Machine owners who regularly maintain their machines prevent many unplanned downtimes and thus improve the entire production reliability of their facilities. Nevertheless, many users still let their machines run until severe damage has occurred – without ever performing a comprehensive check beforehand. What is important when it comes to inspection and maintenance, and what opportunities does IoT technology offer in this regard? A conversation with Patrick Theiss, head of the After Sales/Service business unit at EMAG.
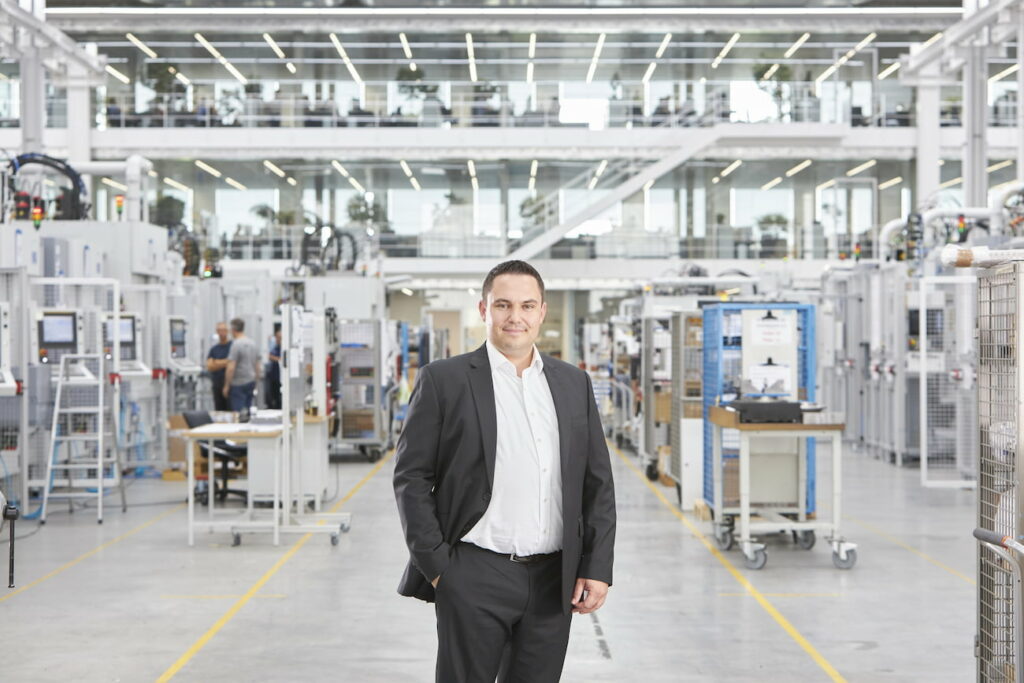
Patrick Theiss, Head of the After Sales/Service business unit at EMAG
Mr Theiss, what significance does inspection and maintenance have in general in mechanical engineering?
A very high significance! Actually, that should be obvious, because modern machine tools are complex pieces of technology with many moving elements and perfectly adapted software solutions. Additionally, strong forces are involved and frequently the machines are used in harsh environments with dust and fumes. Furthermore, maintenance generally results in more efficient production processes with constant production quality. It thus makes a lot of sense to regularly check the machines and replace small parts that are worn. After all, you also get the brakes on your car replaced regularly instead of driving until there is an accident.
Can you give us an example for the effectiveness of inspection and maintenance at the customer?
Let’s look at a customer from the south of Germany, from the field of agricultural machines and vehicles. Here we annually perform an advance inspection with subsequent maintenance – on no less than 18 machines of type VSC/VT. These are used for machining of castings for transmission components and are run in four-shift operation. The machines are therefore subjected to heavy use. Nevertheless, we succeeded in drastically reducing the unplanned downtimes. On average, only two to three are reported per year – for the entire machine fleet! As a result, we were able to reduce the ongoing maintenance costs by 30 percent through targeted servicing.
Why are there still users that never get their machines serviced or checked?
On the one hand, this can be viewed as an indirect compliment for EMAG. Many users simply know from experience that our solutions are very robust and serve their purpose well without noteworthy problems, sometimes for many years. This easily gives rise to the notion that maintenance and inspections are not necessary at all. But on the other hand, this is a false conclusion, of course. We are not able to override the laws of physics – friction heat and vibrations in time lead to minor damage that can usually be quickly eliminated with only little servicing work.
But can’t one simply eliminate such damage when the machine does happen to come to an unplanned standstill?
The problem is that, in these cases, the damage is frequently already much more severe. For example, it might be necessary to replace the entire turret and other high-quality machine components costing several tens of thousands of euros – and this is the exactly the kind of damage that can easily be prevented at an earlier stage by simply replacing very affordable seals or checking the status of certain filling materials. By the way, we conduct our maintenance and inspections at optimal times, of course – for example when the production facility has scheduled downtimes anyway. We are also fast because we understand the susceptibilities of the machines in detail. This minimizes the downtimes. On the other hand, downtimes caused by technical damage can, in the worst case, last several weeks – and it is unplanned. You need to produce but cannot. This additionally drives up the costs.
What significance does maintenance have for the production quality?
If you do not regularly service or inspect your machines, important machine parameters can change or key components can get worn out. This impacts the production quality, of course. The topic is therefore also important for this aspect.
Can you give us an idea of what a maintenance or inspection contract looks like?
Together with the customer, we precisely define what we do, always with cost efficiency in mind. There are many questions to clarify – from the term of the maintenance contract and the scope of the tests to the planned replacement of service parts. The goal is always the same: maximum transparency. Subsequently, the users always profit from a wealth of experience: Our service technicians are experts in “their” technology – from the travel accuracy and repeatability of the NC axes, the swiveling accuracy of the tool carrier, and the smooth movement of the clamping chuck to the geometry of the entire machine.
What role does the respective deployment scenario of the machine play?
It is considered for the maintenance schedule, of course, because different applications mean different forces during machining and the machines have different operating durations per year at the different customers. However, we always know comparable applications, and use these as basis for suggesting targeted maintenance cycles and strategies.
Is it possible to just have a machine checked, with a small scope?
Of course, we offer different inspection packages for this purpose. For example, there is the quick check for a visual and mechanical inspection of the machine. The results provide information on the main components. Within the scope of the slightly more comprehensive fitness check, a predefined checklist is used. Subsequently, repairs and maintenance action can be initiated, if necessary.
How important is the topic of IoT in the context of maintenance and repairs?
The topic is very important – we have more and more customers who use our extensive EDNA system, because its data-based health check helps to reduce costs. The basis of the solution is the EDNA IOT CORE – an industrial PC that is connected to the machine controller and receives and records manufacturing data by means of the EDNA CORTEX software. For the health check, regular vibration measurements are then performed by means of sensors. The measurement program traverses various axes and components in the machine and determines their vibration data. The data is processed in the EDNA cloud or directly at the customer, in the EDNA edge cloud, and is analyzed by means of AI. The AI model has been so well trained that it can determine a trend for the health of the machine.
What is the economic effect of this approach?
In practice, the system results in astounding cost benefits, as current application examples of EMAG clearly show. The majority of unplanned downtimes can be recognized and the waiting periods for spare parts and service technicians are drastically reduced – for example, because spare parts are supplied well in time and the deployment of service technicians is scheduled at an equally early stage. On this basis, a productivity increase of around three percent can be achieved.
Finally, what will the significance of maintenance be in the future, in your opinion?
We are convinced that servicing will gain increasing importance in mechanical engineering in the years to come. Higher requirements on component quality and just-in-time production processes dictate the way ahead. In this context, we are in an optimal position with the services we offer.
Read more here: