Automating machine tools using robots creates a lot of benefits for production, making the entire process faster, more cost-efficient and more reliable. EMAG’s pick-up technology is particularly suited for automation because the machines’ internal automation systems mean they can be loaded and unloaded very effectively using robots and can easily be interlinked. A conversation with Stefan Erhardt, head of the Automation and Robotics Business Unit at EMAG, discusses the possibilities with combining robots and EMAG machines in production.
Mr. Erhardt, how important are robots for establishing new EMAG production solutions?
They are becoming increasingly important – and that’s no coincidence since they enable us to offer the customer integrated solutions from a single source and result in a smooth parts flow within production. The components, therefore, get from A to B with extremely little effort. Either an operator is no longer required for this or there is very little work involved for the operators. The man hours on the machine decrease, which, of course, ultimately leads to lower costs.
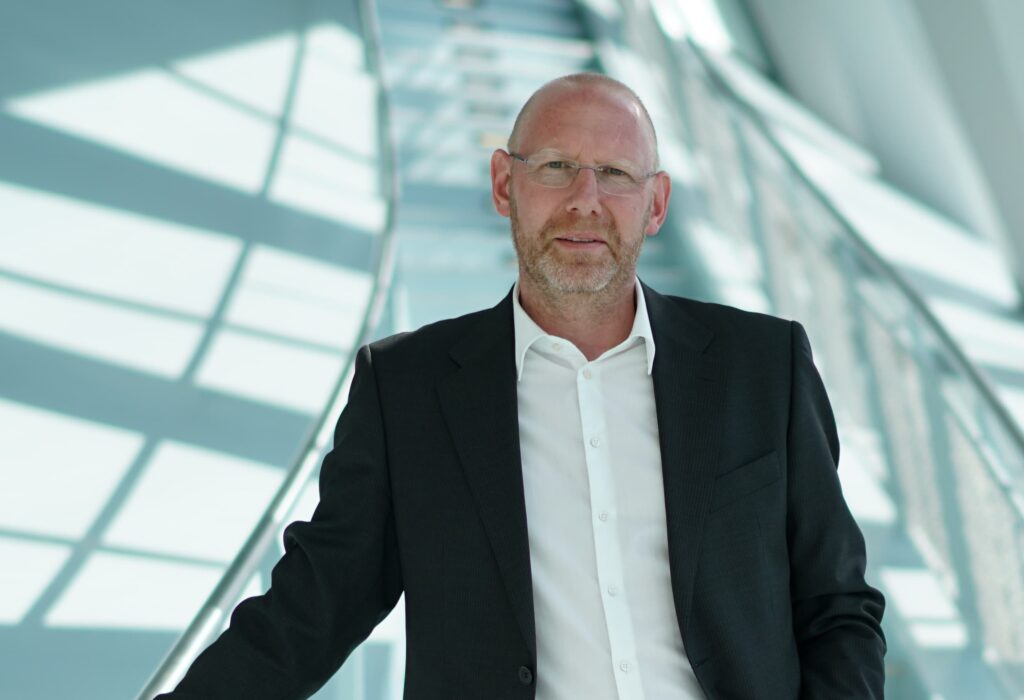
Stefan Erhardt, head of the Automation and Robotics Business Unit at EMAG
What role does EMAG technology play in this context?
It provides the ideal basis. For example, we have lots of solutions that execute various operations in just one machine, with pick-up spindles often used for loading the machining area. Combining this technology with a robot cell closes the circle: The entire machining of complex parts – from loading the system with raw parts to removing the finished parts – takes place in an automated process, quickly and smoothly.
What robot solutions are used with EMAG machines?
This varies a lot and depends on the requirements of the workpiece and of the production process. Crucial questions include the batch sizes that will be manufactured in a specific period and how autonomously the solution should work. No matter what, we have great flexibility and many ways of adapting to the existing production environment or the space conditions. In concrete terms, this means that the parts can, for example, be fed in using belts, palletizers, drawer systems or by means of bin picking – these systems allow the robot to “help itself.”
What criteria determine the choice of the correct infeed and outfeed around the robot cell?
Let’s take the example of “belt or hinged conveyors.” They are an ideal variant if the parts flow is to take place smoothly from an upstream production solution to the EMAG machine. The robot can simply pick up the parts from the belt and place them back down again later, with the belts arranged in different ways – depending on the space situation or the desired parts flow. Here we can adapt to the conditions at the customer. If the customer is already using a specific belt system, then we also use this to feed parts to our robot. A highly flexible alternative to this method is bin-picking systems. Here the workpieces are in chaotic positions. With the aid of a 3D sensor system, the robot arm not only takes out the parts, but also correctly identifies and aligns them and feeds them to the next machining step. The system is versatile and can be configured for lots of use cases.
Are there other solutions – for instance if space is very limited?
Of course. At many customers, we find a compact arrangement of oriented workpieces in baskets that are stacked on top of each other on roller bases to form a stacking unit – in other words, a relatively large quantity in a small area. In this way, the roller bases with the baskets are brought to the relevant production machine. The robot then takes the workpieces out of the baskets and repositions the baskets.
Another level of automation is then making the material available in the baskets with the SCS 4 from EMAG. In the SCS 4, the baskets with the workpieces are repositioned by the internal axis system and made available to the robot. The clear advantage of the SCS 4 is that the autonomous parts storage unit is very large and production is not interrupted. The robot ensures a continuous material flow with the baskets provided by the SCS 4.
However, the cycle time of the EMAG machine and the desired man hours on the machine must always be in relation to each other. If the cycle time of the machine is just a few seconds, the right automation system with the right parts storage unit must be used to ultimately achieve production at attractive unit costs. But these are precisely the analyses that we perform for every robot solution, and then we advise the customer accordingly.
Are robots only used for loading and unloading the EMAG machines?
No, we can integrate many peripheral systems into the robot cell. The spectrum is very broad. We offer statistical process control (SPC) including measuring station, optical control systems with cameras, gripper stations for machining a large spectrum of workpieces using robots, small washing and cleaning stations, as well as deburring systems or laser and engraving stations. The robot also loads and unloads the relevant solution. The result is therefore a continuous parts flow across various technologies.
How exactly are the systems planned and configured?
For long-term success, we rely on computer-based simulations when planning automation cells. This lets us check essential factors such as cycle time, accessibility of the robot, the material flow for large production lines and much more. Similarly important is the virtual start-up – in other words testing the planning data on a virtual machine. This is how we uncover anything unexpected and correct it in an early phase of development. And the “real” start-up goes much faster later.
Automation Systems from EMAG
Automation cell with basket stacking
In automation cells with basket stacking, the loading and unloading of the system is done using baskets from which the robot grabs the pre-aligned workpieces or deposits them. The empty baskets are placed onto the stack by the robot.
Bin-picking automation cell
With bin-picking systems, the workpieces are in chaotic positions. With the aid of a 3D sensor system, the robot not only takes out the parts, but also correctly identifies and aligns them and feeds them to the next machining step.
Automation cell with drawer system
With the drawer system, the workpieces are provided to the robot on different levels. While the drawers are being filled, the robot in the cell supplies workpieces to the machine.