There is no “one” big lever that can be used to improve the energy efficiency of machine tools. Instead, it is important to take a holistic view of all energy flows and that is EMAG’s approach, which the specialists apply to every new development as well as to the retrofitting of older machines. In conversation with Konrad Heimbach, Lead Engineer Energy Efficiency, it becomes clear that even relatively simple measures can massively reduce energy consumption.
Mr. Heimbach, how do you reduce the energy consumption of a machine tool?
There is no one right answer to this question, because a machine and its peripheral devices contain a large number of processes – and you can start anywhere. We have defined a total of six areas for greater energy efficiency, which we use as a guide.
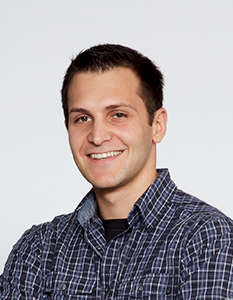
K. Heimbach, Lead Engineer Energy Efficiency
Which topics are these exactly?
The choice of manufacturing process has the greatest influence on energy consumption. This is easy to explain: for example, it makes a big difference whether a component is cast with cavities and holes and then turned or if it is milled “from solid.” I Individual components, energy management, AI-based optimization of the manufacturing process and data-driven production planning are all paramount in selecting the propper machine concept. This is where we always start!
Why does the machine concept play such a big role?
Let’s take the example of “automation”: every workpiece handling process naturally requires energy. Conversely, machines that can be easily integrated into the production flow reduce energy consumption. We achieve this through integrated parts storage and simple loading and unloading options, as an example. Another interesting example is the Duo machine platform, where only one set of peripheral devices is used – two single machines, on the other hand, require two sets, which naturally need more power.
Do you also have specific figures for these and similar savings?
We compared the energy consumption of different processes that were used for the same machining requirements on a component. The resulting energy requirement per machined volume is extremely different. For example, 663 J/mm3 is required for grinding, 220 J/mm3 for hard turning and only 57 J/mm3 for scroll-free turning on the same workpiece. In other words, it is essential to keep the energy requirement in mind when selecting the respective process.
Keyword “retrofit” – how do you know which adjustment screw to turn for more energy efficiency on an older machine?
To do this, we start by creating an energy flow diagram that details the consumption of the drive system, cooling system, hydraulics and lubrication. In this way, we identified the biggest problem areas for a VTC 250 shaft lathe that has been in use at a customer plant for 15 years. In this case, it was the hydraulic unit, cooling lubricant pump and cooling unit. All three units were replaced. The end result is that the user saves around 18,000 kWh per year or 6.7 tons of CO2, whichis more than the annual consumption of two detached houses.
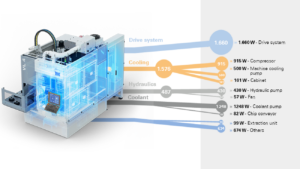
At EMAG, the energy efficiency of a machine is determined using an energy flow diagram.
How long does such an exchange take?
It’s very quick, because the installation takes place directly at the customer’s premises. In this case, everything was done in around one and a half days. Incidentally, the costs incurred on the retrofit are amortized in about 2.5 years, including the state subsidy.
Are there also approaches for holistically optimizing production sites?
For some time now, we have been working with the ETA factory (Energy Technologies and Applications in Production), a dedicated facility and research project at the TU Darmstadt campus in which various industrial partners and companies are involved. In the ETA factory, there are demo process chains in which all production steps are coordinated and closely networked with the production building. Every step of a process is monitored and optimized digitally, in real time and with energy and resource efficiency in mind. The waste heat from the machines is used to heat office buildings, for example. Incidentally, the ETA factory also offers advanced training courses for interested companies.
What role do IoT solutions play in this topic?
They are becoming increasingly important. For example, with IoT we are currently working on using the resulting measurement data to compensate for the warm-up of the machines and thus make it superfluous. This is an important topic because relatively large amounts of energy are consumed in this start-up phase – without any output. The EMAG Energy Monitor is similarly interesting. Users can call up information relating to electricity and compressed air and at the same time establish a reference and form key values such as “energy consumption per shift”, “energy consumption per workpiece” and “energy consumption per non-productive time”. Unusual deviations are immediately apparent and can therefore be rectified more quickly, which ultimately improves the energy balance. Overall, it is safe to say that we are using all known levers for sustainable production, although we are still in the very early stages – the journey continues.
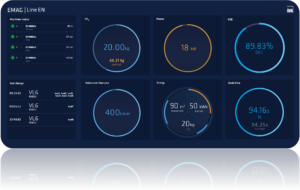
The EMAG Energy Monitor allows users to keep an eye on their machine’s consumption data at all times.