As a mechanical engineering company, EMAG is making an important contribution to establishing electromobility: The specialists are developing the production technology that can manufacture central components of the electric motor – on a turnkey basis. A new production line for the rotor shaft of electric cars used by a German components supplier illustrates their approach. The solution was delivered at the end of last year. Here we have a conversation with Andreas Bucher, Key Account Manager at EMAG, and Michael Ihring from EMAG Systems about the reasons for this cooperation.
How did EMAG come to work with the customer?
Andreas Bucher: This customer was looking for a highly flexible system including smart automation solutions which we can cover with ourlarge portfolio of machining operations relating to the rotor shaft. They chose EMAG as their mechanical engineering partner because we offer turnkey solutions from a single source.
From your point of view, what was the process like from process design to the start of production?
Andreas Bucher: Very satisfactory. The entire line was developed in close cooperation with the customer, the tool manufacturers, and us. The entire project management was structured at all times. Ultimately, this open-ended cooperation ensured that we were able to work through even critical situations in a goal-oriented manner and that the preproduction launch went ahead as planned.
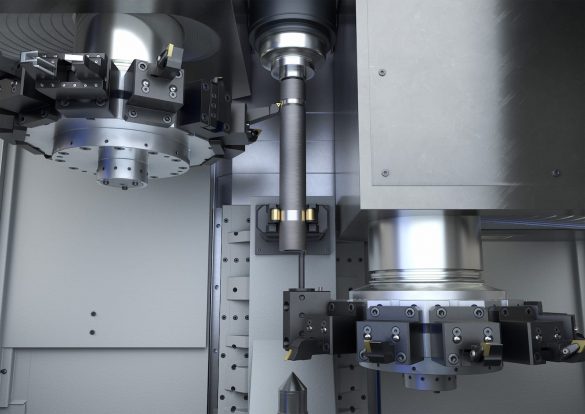
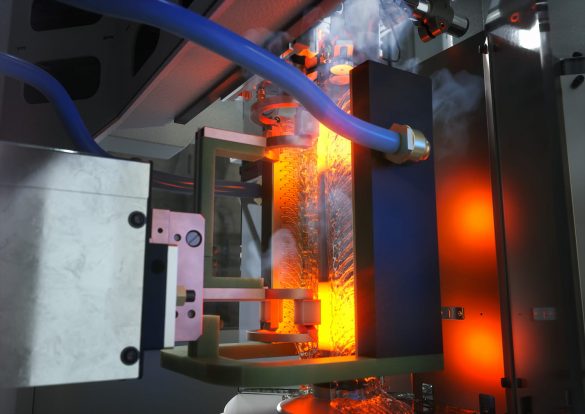
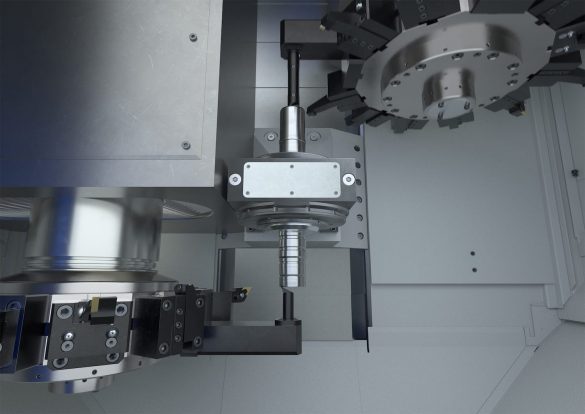
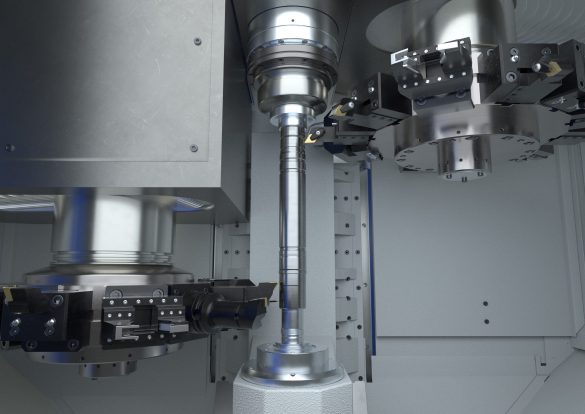
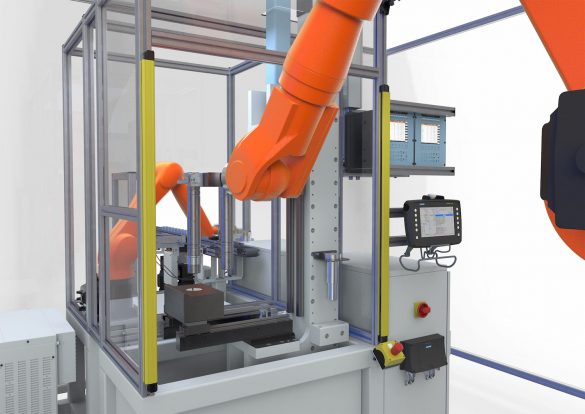
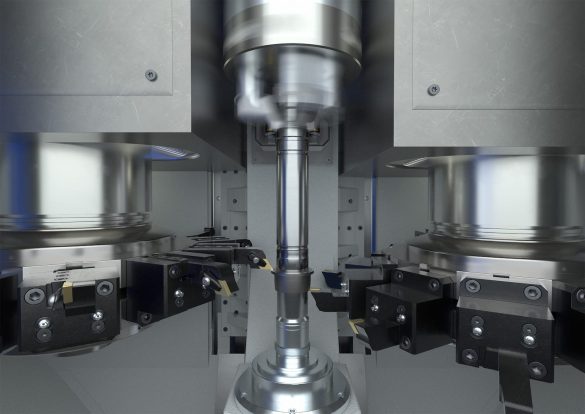
What are the general technical advantages of this solution?
Michael Ihring: All in all, the customer now has a highly flexible system for a large portfolio of machining operations. Twelve main operations and various secondary operations are carried out on the rotor shaft. The individual machines and stations are automated and interlinked using robots, gantry systems, and EMAG’s own TrackMotion system. All processes are very stable, which in turn is reflected in the component quality. At the same time, we benefit from a cell solution that we can expand at any time as our capacity requirements increase. The flexibility is evident in every detail, right down to the automation system.
What practical experience do you have with the machine?
Michael Ihring: The first feedback reports from the customer have been very good. For example, we are seeing perfectly reproducible results. After it was set up last year, there has been no need for action in regards to component quality. It is equally positive that downtimes are rare due to the intelligent tool change strategies. In summary, the customer is in an ideal position.
-> More information about machining rotor shafts you will find here…
-> Watch our webinar about “The Rotor Shaft – Efficient Manufacturing Solutions for an Essential Part in E-Mobility”