The EMAG ELC 6 laser welding machine plays a key role in the production of drive components for electric motors. In our interview with Konrad Eibl, you will gain a deeper insight into how the ELC 6 works, the technical aspects and the wide range of possible applications. You will learn how this innovative machine contributes to increasing efficiency in production and what role it will play in the future of manufacturing technology. Particular attention will be paid to the production of rotor shafts, a critical element in the rapidly growing electromobility industry, where precision and process reliability are highly important.
Mr. Eibl, what is special about the EMAG ELC 6 laser welding system?
The ELC 6 is a top solution for laser welding powertrain components. Its special feature is the combination of high speed, precision and flexibility. It efficiently integrates various processes – from pressing together to preheating and welding.
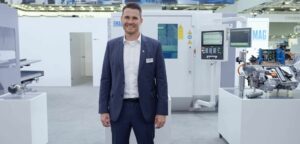
Konrad Eibl, Head of Offer Engineering, Business Unit LaserTec at EMAG LaserTec GmbH
Can you elaborate on the specific functions that make the ELC 6 so efficient for the production of rotor shafts?
Naturally. When it comes to rotor shafts, the central components of electric motors, precision is key. A production system with an ELC 6 makes this possible with a range of functions:
- Laser cleaning: before welding, the components are cleaned with our LC 4 laser cleaning machine. This ensures that the weld seams are clean and free from contamination.
- Inductive preheating: before joining the components, induction technology ensures an optimum processing temperature, which minimizes the risk of defects in the weld seam.
- Precise positioning: before welding, we check the position of the weld seam and adjust the component position with precision. This is done by precision scanning before welding and then adjusting the welding optics with an NC axis.
- Rotary welding: during welding itself, the workpiece rotates while the laser optics remain stationary. This process enables focused and precision energy input along the circumferential seam.

ELC 6 in use: laser welding of rotor shafts
How does the ELC 6 contribute to improving overall productivity?
The ELC 6 can be used in a comprehensive production system. Clever integration significantly increases overall efficiency. For example, the rotary table of the ELC 6 enables loading and unloading during welding, which drastically reduces non-productive time. In addition, the processes in the machine are perfectly synchronized, enabling continuous and trouble-free production.
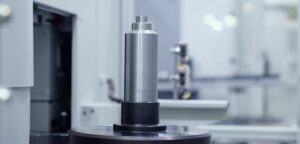
The rotary table of the ELC 6 enables simultaneous loading and unloading for the highest productivity level.
How does the ELC 6 fit into EMAG’s technology portfolio?
EMAG offers a wide range of solutions for the automotive and supplier industry. The ELC 6 is a key element of this portfolio, particularly in the field of electromobility. With our expertise in a wide range of manufacturing technologies – from turning to gear cutting and grinding – and the integration of these technologies into a complete solution, we can offer our customers unique, customized production systems. It is important to emphasize that the production of rotor shafts for electric motors is very demanding. With the ELC 6, we can meet these challenges with precision and efficiency. Thanks to the optimized workpiece fixture and the resulting minimal distortion, the ELC 6 offers outstanding weld seam quality.
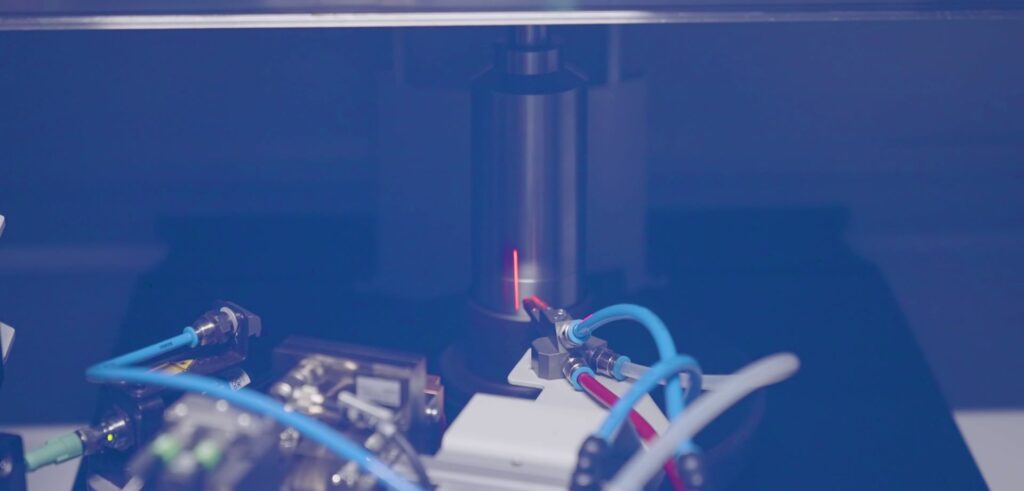
Precision control: The ELC 6 carefully checks the seam position before laser welding
And finally: What future prospects do you see for the ELC 6 and similar technologies at EMAG?
We are at the beginning of an exciting development in production technology, particularly in the field of electromobility. The ELC 6 is an example of how advanced technologies can decisively advance production processes. We have successfully completed demanding rotor shaft projects using the ELC 6 and are constantly developing technologies to meet the growing demands of the industry while offering our customers the best solution for their production requirements.
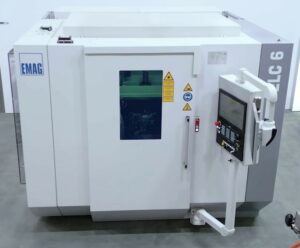
ELC 6: Innovation in the precision production of rotor shafts
The future for us lies in solutions, e.g. for variants of the rotor shaft and other drive components of electric motors.