Predictive maintenance, increasing output quantities and decreasing error rates – the performance promises of Industry 4.0 are great, although many users still doubt their feasibility: “It’s all a long way off,” as we often hear. At this point, we want to take a very practical look at this topic: At a major German automotive components supplier, IoT experts from EMAG, and their partner companies EXXETA, intuity, and anacision, have optimized a central production process – with amazing results, such as a significant increase in the production capacity of the EMAG line. A conversation with Andreas Kühne, lead data scientist at anacision, about the current successes of the associated EMAG EDNA technology, and how machine builders are comprehensively digitizing their machines.
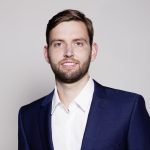
Andreas Kühne, Lead Data Scientist bei anacision
Mr. Kühne, how do you gear up ongoing production for Industry 4.0?
We work with our customers in a highly cooperative way. We started with a workshop in which we identified conceivable use cases. This is where application experts from EMAG, the customer’s users, and IoT experts come together. In the current case study, installing our technology within the first production line was the next step. The whole system consists of the “EDNA IoT CORE” industry PC, the “EDNA NEURON 3DG” acceleration sensors, the “EDNA LIFELINE DASHBOARDS” visualization solution, and the “EDNA CORTEX” software. They form our modular software ecosystem.
And then it goes straight to work?
What we call the “EDNA HEALTH CHECK” for the machines was quickly put to use. Data not relevant to the process is collected and sent to EMAG once a day, and is then evaluated with the help of artificial intelligence. You can think of it like consistently taking a patient’s temperature. In the sample application, we found that unwanted interference frequencies build up. An expert from EMAG then took a look at the whole thing on site and was able to eliminate the problem by optimizing the spindle. The end result is that the machine now runs more smoothly and with greater stability. Therefore, It can be said that mechanical engineering expertise from EMAG and the computational results of artificial intelligence are brought together. This is crucial for success.
What has changed about the customer’s actual process?
We distinguish between three basic approaches: automated data applications for the existing production dashboards, accompanying KPI analyses, and custom-fit analytics solutions. With the help of these, the customer independently develops further investigations.
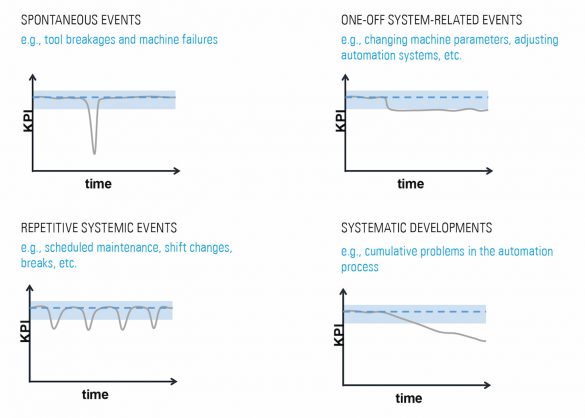
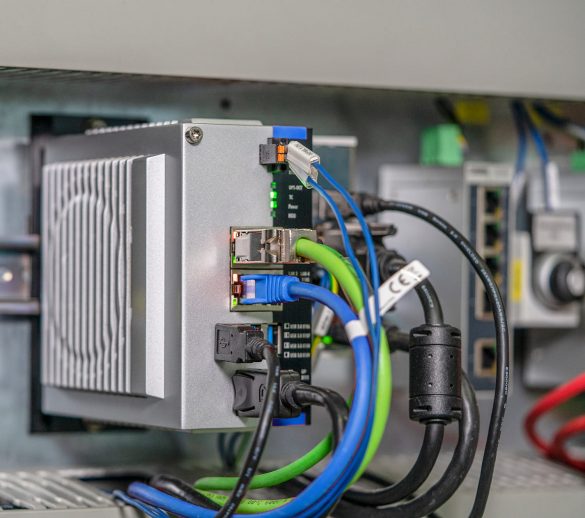
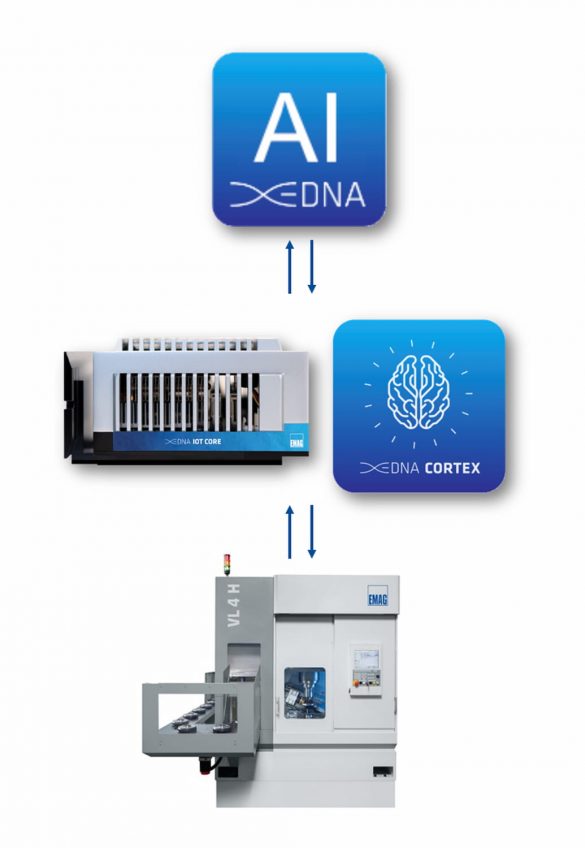
What impact do the production dashboards have on everyday work?
We have had exceptionally positive feedback from the customer. The large dashboards are located in close proximity to the machines and are well received by operators because they simplify work planning with clear information about the status of the machine. To do this, it is necessary to know that we evaluate current machine data and make various predictions on this basis – for example regarding how long the average cycle time is and when a tool change is due. As a result, employees can better manage their breaks. Because of this, it ismuch less common for a machine tool change to be required during the shift break.
What results did the accompanying KPI analyses produce?
We have comprehensively analyzed several months of machine data. The results include detailed information on OEE, cycle times and tool life, the duration of tool changes, the effect of shift changes on the number of pieces produced, and more. This enabled us to see, for example, that the shift changes do not always run smoothly and that the machines are at a standstill for different lengths of time. Subsequently, it was then possible to evaluate the resulting optimization measures.
About the analytics solutions that you have developed for the customer – how should we think about those?
Basically, the idea is that the customer’s decision-makers evaluate and visualize their machine data independently – with the help of a particularly simple programming environment that can also be used by people without advanced knowledge. In the current case, for example, the people responsible at the customer facility checked the effects of reducing the number of specific measuring processes in the machines and shortening their cycle times. It quickly became apparent that such an approach posed no problem and that the component quality remained unchanged at a high level.
What is next?
We are currently working with the partners involved on a proactive notification system. This means that the production lines provide continuous information – for example, via a push message to a smartphone – about various events such as impending downtimes or parallel tool changes on various machines. The message to the Service department could then be, for example: bring forward a tool change to avoid work overload and unnecessary downtimes! In the future we want to detect undesirable anomalies such as impending insert breakage at an early stage. The important thing is for all measures to be coordinated and complement each other. The end result is a continuous increase in the productivity of the machine lines.
–>More details about EMAG EDNA