In the world of high precision drives, Zoerkler is a name synonymous with innovation, quality and technical excellence. In its almost 120-year history, the company has developed from a modest mechanical engineers’ workshop into a leading supplier of drive systems for the automotive and aviation industries. In this interview, Managing Director Bernhard Wagner provides insights into the fascinating world of precision manufacturing, innovative production technologies and the future visions of Zoerkler Gears GmbH & Co KG.
Let’s start by taking a look back. Can you briefly outline the history and development of your company?
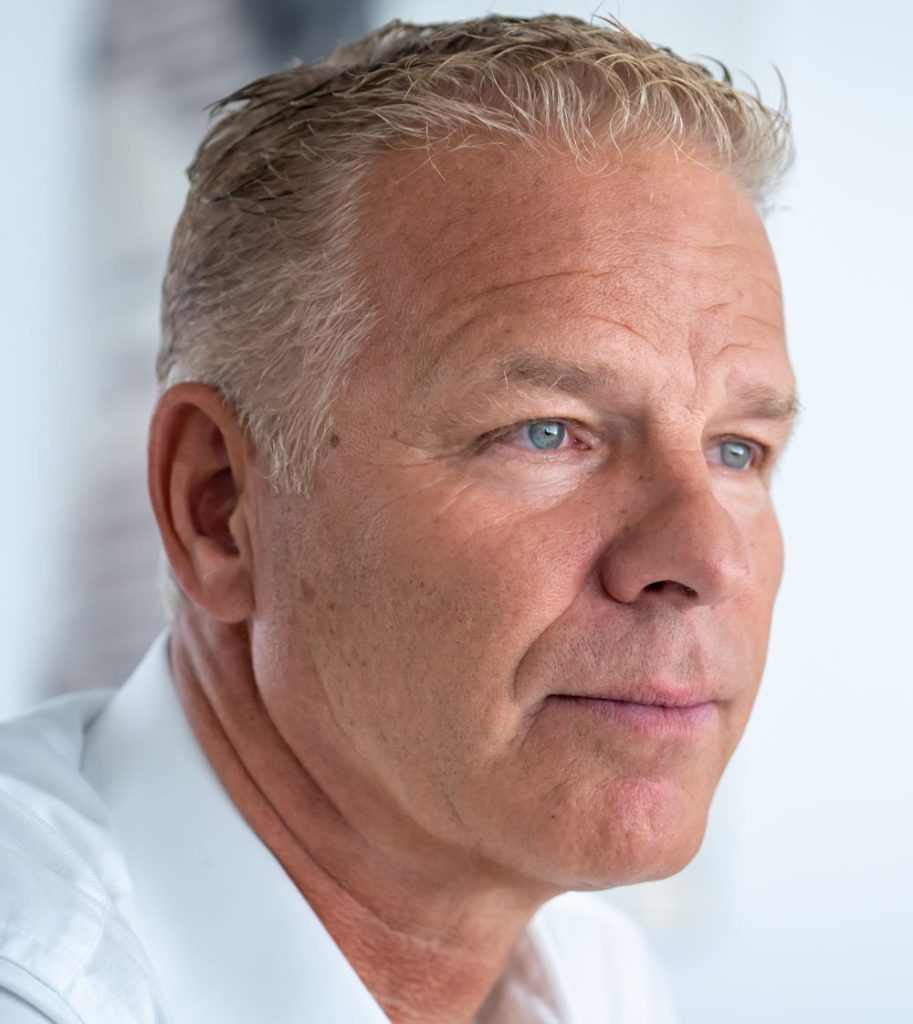
Bernhard Wagner, Managing Director of Zoerkler
With pleasure. Our company can look back on almost 120 years of history. It started out as a modest family business – a small mechanical workshop. My grandfather laid the foundations by manufacturing simple spare parts. Over time, we specialized more and more in gear cutting, especially for construction machinery.
We expanded continuously over the following decades. At our old location in Vienna, we began producing high-quality drive systems and gears on an area of around 1,800 square meters. We made the big leap in 2008 when we moved to Burgenland. Here we have a production area of 8,000 square meters, which enables us to manufacture high-quality drive systems and precision parts at the highest level.
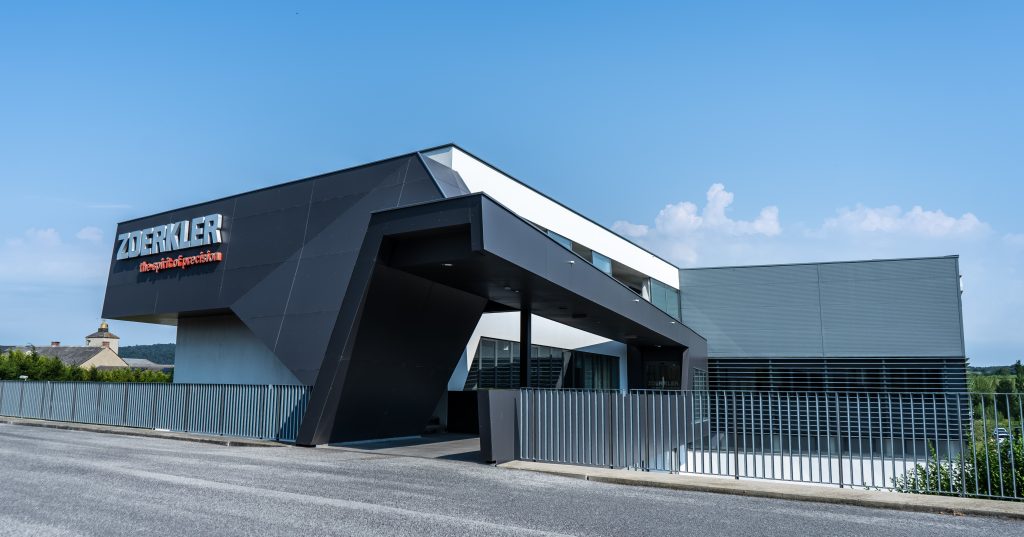
The high quality standards are also reflected in the modern design of the production hall.
An impressive development. How many employees do you currently have at the site?
Our team currently comprises 100 employees. This includes eight trainees, which underlines our commitment to training young specialists. Around 15 of our employees are highly qualified design engineers who work in our development team. The majority of our workforce, namely 77 employees, work in production, where they contribute their knowledge and skills to the production of our precision components.
Can you give us a deeper insight into your core business? You mentioned precision and high-quality gearboxes.
Our core business is the design, manufacture and testing of high performance drive systems. We have specialized in two main sectors: the automotive and aviation industries. Here, the requirements for precision and reliability are particularly high.
Our drive systems can be found in high performance vehicles that belong to the absolute top class of the automotive industry. In aviation, we equip helicopters and airplanes with our systems. The extreme operating conditions demand the highest quality and reliability.
We also serve the railway and agricultural machinery industries, where our drive systems are also used. However, our main focus is clearly on precision drive systems for the most demanding applications in the automotive and aviation industries.
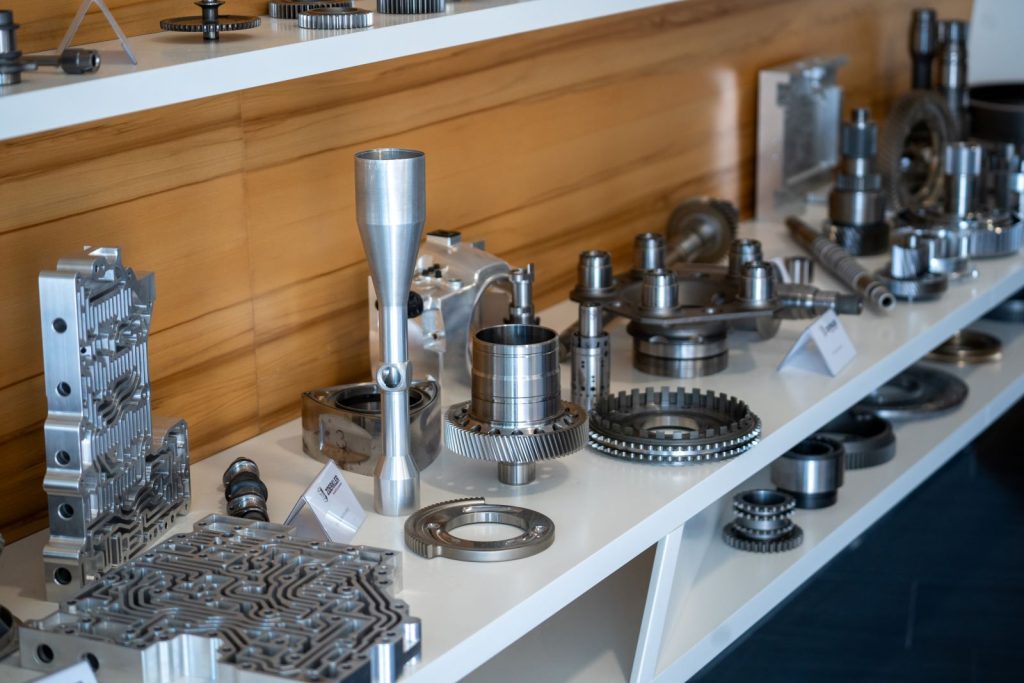
A selection of different precision parts manufactured by Zoerkler. The components vary in size and shape, from small gears to complex transmission parts.
On your website, you mention that you offer drive systems from design and development through to the calculation and production of prototypes or to series production. Can you explain this process in more detail?
Of course. Many of our orders are future-oriented “built-to-spec” projects. This means that we receive detailed requirements and specifications from the customer. On this basis we take over the entire development process. First, we create a comprehensive layout. Our engineers develop, design and manufacture the drive system down to the smallest detail. Once the planning phase is completed, production begins. All components are manufactured in-house and then assembled by our specialists.
A special added value for our customers is our in-house test center. On request, we can carry out extensive tests through to a complete certification of the system. This ensures that every product that leaves our premises meets the highest quality standards and is optimally suited for the respective application.
That sounds like a very comprehensive approach. What is special about a Zoerkler gearbox? What are the strengths of your components?
The special feature of our gearboxes is the combination of the highest quality of the individual components and their perfect interaction in the overall system. We place the greatest emphasis on the precision of each individual component. When these precision parts are then assembled into a system, the result is an overall performance that is unparalleled in terms of reliability and quality. A key advantage of our approach is the complete integration of all process steps – from engineering to testing – under one roof. This allows us to significantly shorten the development time. Even in the engineering phase, we can say with a high degree of certainty that the tolerances specified in the drawing will be adhered to in production.
For our customers, this comprehensive approach means an enormous advantage in terms of transparency and control. They have the opportunity to come to us with their team and follow the entire process on site – from design on the computer through production and assembly to the test stand. This openness and direct involvement of the customer in the design and development process is a unique selling point that our customers greatly appreciate.
That is indeed an impressive approach. What quantities and batches do you typically produce?
Our production is very flexible and customer-oriented. Our orders are typically in batches of between 50 and 100 pieces. This allows us to manufacture each product with the utmost care and precision without compromising on quality. However, we also have some series orders in our portfolio where we produce significantly larger quantities. In these cases, we sometimes deliver 800 to 900 units per week. This range shows that we are able to handle both small series and larger production volumes efficiently.
An important aspect of our production is that we only manufacture customer-specific solutions. We have no stock items; every component is manufactured according to the individual requirements of our customers. We only carry out contract manufacture to a very limited extent, as our orders usually require a high level of specific know-how.
Our customers also particularly appreciate our commitment to prototype development. Even if the design and development does not come from us, we support the OEMs’ development departments with our extensive manufacturing expertise in the production of prototypes. This ability to react flexibly to different customer requirements while always delivering the highest quality is one of the reasons why our customers value us as a valuable partner.
Can you give us an insight into the technologies and process steps that you use here in gearbox production?
With pleasure. We are proud of the fact that we can carry out almost all process steps in gearbox production in-house. Our production chain begins with the purchase of raw materials and includes all essential processing steps. We use state-of-the-art turning and milling machines for basic machining. Our high-precision grinding processes, both cylindrical grinding and coordinate grinding, are then used to achieve the tight tolerances required.
A special focus is of course on gear cutting. We have a wide range of options here. We can perform helical broaching and grinding on internal gears, which is particularly advantageous for compact gearboxes. Our repertoire also includes the manufacture of sprockets and ring gears, even for the smallest dimensions.
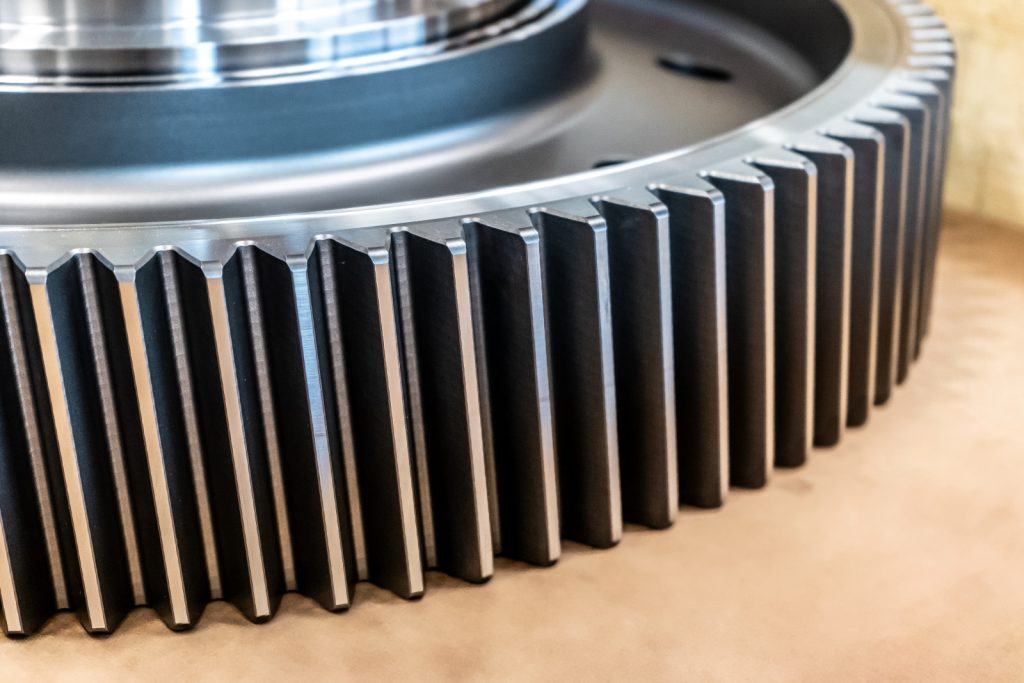
Close-up of a high-precision gears
One of our specialties is bevel gears for helicopters, especially those with angles other than 90 degrees. We have established ourselves as absolute specialists in this field.
NVH (noise, vibration, harshness) is of great importance to the automotive industry. We have also developed special expertise in this area, particularly in the optimization of vibration behavior and microgeometry. We carefully examine these aspects on our own test stands.
This variety of technologies and our in-depth understanding of each individual process step enable us to manufacture even the most complex drive systems to the highest quality.
This broad range of technologies certainly places high demands on your team. Can you elaborate on how you master this challenge?
Our team is undoubtedly our most valuable asset. We may have state-of-the-art machines, but it is our excellently trained employees who bring this technology to life and exploit its full potential. We attach great importance to the training of our junior staff. Every year, we take on two to four apprentices and offer them the opportunity to complete their A-levels in addition to in-depth vocational training. These young specialists are our future – many of them develop into our future managers and team leaders.
The true strength of our 100-strong team lies in the combination of comprehensive training, the great skills of each individual and perfect teamwork. I like to compare our team to special forces – each individual is highly qualified, but the real strength comes from working together. This mixture of specialist knowledge, experience and team spirit enables us to master even complex challenges and develop innovative solutions. Our employees are not only experts in their respective fields, but also understand the interrelationships in the overall process. This is what makes us special and enables us to deliver top performance.
Let’s talk about your EMAG machine. Why did you decide to manufacture small series and frequently changing components on a pick-up vertical turning machine rather than a classic horizontal machine?
The decision for the EMAG machine was based on several decisive factors. The main reason was that we needed a solution for the automated machining of heavier workpieces with the highest accuracy and reliability.
The vertical design of the EMAG VL 6 offers us decisive advantages here. Despite frequent retooling – we change the workpieces to be produced several times a week – we are very satisfied with the consistently high dimensional accuracy. This is particularly important for our precision parts. Another important aspect is the wide range of machining options. We make intensive use of both hard turning and integrated milling operations. This multifunctionality enables us to machine complex components in a single setup, which increases accuracy and shortens cycle times.
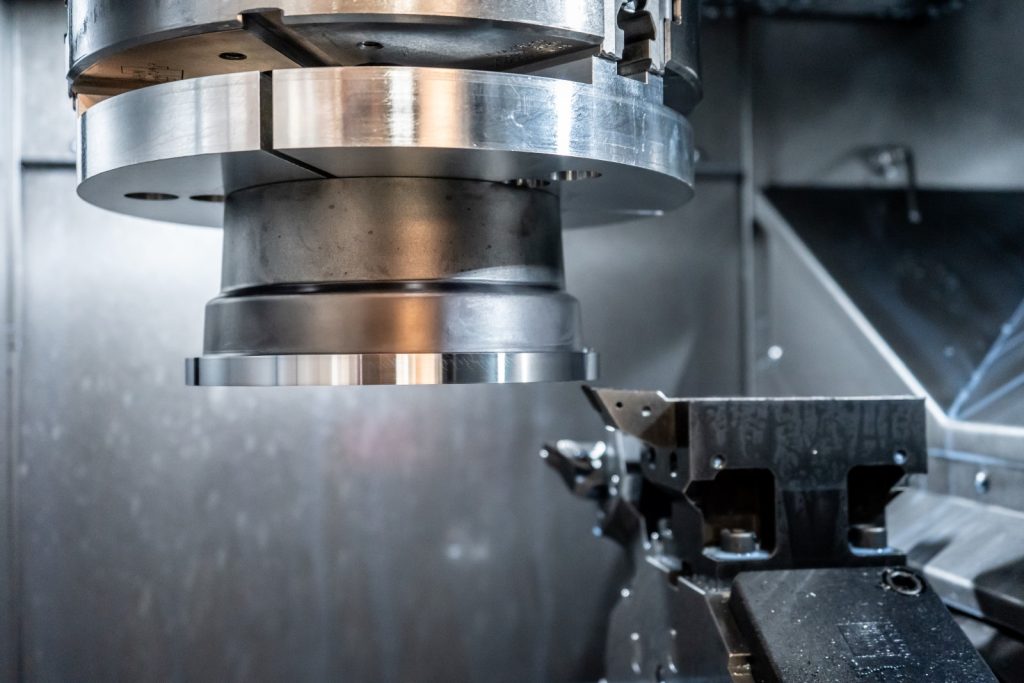
Vertical work area of the EMAG VL 6 lathe with clamped gearbox housing during machining.
Ultimately, we were convinced by the combination of the complexity of the machining options, the achievable accuracy, the high availability of the machine and, last but not least, the excellent service from EMAG. This machine fits perfectly with our requirements for flexibility and precision in small series production.
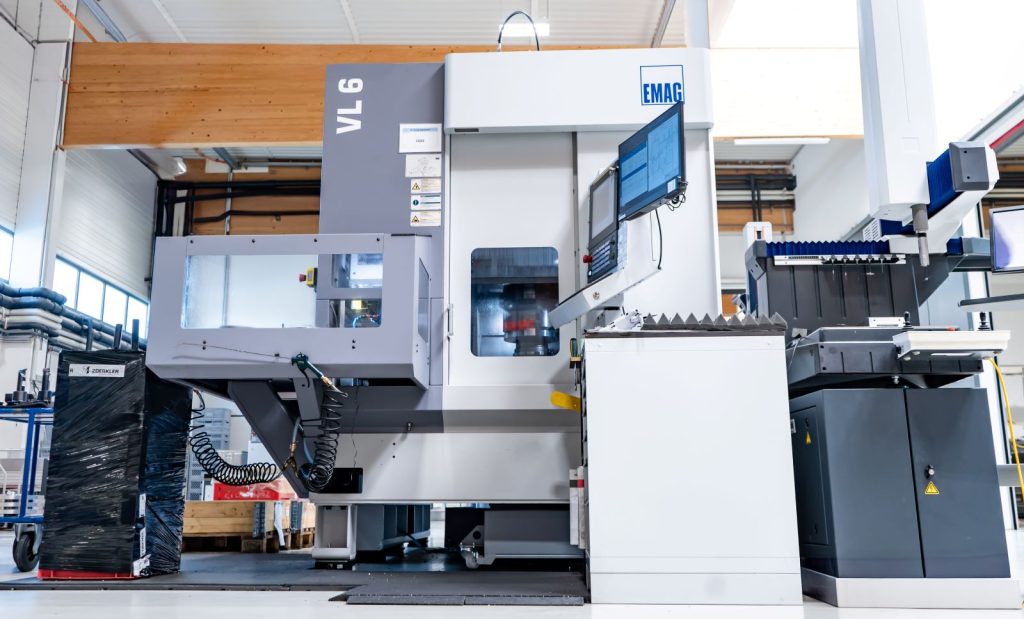
Modern production hall with the VL 6 vertical pick-up turning machine from EMAG at Zoerkler.
What influence does the automation system from EMAG have on your production processes?
The influence of the automation system is considerable, but it is important to emphasize that it only develops its full effect in combination with the outstanding dimensional accuracy and quality of the entire system.
A specific example: We use the option of frequently running the machine autonomously in the second and third shifts. This would not be possible without the extraordinary stability and precision of the system. The combination of reliable automation and constant precision enables us to produce efficiently around the clock without having to compromise on quality. This is invaluable to us. It not only increases our productivity, but also gives us the flexibility to react quickly and efficiently to changing order situations.
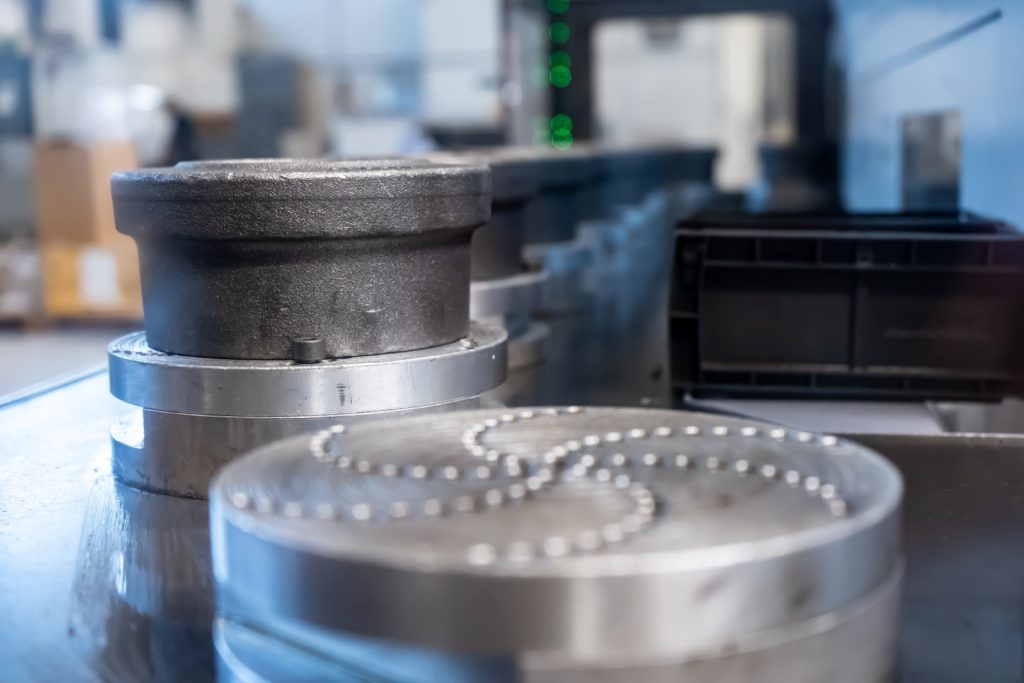
Automation conveyor of the EMAG VL 6 with several workpieces in a row for automated machining. The belt transports the workpieces to the pick-up station, enabling a continuous and efficient production flow.
Quality assurance is undoubtedly a critical aspect, especially for your aviation contracts with their strict documentation requirements. How do you ensure that you meet these high standards?
Quality assurance is our top priority. We have implemented a sophisticated QA system that covers all areas of our production. Especially for the EMAG machine, we have installed a high-precision measuring machine right next to the system. This enables continuous intermediate checks during the production process. All measurement results are automatically recorded and documented electronically to ensure complete traceability.
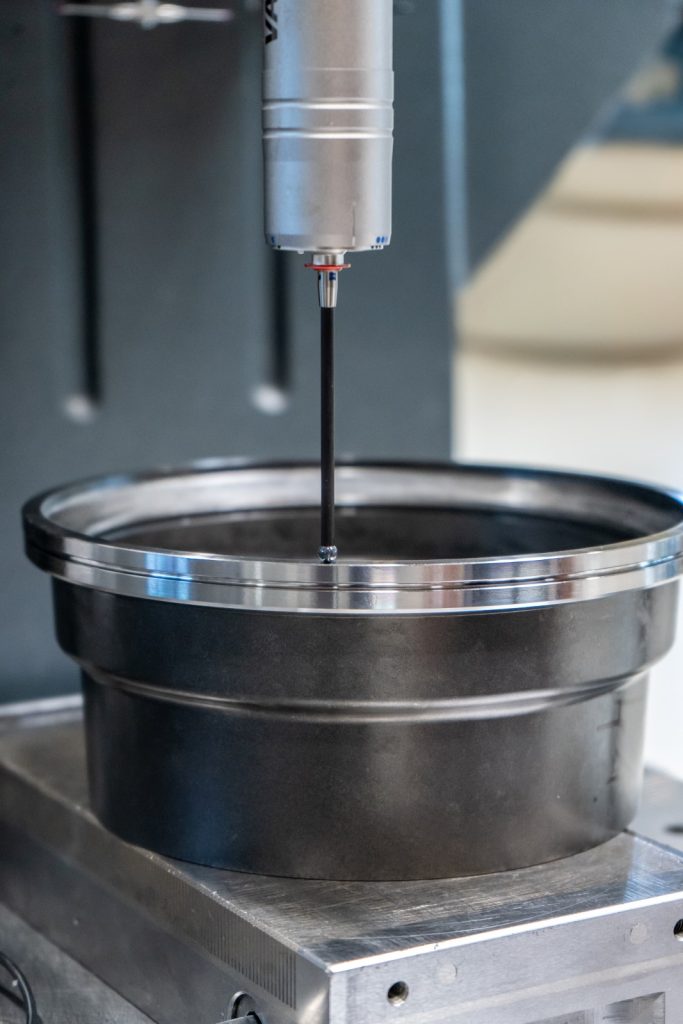
Quality control of a gearbox housing with state-of-the-art measuring technology.
However, our quality assurance system goes far beyond this. We take an integrated approach in which each part is managed in a batch-related manner. For each batch, we create a comprehensive documentation report that shows the entire production history – from the origin of the raw material to each individual processing step.
Complete documentation of all processes is particularly important for the aviation industry. This includes not only technical data, but also information about the employees involved and the technologies used. This data is “frozen”, so to speak, and archived to ensure complete traceability at all times. This comprehensive approach to quality assurance and documentation is not only a necessity in the aviation industry, but also an essential part of our corporate philosophy. It enables us to deliver consistently high-quality products and justify the trust of our customers.
The change from horizontal to vertical construction for the VL 6 was certainly a major adjustment. How did your employees deal with this change of concept?
Switching to the vertical design of the VL 6 was indeed a big change, but I’m proud of how well our team has met this challenge. The advantages of the vertical design, especially in combination with the automation and the pick-up system, were obvious to us. We achieve significantly higher accuracies when clamping and turning the workpieces, which contributes directly to the quality of our products.
As far as the changeover for our employees was concerned, I had full confidence in their ability and adaptability. The 90-degree turn in the machining logic was a challenge at first, but our technicians and engineers mastered it with enthusiasm and professionalism and with the support of the EMAG technicians. We accompanied the changeover with extensive training courses and a gradual introduction. This allowed our employees to familiarize themselves with the new concept and contribute their experience to the implementation.
In practice, it turned out that my trust in our team was fully justified. Not only did they quickly get used to the new technology, they also found innovative ways to fully exploit the machine’s potential. Today, our employees work with the vertical machine just as naturally and efficiently as before with the horizontal machines. This successful transition once again underlines the expertise and flexibility of our team – qualities that are invaluable in our fast-moving and technology-driven industry.
One fascinating aspect of your company that we haven’t talked about in detail is your test stands. Can you tell us more about them?
With pleasure. Our test stands are indeed an essential part of our range of services and an important factor in our success. We have a wide range of ultra-modern test facilities that enable us to test our products under realistic and often extreme conditions.
One highlight is our high-performance helicopter gearbox test stand. It can handle outputs of up to 2 x 4 megawatts, motor speeds of up to 26,000 revolutions per minute and torques of up to 180,000 newton meters. This enables us to carry out even the most demanding certification tests for helicopter gearboxes.
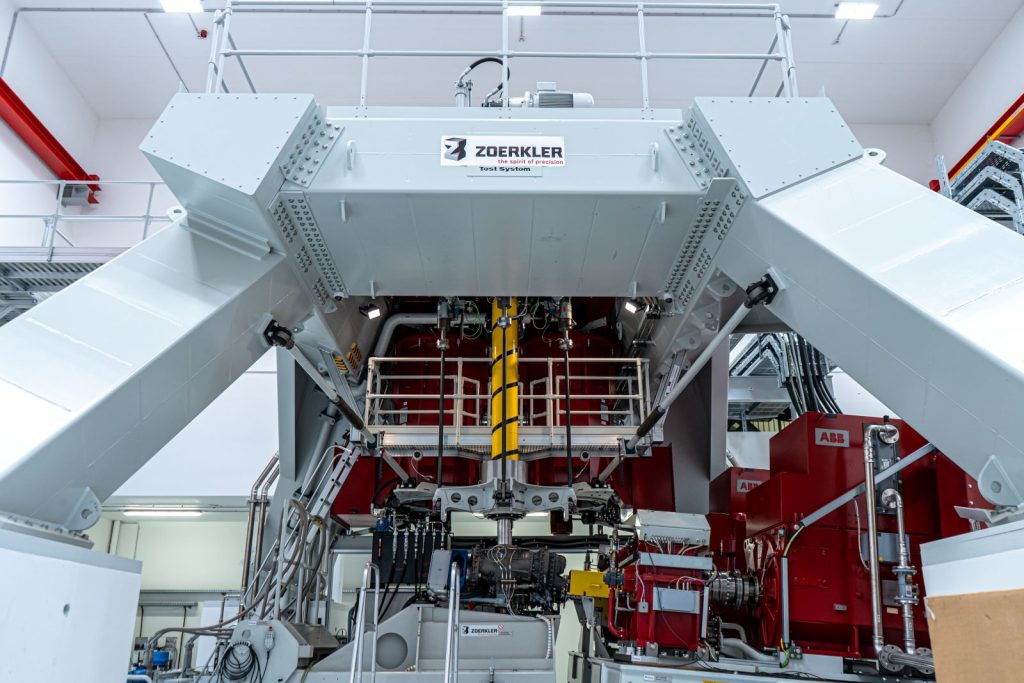
Power under control: the impressive helicopter gearbox test stand from Zoerkler.
In the field of electromobility, we have developed special test stands with battery simulation. This enables us to test e-drives both electrically via the inverter and mechanically. A particular focus here is on NVH analyses (noise, vibration, harshness), which are crucial for the driving comfort and efficiency of electric vehicles.
We offer comprehensive services for the automotive industry, ranging from complete series development to the testing of transmissions and electric drives. We also provide advisory services, especially when it comes to optimizing transmissions. A typical scenario is, for example, the elimination of noise problems at certain motor speeds. Here, we use highly sensitive vibration and noise sensors to carry out a precise analysis and, based on this, the gearbox optimization.
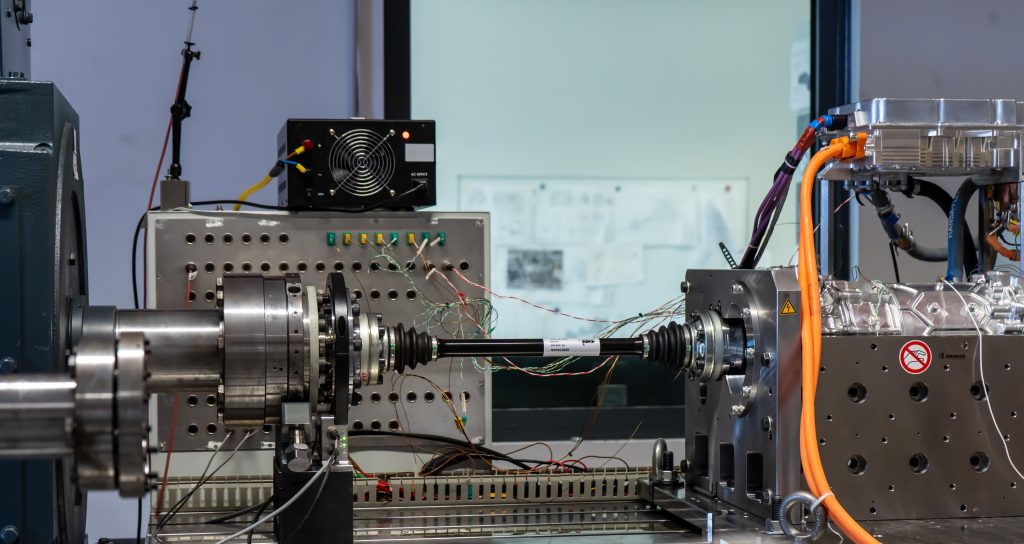
Test stand for electric drives with battery simulation and measurement technology.
These test stands are not only an important tool for quality assurance, but also an essential part of our development process. They enable us to develop and validate innovative solutions before they go into series production. This not only reduces risks, but also speeds up the development process considerably.
Finally, I would like to take a look into the future. Where do you see Zoerkler as a company in the next few years? What strategic goals are you pursuing?
Our vision for the future is clear and ambitious: we want to establish the Zoerkler brand as one of the leading names in the automotive and aviation industry. In concrete terms, this means that we want to play an even more important role in future development projects in key sectors such as helicopters, jets and supercars. We see ourselves as a driver of innovation and want to further expand our position as a preferred partner for highly complex drive solutions.
An important aspect of our strategy is continuous investment in research and development. We keep a close eye on trends such as electrification, autonomous flying and new materials and are working to further expand our expertise in these areas.
Sustainability is another key issue for us. We are working hard to make our products and processes even more environmentally friendly without compromising on performance. We see this not only as an ethical obligation, but also as a competitive advantage in an increasingly environmentally conscious market.
Last but not least, we will continue to focus on our most important asset: our employees. We will continue to invest in the training and development of our employees and create a working environment that promotes innovation and top performance.
Our aim is to further strengthen our position as a technology leader and reliable partner in our core markets and at the same time open up new markets. We are convinced that with our know-how, our innovative strength and our dedicated team, we are ideally equipped to meet these challenges. We are delighted to have found in EMAG a reliable partner for our ambitious future goals.