Fans are used in a number of production processes—they play a key role, for example, in extracting gases, cooling down materials or transporting solids at the heart of ventilation systems. Elektror airsystems, headquartered in Ostfildern, Germany, and with two production sites in Waghäusel (Germany) and Chorzów (Poland), is one of the international leaders in the manufacturing of industrial fans and side channel compressors. About 60,000 devices are produced here every year. For the production of its electric motors, used in a variety of fans, the Waghäusel site has been relying on UNI HEAT from EMAG eldec since May 2018: The system ensures precise induction heating of the empty stator housing before the joining process. An interview with Roland Sand, Head of the Production team at Elektror airsystems, about choosing the right supplier, the collaboration with EMAG eldec and the meaning of process reliability follows below:
Mr. Sand, how would you quickly outline Elektror airsystems’ expertise?
As a manufacturer of industrial fans and side channel compressors, we deliver everything from a single source—from customer-specific standalone solutions to serial devices. This allows us to manufacture the right industrial fan for nearly any application. That is why these devices are found in just about all sectors of industry and manufacturing. Customer-specific design is one of our strengths. Therefore, our production must be flexible, to quickly adjust to changing batches.
What is the role of induction heating for this?
It is used to manufacture the electric motors that drive our fans and side channel compressors. Specifically, the goal here is, as we say, to “marry” the empty stator housing and the motor winding. To achieve this, the housing is first heated to a temperature of 280 to 300 degrees Celsius. This causes it to expand and allows for the motor winding to be inserted. Once they have cooled down, both components establish a form-fitting and solid bond. This joining process has existed for a long time in our production. However, the former induction heating system was in need of improvement. Among the issues was that it did not indicate the component’s actual temperature after heating. This then led to extended throughput times when joining the empty stator housing and the motor winding. One of our main goals, therefore, was to improve this process and make it more reliable.
Why did you choose a solution from EMAG eldec?
It all started out with an Internet search. I gathered information beforehand about potential suppliers that have the required expertise and proximity to Waghäusel, because the issue of “fast service” was very important to us. In a second step, we visited the EMAG eldec site in Dornstetten and talked the project through. In the end, it was EMAG eldec’s extensive experience with induction turn-key solutions that convinced us.
How did the subsequent UNI HEAT development process take place?
The collaboration was very cooperative. Many details regarding the control unit, safety, and the design of the new comprehensive solution were worked out with us—this also includes a modified induction heating process, for example. To some extent, this process is now performed backwards, because an induction rod is plunged into the hollow component—before, a ring inductor, which enclosed the component from outside, was used. The new solution ensures precise heating results.
How is process reliability now guaranteed?
For one, the entire process is very lean and the machine’s control unit very simple. First, the operator places the empty housing in the custom-fit workpiece carrier and pushes it inside the UNI HEAT. As soon as he closes the front door, the first mechanical processes are initiated in the machine: The component is lifted and encompasses the inductor when it reaches its processing position. The actual induction heating then only lasts 30 to 120 seconds depending on the size of the housing. Once it is completed, a warning light signals to the operator that the component can be removed. The actual component temperature is continuously shown on the operator panel.
What happens then?
The operator places the hot housing on a mold, which is ready at the cooling location. He pushes the motor winding from the top into the housing. That’s it. After about two minutes, the component has cooled down and can be placed on a conveyor belt.
Does the machine undergo many retooling processes?
Yes, this is an important issue, because the motors we produce are a variety of sizes and sometimes the batches change several times a day. That’s why we must keep retooling the UNI HEAT, although this doesn’t take more than about a minute: The operator loosens two screws on the inductor mount, removes the inductor and puts on a new one—we have a total of six different inductors for the various empty housings. The workpiece carrier is simply set down and can be changed easily in a few seconds. Then, you change the program on the operator panel in just a few clicks. That’s it. Various safety features prevent operator errors.
What impression do you get from this solution now that it has been in operation for nearly one year?
We’re very satisfied. After all, in Waghäusel, we produce about 250 motors a day—and for each model the empty stator housing runs through the induction heating process. Despite these unit volumes and the frequent batch changes, there are no issues or defective parts. Moreover, the EMAG eldec service team quickly rectified minor startup problems. The company is only 120 kilometers away. We’re entirely satisfied with our decision to choose this induction heating system.
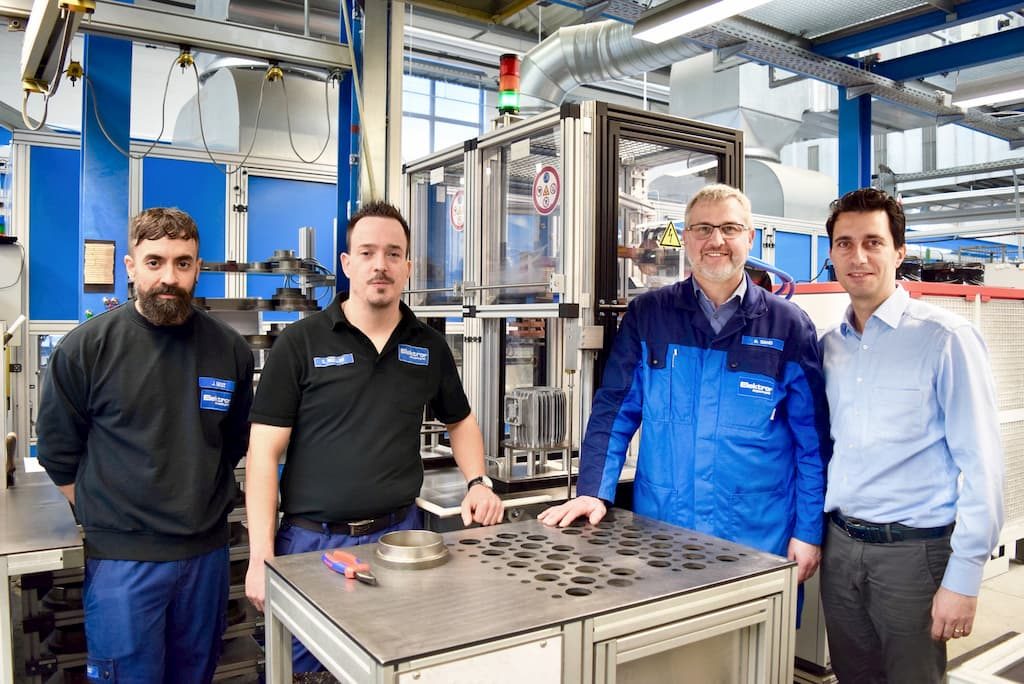
Interviewee Roland Sand, Head of Production team at Elektror (2nd from left), together with Steffen Müller and John Best from Elektror (1st and 3rd from left) as well as Pasquale Di Santi from EMAG eldec.