Mack Rides roller coasters can be found all over the world. The company based in Waldkirch near Freiburg is a global player in the amusement industry and produces complete solutions in-house, including rails, vehicles, decorations, animations and much more. On board for the rail production: induction technology from EMAG eldec. It ensures precise heat treatment prior to final alignment of the components. A conversation with Marcel Martinetz, head of equipment design, about the special know-how of his company and the associated production solutions.
High Requirements in Roller Coaster Engineering
Mr. Martinez, what is special about Mack Rides?
First of all, we very intensively tailor our products to the requirements of our customers. With roller coasters, there are no “twins.” Each solution is different, especially since we handle everything, from engineering to rail and vehicle production, animation, final assembly and installation, ourselves. Another aspect of note is that the family that owns Mack Rides also operates roller coasters at the Europa-Park in Rust. Here, customers can see and test various models at a single location.
What does that mean for production?
Roller coasters are manufactured individually. The production quantities for the respective components, therefore, tend to be small. At the same time, we maintain very high technical standards. For this reason, we choose to keep our manufacturing largely in-house. This enables us to not only ensure that the technical details are perfect, but also to efficiently and quickly implement the wishes of the customers. We have a large range of machinery that intelligently combines robotic solutions, CNC technology and manufacturing applications. When new production solutions are needed, we always have a very clear idea of what we are looking for. This is why it is important to us that the machine manufacturer shares our very goal-oriented philosophy, work approach and lean processes.
How did the current cooperation with EMAG eldec come about?
In the production of roller coaster rails, extreme precision is vital. The rails are up to around 12 meters long. Nevertheless, across all their twists and turns, they may not deviate more than 3 mm in the length or more than 2 mm in the track gauge. To safeguard this, we have a two-step process. After we bend the rails, we place them in a jig and measure them with a laser. Here, we can detect any non-conformance immediately and correct it with a special robotic clamping solution. First, though, this requires heating of the rails at defined points. In the past, we used a naked acetylene flame. However, that increased the risk involved in this work. Furthermore, the flame only applied the heat on the surface. This means that more force was needed to correct the pipe. Then induction heating caught our attention as an alternative. We already knew the process from another in-house solution.
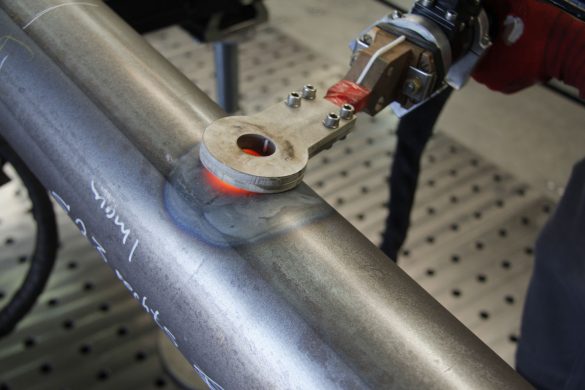
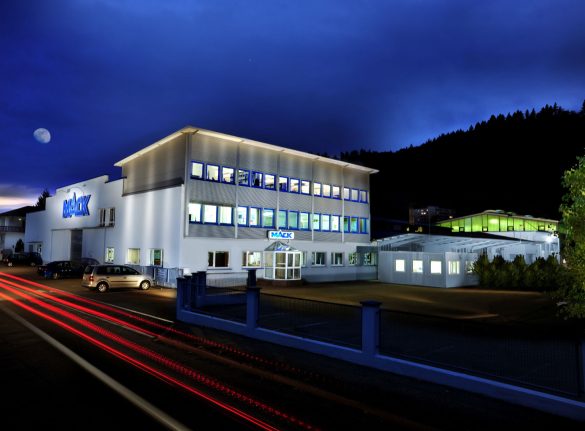
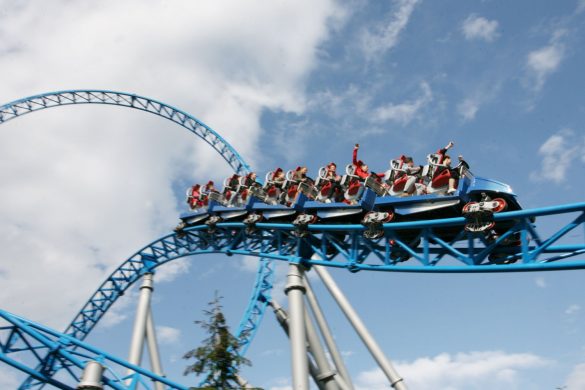
What was important in the implementation of the production solution?
We first tested an alternative induction technology and noticed that it was not easy to reliably implement the process for our specific application. To clarify, the operator must position a ring inductor by hand, maintaining contact with the rail pipe – and this has to be done at various positions. Even slight inattention causes the inductor to lose contact with the pipe. The first solution we tested resulted in overload damage to the generator. We then contacted EMAG eldec to develop a solution that is significantly more robust. Small operator errors cannot be permitted to cause machine failure.
And today, what is your opinion of the completed EMAG eldec solution?
We’re very satisfied. The solution, which includes a handheld ring inductor as well as a 15 kW PICO-SC generator with cooling system, has now been in use for around a year in our production. The process is very stable and it is no longer a problem if the ring inductor loses contact with the rail. All in all, we also benefit from a very fast and easy procedure. The operator starts the respective program via the touchpad interface of the generator and moves the inductor to the component. After a defined period, the desired temperature has been reached and the adjustment can start. Per heat spot, the induction technology is around 30 seconds faster than heating the rail with an acetylene flame.
In your opinion, how did the cooperation with EMAG eldec go?
The whole process was fast and goal-oriented, with EMAG eldec already participating early in the project planning stage. Additionally, we sent a test pipe to eldec’s premises in advance, for experimental analyses with test inductors and generators. Service personnel also assisted us with the initial start-up. All in all, eldec’s philosophy matches our demands. We need partners that are flexible and can quickly implement individual requirements.