How can commonly mass-produced transmission components, such as planetary gears be produced even more efficiently? The EMAG Group provides a customized answer to this question with the development of the twin-spindle pick-up turning center, VL 1 TWIN. It machines two identical components simultaneously in the same machining area. This technology opens up a wide range of possibilities: When two machines are combined in a line, the planetary gear can be machined from two sides—and all that is completed with shorter cycle times. What exactly does the line solution for planetary gears look like?
Planetary Gear: Two Finished Parts Every 20 Seconds
What exactly does a VL 1 TWIN line solution for the soft machining of planetary gears look like? The process is generally run on two machines that are connected to each other via a TrackMotion automation system. The associated TransLift (a lifting and rotating carriage with an electric gripper) simultaneously picks up two raw parts from the feeding conveyor and transports them to the first machine. The VL 1 TWIN’s two pick-up spindles then take over and place the components into the machining area. The turning operation then follows on the first side of the inside and outside diameters (OP 10 – OP 10). The diameter and length (X/Z directions) of both workpieces can be readjusted independently of each other, since the headstocks can traverse autonomously. This is particularly important after a tool change to compensate for deviations (e.g. after replacing the indexable inserts).
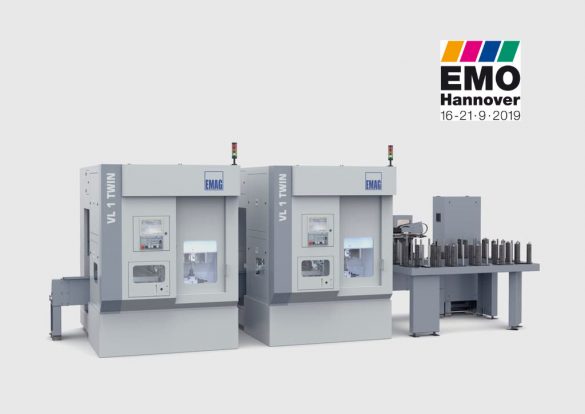
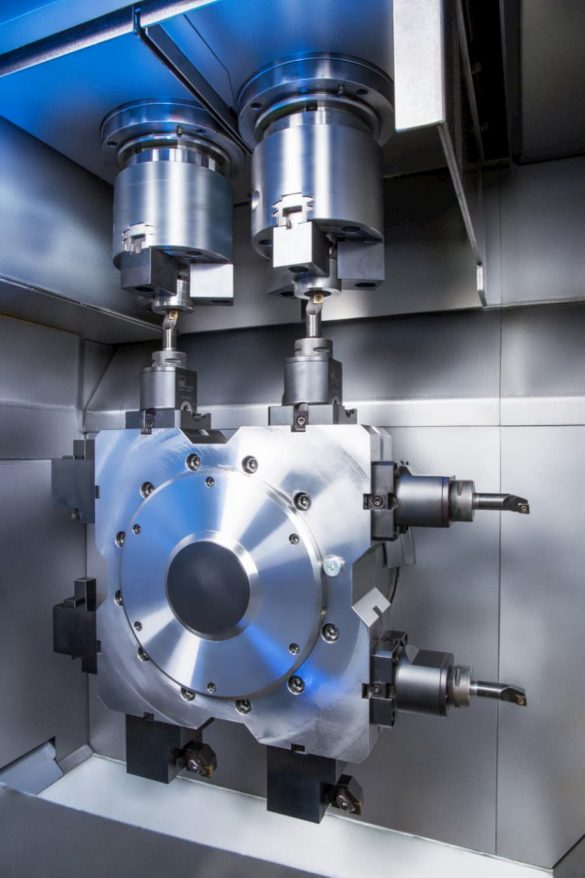
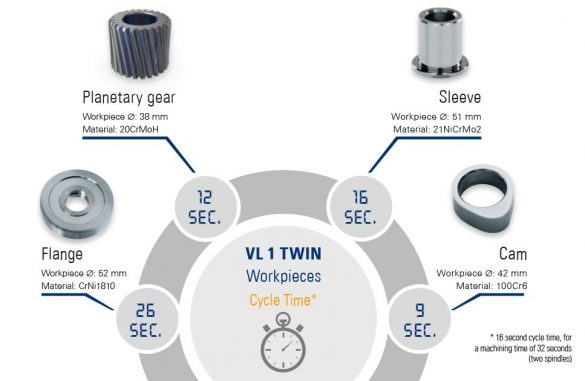
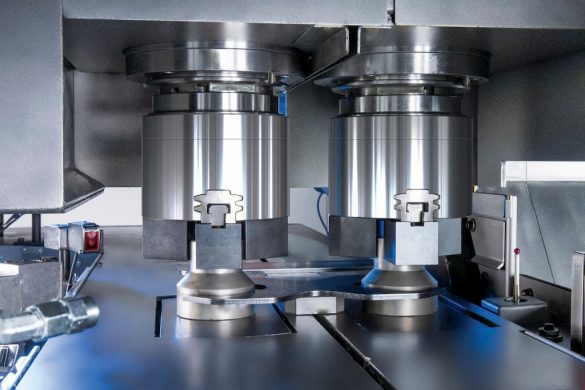
Once the two semi-finished components have been transported out of the machine compartment, the TransLift takes over again to turn them by 180 degrees and transport them to the second VL 1 TWIN. This is where the second side of the outside diameter is turned on its face (OP 20 – OP 20). The TrackMotion automation system then finally places the finished component on the conveyor belt, which can hold up to 400 finished parts on the integrated stacker units. The overall process is completed within a cycle time of about 20 seconds for two components. The average chip-to-chip time is just under 5 seconds. This tremendous pace is made possible by a series of technical configuration details: The two pick-up spindles feature high power values of 9.9 kW (13 hp) and 136 Nm (100 ft-lbs) at 40% duty cycle.
At the same time, the wear-free linear drive in the X-axis (in combination with the direct distance measuring systems) has a high acceleration of 8 m/s2 (26 ft/s2) -including long-term accuracy. This allows for controlled manufacturing of the frequently required H6 fits of the main drill hole.
Perfect Solution for Transmission Production
Overall, the TWIN approach allows for enormous increases in productivity for a whole series of components—from cam elements to bearing rings all the way to flanges. Depending on the requirements, we can also create multi-technology production lines that include EMAG hobbing and deburring machines, for instance.
The VL 1 TWIN live at the EMO 2019
Visit EMAG at the EMO 2019 in hall 17, at booth C29 and see first-hand the benefits of the VL 1 TWIN’s performance.