Because its dynamics and motor speeds influence cycle and non-productive times, the spindle is essential for the productivity of a machine tool. However, the central assembly is also subject to wear – after a certain period of use, it must be replaced or overhauled. Learn more from a conversation with Markus Heidel, Head of Retrofit at EMAG, discussing the processes involved in retrofitting spindles.
What distinguishes EMAG’s spindle service in the subject area of “Retrofit?”
First, it should be emphasized at this point that EMAG has a special market position in this area. After all, we were the first company to develop a machine with a vertical work spindle that can move in the main axes and pick up components outside the work area. The spindles are, therefore, at the center of our attention and are constantly being further developed. That is why, for example, they have a particularly rigid and robust design. In this context, our “spindle and component assembly” team has a great deal of know-how and experience. Of course, this always flows into the retrofit of spindles.
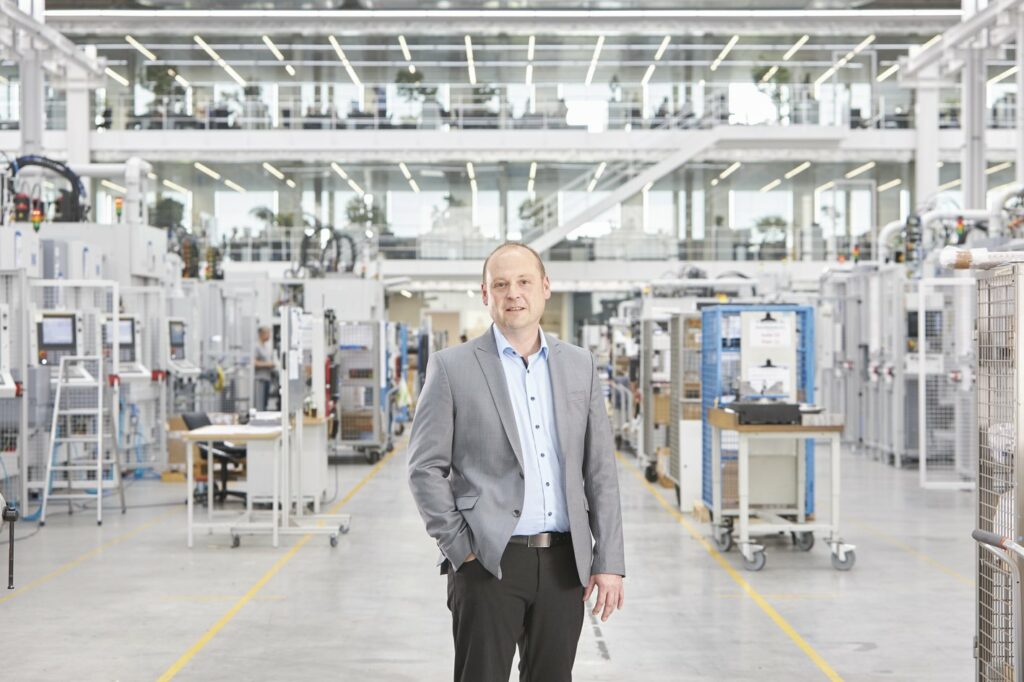
Markus Heidel, Head of Retrofit at EMAG, discussing the processes involved in retrofitting spindles
When and why does a spindle need to be replaced?
The main spindle is inevitably subject to wear; after all, enormous physical forces act on the central component. However, most customers only come to us when there is more concrete damage – for example, the bearings are jammed. As a result, the assembly must be replaced quickly to avoid long downtimes. In this case, new spindles or spindles reconditioned by us can be used – the second case is an inexpensive alternative. We guarantee that every retrofit spindle has the usual performance and stability.
What does the process around the spindle look like when retrofitting a complete machine?
When a machine is completely overhauled and completely rebuilt, this naturally also affects the spindle. We divide the process up at our company. One team overhauls central elements of the machine such as linear guides, feed drives, cabling and seals, housing and more. Another team deals with the spindle. Like the machine, it is completely disassembled and cleaned, wear elements are replaced, re-measured and finally tested on the test stand. The result is high quality that can compete with new spindles.
Can you also react quickly in the event of a collision, for example?
Yes, of course. After a collision between the main spindle and the tool – due to a programming error, for example – damage occurs to the spindle bearing, which under certain circumstances can lead to a machine standstill. In the first step, it is then possible to determine the extent of the damage by taking measurements. If it is very large, replacement is unavoidable. Our customers then benefit from the fact that we keep many individual parts as well as standard assemblies such as main spindles and turret units in our central spare parts warehouse. As a rule, we deliver only one day after the order is placed.
Who takes care of the replacement on site at the customer in such a case?
We are completely oriented to the customer’s ideas here. If the replacement of the spindle cannot be carried out by the user’s employees, our service experts are quickly on site and take over the entire replacement process. By the way, the same also applies to the retrofit of a complete machine. For example, we were currently on site at a customer in Mexico and carried out almost all the overhaul processes there. After all, sending the machines to Germany would be far too costly. In such cases, only the spindle retrofit is carried out at our plant in Eislingen.