According to a survey carried out by the digital association Bitkom, roughly six in ten German companies are already using Industry 4.0 applications. However, just 14% of them are using artificial intelligence (AI) to boost their productivity. But getting started with the whole field of data science is easier than many people think. EMAG’s partner anacision is offering a cost-effective Industry 4.0 workshop and compact data analysis packages to help users fulfill their business potential. We talked to Daniel Poodratchi, Head of Product at anacision, about quickly identifying ineffective processes using AI, data-driven production optimization and successful customer projects.
Industry 4.0 is very attractive for small and medium-sized enterprises too
Mr. Poodratchi, how would you describe the current state of evolution of Industry 4.0 in Germany?
The term has been around for at least ten years. Up to now, it was mostly heard in connection with pilot projects and research. All that is changing now as the decision-makers in companies become aware of the potential of data-driven solutions in production. Data-driven approaches are helping manufacturers to achieve unprecedented leaps in efficiency. This translates to competitive advantages on the cost side. Also, makers of plant and machinery more than ever need to offer modern data interfaces too, since manufacturers need that data for their Industry 4.0 solutions.
Why are many companies still dragging their feet in embracing long-term data analysis and data use?
Up to now, many approaches in the Industry 4.0 environment were not practical enough. In addition, many of these approaches were never going to catch on due to the lack of measurable added value. This led to planning uncertainty and high levels of investment. Now, though, things are different: Costs and benefits can be measured. This makes Industry 4.0 very attractive for small and medium-sized enterprises in particular. What’s more, you can get started in the Industry 4.0 world with relatively little effort. That’s our mission in each new project, and we are underlining it now with a new offering.
What exactly does this offering look like?
It is divided into two services, which customers can take advantage of individually or together. The first part consists of a one-day workshop, where we identify a production site’s Industry 4.0 potential. For the second step—practical implementation—we offer compact data analysis packages for boosting production output in the desired area. Overall, the goal is to identify a production site’s potential and develop it in a way that can be measured in ROI terms. For this, manufacturing experts and data specialists need to come together. And that’s exactly what we offer with the Industry 4.0 workshop.
What does the workshop involve?
To prepare for the workshop, our production experts meet with the customer’s representatives for an initial discussion about the challenges in production. We get information about manufacturing processes, central value propositions such as delivery reliability, unwanted downtimes and output and quantity per shift. In addition, the users can introduce specific ideas or critical topics from production during this process. We analyze the data and use it to prepare the workshop, dividing it into several parts. It kicks off with an introduction to the topic “Industry 4.0/IoT and Artificial Intelligence in Production” by an anacision employee, who provides information about the current capabilities of the technology. Our IoT experts then discuss all the production relevant tasks and problems together with the production managers, shopfloor staff, and maintenance staff. Next, we use the results to come up with action scenarios for harnessing business potential. Then we define two to three recommendations for concrete action based on those scenarios. After the workshop, these are examined further in terms of ROI (return on investment) and are prioritized. At the end, the customer therefore knows exactly what is possible in their production and how to reach the targets.
What services do the subsequent data packages include?
First, we use artificial intelligence to analyze the machine data and process data generated in the desired production area. In this way we identify unwanted drivers of downtimes, production faults and inefficient processes within a shift, and at the same time make the unharnessed potential measurable.
As a result, even the basic-level data analysis package gives customers specific recommendations for how to reduce downtimes and boost their output in practice—essentially, they need to eliminate the drivers of the problems. Additionally, they have exact numbers on how great the potential is and can decide which measures are best to implement. With our two advanced packages, we then start with implementation directly on site and get AI solutions for optimizing production up and running.
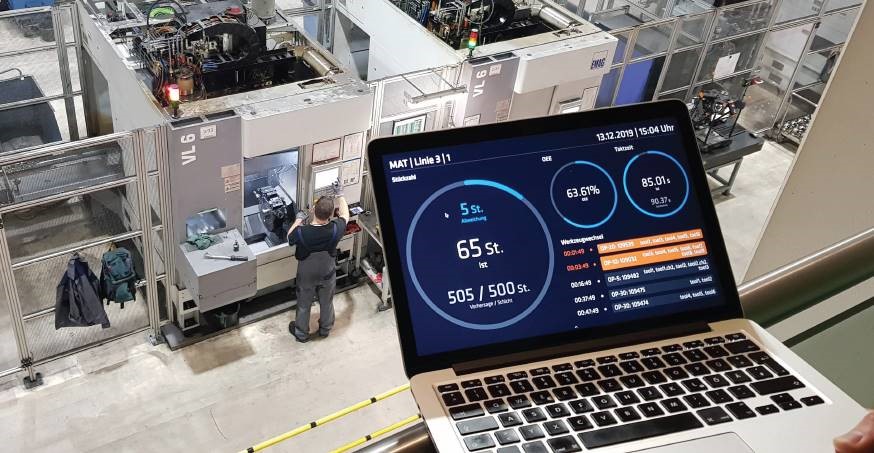
Even the basic-level data analysis package gives customers specific recommendations for how to reduce downtimes and boost their output in practice.
What exactly can be optimized using AI data analysis?
The spectrum is broad. For example, it is possible to provide real-time forecasts about the component quality produced, which cuts down on manual quality assurance processes. It is also possible during production to identify whether shift targets are in jeopardy, what is causing systematic stoppages, and what a machine’s state of health is like. Another thing that is really interesting for many users is the quantum leaps currently occurring in detailed planning using AI and IoT technologies, with intelligent planning responding “adaptively” to manufacturing events. AI analyses identify optimization potential by means of target/actual comparisons, for higher utilization of machinery.
What role does EMAG’s EDNA IoT system play here?
EDNA is EMAG’s Industry 4.0 ecosystem, a network of software and machine components. It records a lot of manufacturing data and prepares them for data analysis. As a result, the system naturally forms the ideal basis for our data analysis. But we can also work based on data from ERP and from operational and machine data logging systems as well as NC data.
To finish, can you give us an example of your work’s success?
An automotive components supplier was having isolated quality problems when cutting threads in mass production. This led to complex quality checks, some of which had to be done manually. Using the control data—in this case regarding high-frequency axis positions of the machine tool—an AI model now detects 100% of faulty parts during production. Manual quality assurance for this component is no longer needed at all.
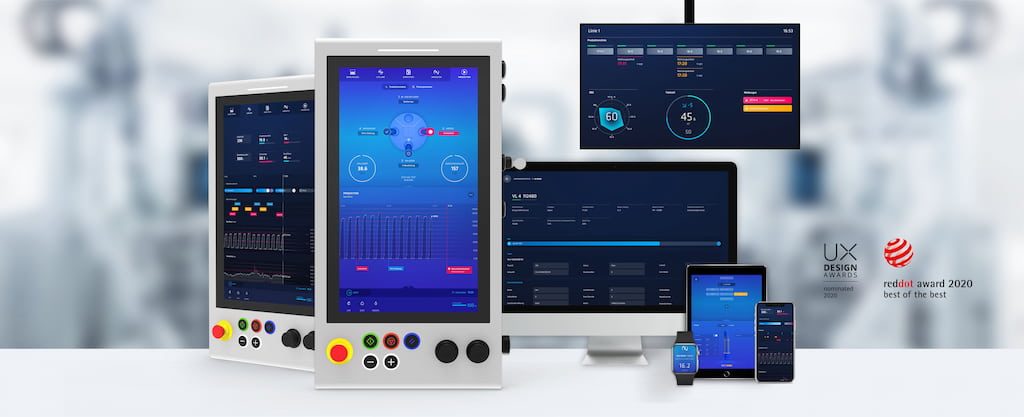
EDNA is EMAG’s Industry 4.0 ecosystem, a network of software and machine components.