High-strength materials, complex geometries, large unit volumes—the production of turbocharger shafts is one of the most challenging tasks in automotive manufacturing. With its new turn-key production system, EMAG has developed a holistic and complete solution. How exactly does it work?
Things get hot inside a car’s turbocharger: The engine’s exhaust stream flows through this key engine component and drives an extremely fast-rotating turbine wheel, which in turn is connected to a second wheel through a shaft. This wheel presses the compressed fresh air into the combustion chambers. The more air that ends up in the combustion chamber in this way, the more oxygen molecules are connected to the hydrocarbon molecules during combustion—and this is precisely what provides more power. But in the end, “more air” means that the turbine shaft rotates even faster and must withstand increasing workloads. These basic requirements are what make the production of these shafts one of the most challenging tasks in automotive manufacturing, because they are manufactured with high precision from high-performance materials such as Inconel. Considering the general downsizing trend in the automotive industry, turbochargers are becoming even more important. You can read up on it here on the EMAG blog.
EMAG: Knowledge from a Single Source
The question this raises for the automotive industry has become a classic: How can you produce a complex shaft from a high-strength material in high volumes as efficiently as possible—and, of course, do all of that free of error? “Our extensive expertise is a critical when it comes to answering this question,” says Markus Neubauer, Technical Application Engineer at EMAG. “Our broad range of technologies enables us to cover the entire process chain from pre-machining all the way to finishing, including balancing. We are therefore able to develop a comprehensive line solution for this task—including planning, project management, execution and servicing all provided by a single source. This simplifies the entire planning and after-sales process for our customers.“
Reaching “Final Quality” in just Five Operations
A quick glance at the sophisticated production system clearly shows how great an advantage this really is: It contains a total of five operations that are all performed with EMAG machines. It immediately starts at a high pace, since the shaft is pre-turned in a four-axis machining operation performed on the VTC 100-4 vertical turning center. This guarantees lower processing times. Although this example shows a different component, this impressive video clearly demonstrates the precision and stability with which the high-speed process runs on the machine. Once the pre-turning operation is complete, the turbocharger shaft ends up on a conveyor belt. A robot picks it up from there and transfers it for heat treatment in a MIND-L 1000 from EMAG eldec, which very quickly and precisely heats the component to a specific temperature to relieve any possible stresses. The bearing seats of the turbocharger shaft could also be hardened with this machine. The induction technology from EMAG eldec guarantees extremely fast, economic and precise processes in every case.

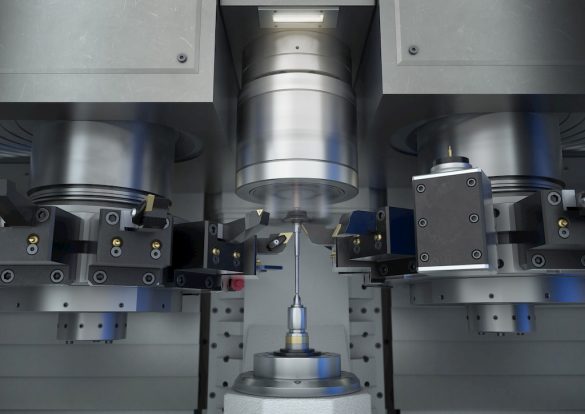
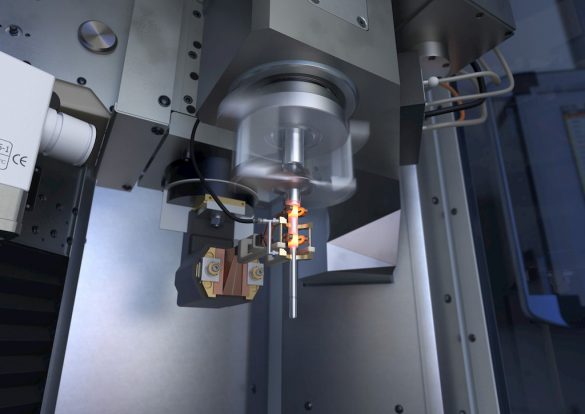
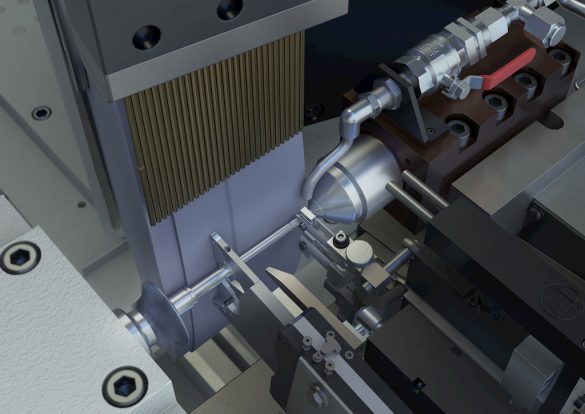
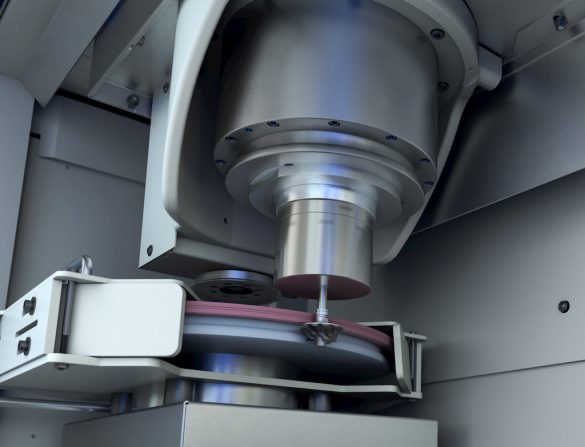
Using Electro-Chemical Machining for Balancing
Various grinding operations then make up the third and fourth operations in EMAG’s line solution: These start with an HG 204 with a horizontal grinding operation on the shaft (including shoulders). Next, the VLC 200 GT vertical grinding machine finishes the ring grooves and the outer wing contour of the turbine wheel. Optionally, the wing contour can also be deburred in the machining area of the VLC 200 GT using a driven brush. After the subsequent washing and measuring process, the line ends with chip-free electro-chemical machining (ECM). Balancing is performed on a CS machine from EMAG ECM. It is completed with a single repeat step and minimum tool wear. How this technology works is shown in this video.
Cycle Time of Only 50 Seconds
Five operations from pre-turning and induction heat treatment to grinding all the way to electro-chemical balancing—EMAG’s linked production system handles the entire finish-machining of turbocharger shafts from start to end. A component leaves the line every 50 seconds in “finish quality.” With three-shift operation, this results in an output of 420,000 to 450,000 turbine rotors per year. Given these performance values, many production planners are thrilled with this solution. After all, considering the continued trend to downsize in the automotive industry, turbocharger shafts are even more important. “Our advantage to the market comes from the fact that we are able to guarantee a customized system architecture for this and similar projects,” concludes Markus Neubauer. “Knowledge from a single source is what guarantees our success and gives us a convincing edge on the market.”
EMAG Systems as a Full-Service Provider
Comparable EMAG production systems can be implemented to manufacture a large number of transmission, engine and chassis components. The new EMAG Systems is a full service provider and can assist with the planning, simulation and execution of manufacturing lines.