At the same time, cost pressures are very high and changing production batches must pass through the production lines with high productivity and short set-up times. As a specialist in the machining of brake discs, EMAG has already implemented numerous customized turnkey solutions in close cooperation with customers operating worldwide. In the following interview with Dominic Grimminger, expert for brake disc production systems at EMAG, we learn more about the challenges and solutions in this field of application.
Mr. Grimminger, how has technological development in automotive engineering affected the brake disc?
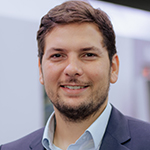
Dominic Grimminger, specialist at EMAG for the machining of brake discs
The rapid pace of technological development in automotive engineering does not stop at brake discs. For example, the quality of cast blanks has improved significantly in recent years. In addition to the classic pure cast iron brake discs, combinations of a cast iron base carrier material and hard-coated friction surfaces are increasingly being used. Alternatively, composite brake discs with carbon friction rings are also used in the premium segment. At the same time, the machining process is changing: users are demanding highly flexible production lines that can be converted to new brake disc types without long downtimes. In addition, both OEMs and their TIER 1 suppliers are seeing a sharp increase in the number of brake discs produced due to platform strategies. The focus here is on unit production costs in high-volume production.
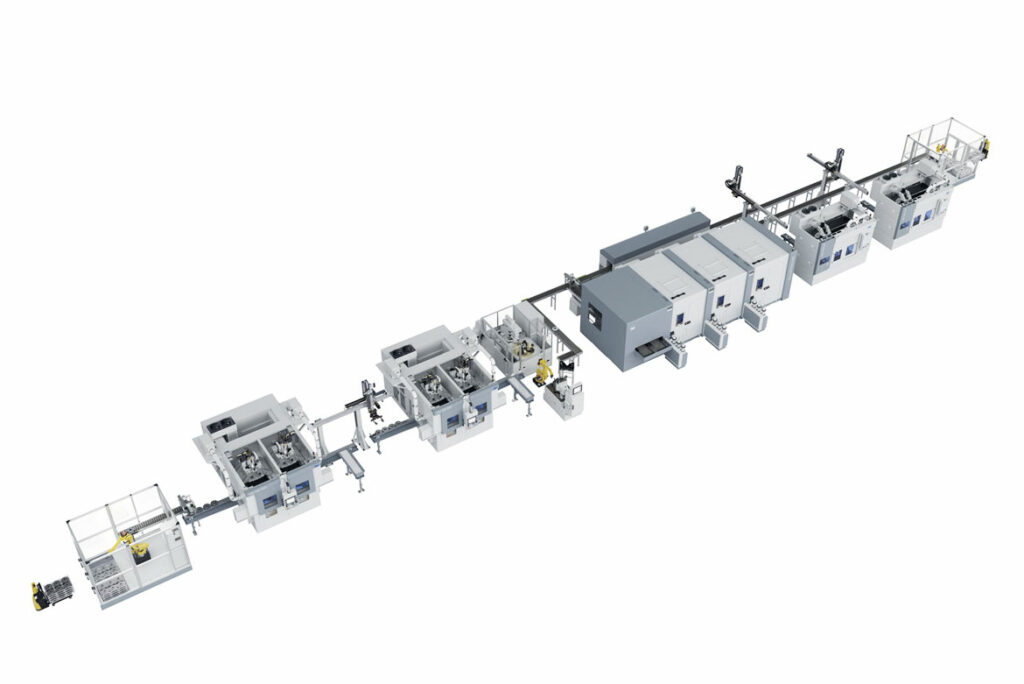
EMAG manufacturing systems for the production of brake discs offer the highest precision, efficiency and quality from vertical machining to coating and grinding of coated brake discs.
What role do EMAG’s vertical pick-up turning machines play in brake disc machining?
Our vertical pick-up turning machines are at the heart of brake disc machining. They ensure speed, precision and process reliability. In addition, the modular machines can be precisely configured for any requirement and very easily integrated into a production line. With the pick-up turning machines of the VSC series, EMAG offers manufacturing solutions that combine quality, productivity and process reliability in this field of application. Short cycle times are achieved by fast loading using a pick-up work spindle in conjunction with high linear feeds and the shortest possible turret swivel times. The machines also have a particularly vibration-damping machine base made of Mineralitâ. Powerful turrets with driven tools enable drilling and milling operations in addition to turning.
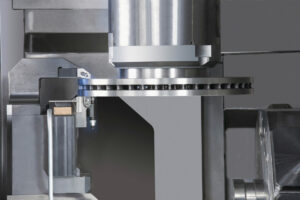
Pick-up vertical turning machines from EMAG ensure speed, precision and process reliability in the machining of brake discs.
Can you tell us more about the machines for machining brake discs?
The VSC 400 DUO vertical machining center, for example, is an ideal production solution here: both simultaneous machining and different operations (OP 10/OP 20) can be carried out irrespective of each other. This allows the machine to be adapted very flexibly to changing batches. All necessary operations such as turning, drilling or milling can be carried out in its work area. This series is, therefore, ideally suited to the machining of brake discs.
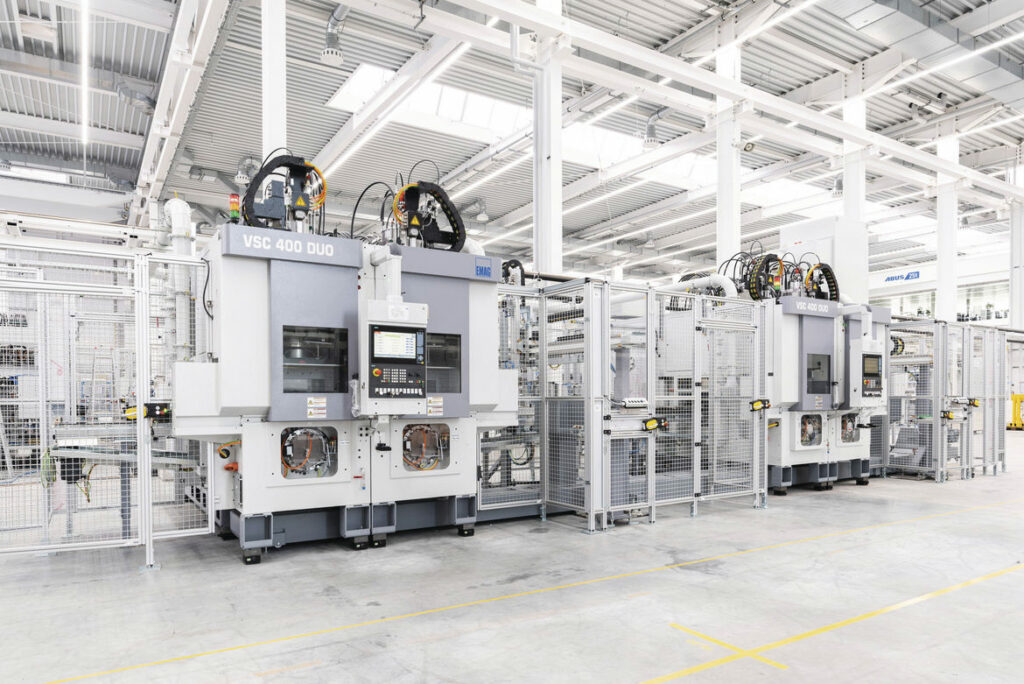
EMAG’s modular machines can be configured precisely for any requirement and easily integrated into a production line.
What about the coating and grinding of brake discs?
EMAG offers scalable mechanical engineering with enormous experience in laser metal deposition from small to large series. We also have both tool technologies relevant for this application in our portfolio: laser metal deposition and grinding. The EMAG solution for laser cladding in large series production is usually carried out in two setups. The workpiece is in an inclined position during the process. The inclined position leads to various efficiency advantages in the “laser – powder” interaction. The heat can also be dissipated better. Additional cooling technology ensures that the thermal load remains manageable even with large quantities.
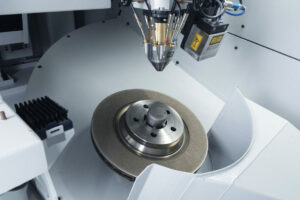
Laser deposition welding of brake discs offers numerous efficiency benefits and perfect thermal control.
The EMAG solution for double-sided face-grinding of the hard coating of brake discs benefits from high rigidity and an intelligent cover concept for the grinding wheels. The two grinding spindles are arranged in parallel and the brake disc is machined in cross-grinding mode. The grinding wheels sharpen themselves thanks to the selected material pairing. Mineral oil-free water is used for the cooling system, from which the very small grinding particles can be easily filtered out.
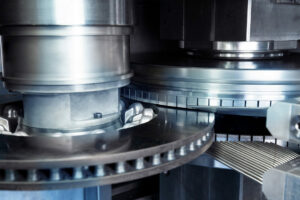
The double-sided face-grinding of coated brake wheels from EMAG benefits from high rigidity and an intelligent cover concept for the grinding wheels.
What are the advantages of EMAG solutions?
The “One Face to the Customer” principle applies. An experienced contact person at EMAG discusses the requirements for the entire manufacturing solution with the customer – including, for example, machines that do not come from EMAG. We take care of each individual component of the manufacturing solution and defines its specifications. This saves the customer a considerable amount of planning work in the quotation and order phase.
What IoT solutions does EMAG offer?
EMAG has developed its own IoT solution (“EDNA”), which can be easily integrated into the machines. Users benefit from this in many ways – including maintenance, for example. With the “EMAG Health Check” software, the health status of axes and spindles can be determined at an early stage and without great effort, necessary maintenance work can be optimally planned for the operating process and the spare part can be ordered just-in-time accordingly.